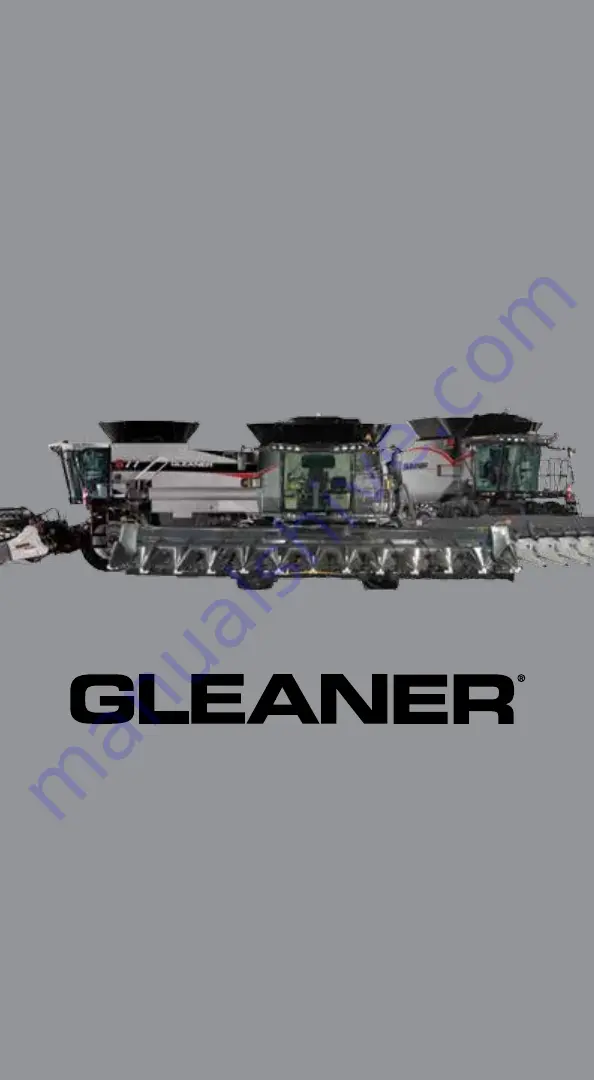
2016 Quick Reference Guide
S67/S68/S96 • S77/S78/S97 • S88/S98 Models
It is YOUR responsibility to read and understand the safety section in your
Operator’s Manual and the manual for all attachments before operating your
machine. Remember YOU are the key to safety. Good safety practices not only
protect you, but also the people around you.
Study the features in your Operator’s Manual and make them a working part
of your safety program. Keep in mind that the safety section in your Operator’s
Manual is written only for this type of machine. Practice all other usual and
customary safe working precautions, and above all REMEMBER - SAFETY IS
YOUR RESPONSIBILITY. YOU CAN PREVENT SERIOUS INJURY OR DEATH.