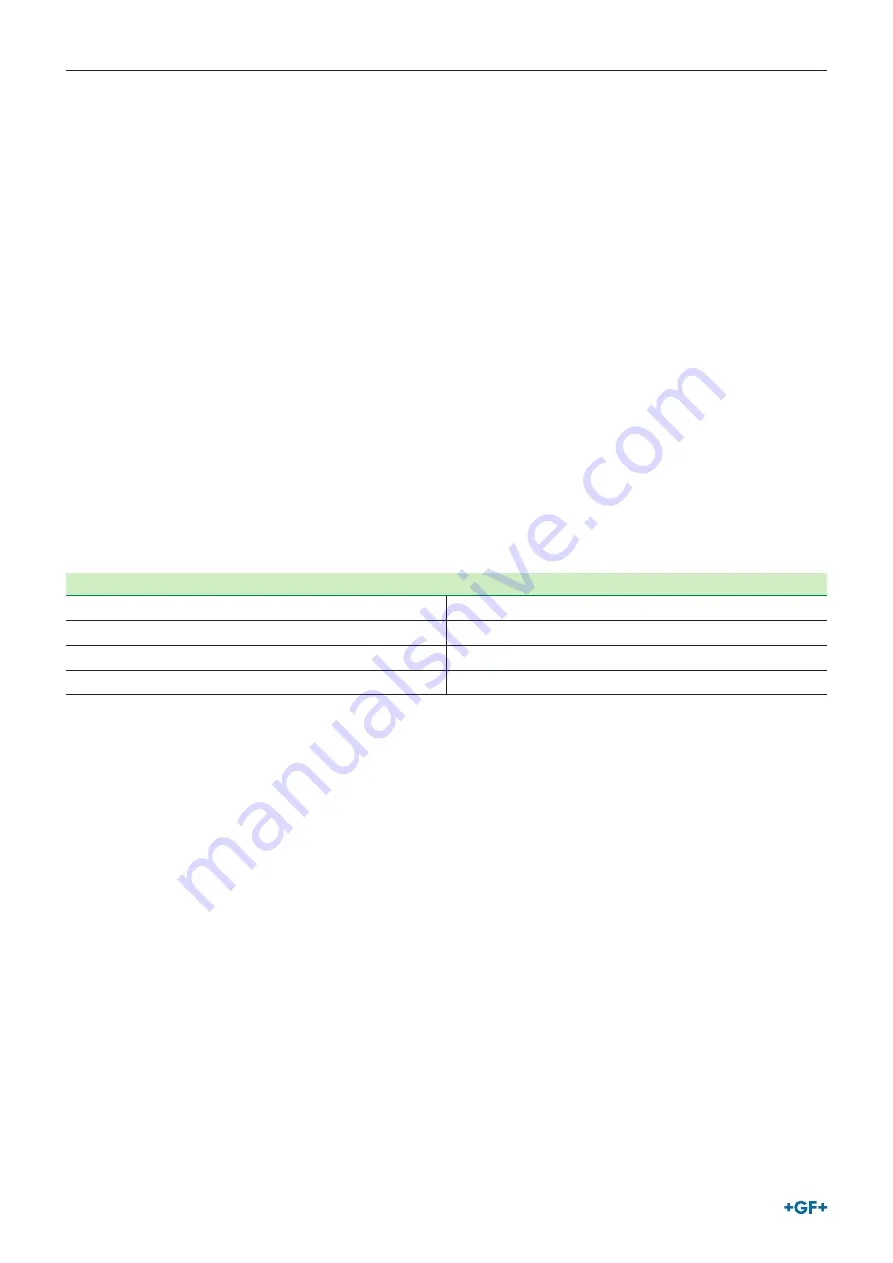
8
Instruction manual
5
Modbus RTU interface description
5.1
Introduction
Modbus is a master-slave system, where the master communicates with one or multiple
slaves. The master typically is a PLC (Programmable Logic Controller), DCS (Distributed Control
System), HMI (Human Machine Interface), RTU (Remote Terminal Unit) or PC.
The Modbus RTU interface board fits into the option slot 1 (X6) of the EA25-250 and EAMT25-
100 baseboards. It supports the Modbus RTU protocol via 2 wire RS-485 serial communication
standard. The Modbus board performs the tasks of RS-485 interface, actuator data conversion
and the issuing of actuator commands. A Modbus RTU master may command an actuator fitted
with the Modbus board to open, stop, close etc. Full list of functions, see chapter Modbus Regis-
ter Map.
You need physical access to the baseboard and Modbus board only for:
•
Installing the Modbus board on the actuators baseboard and wire the RS-485 cables
•
Setting of the termination switch S1 on the Modbus board
•
Resetting the EA baseboard and Modbus board to factory defaults
•
Viewing the diagnosis LEDs on the Modbus board or failure codes on the 7-segment
display located on EA baseboard
All other adjustments to the settings for the Modbus board may be made remotely via the
RS-485 and the Modbus RTU protocol.
5.2
Supported Function Codes
Command
Function code
Read holding/ analog output registers
03
Read input registers (2 Bytes per register)
04
Write single register (2 Bytes)
06
Write multiple registers
16
5.3
Slave Address
The slave address is changeable via Modbus RTU in the Range 1…247 (see 7.2).
Slave address 1 is the default address after factory reset.
Slave address setting 0 is not allowed.