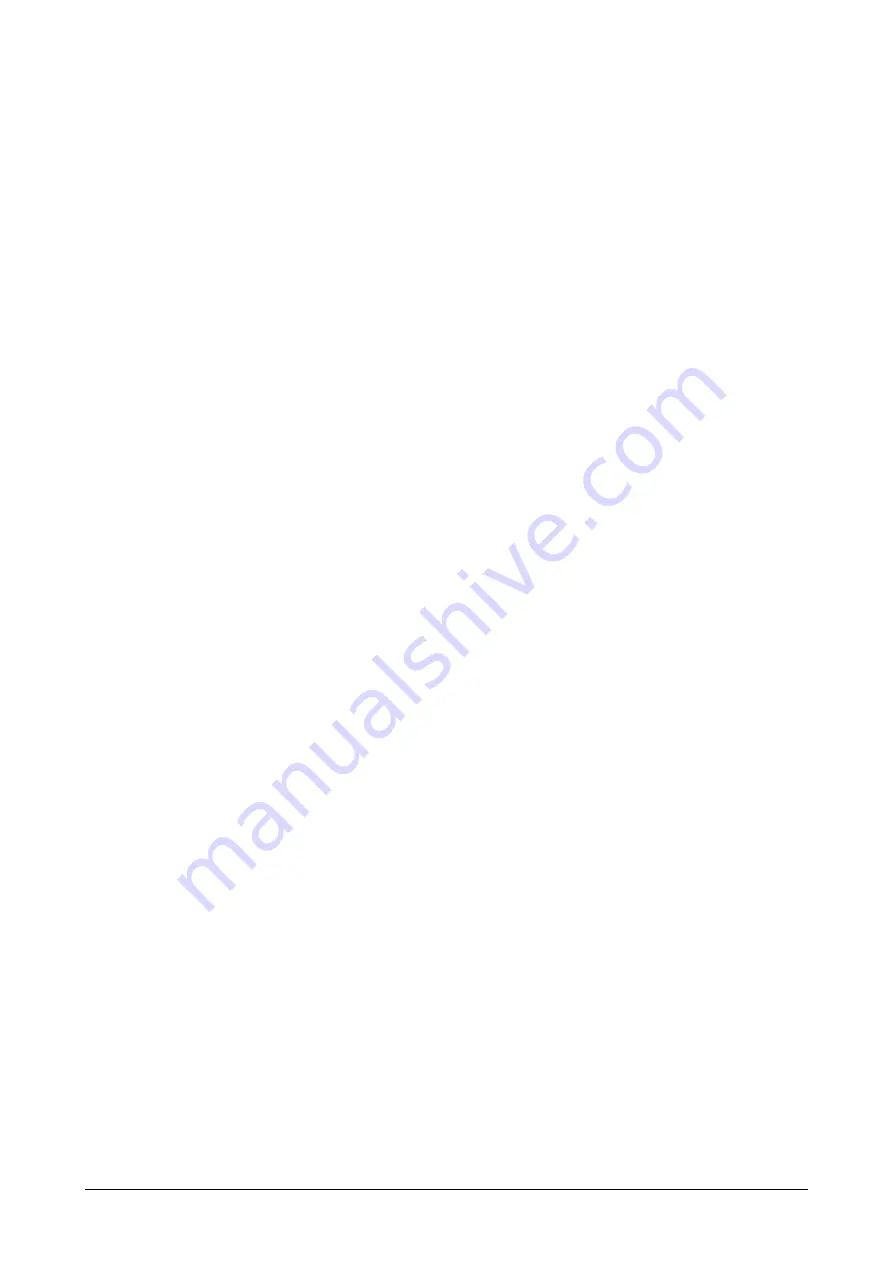
____________________ _
ADL300-EPCv2- User Guide
Page 18 of 64
3.3.4.1 Minimum lift travel limit
The minimum lift travel limit is equal to the minimum limit of the zero cam.
The lift must normally never exceed this limit, although there are some exceptions when special
maintenance operations are required.
Due to these exceptions the control system does not perform any checks or take any action if this limit is
exceeded.
All control procedures and any alarms are thus managed by the external PLC
.
The external PLC must also prevent activation of the zero cycle sequence if the lift car is below the zero
cam. If this rule is not observed the lift car will over-travel into the pit and crash into the floor of the shaft.
3.3.5 SelfStudy command
The Self Study command is used to detect the position of the cams indicating the position of the floors in the
lift shaft. The control system detects these positions automatically, by performing a series of movements.
This command should only be executed when installing the control device or moving the floor identification
cams.
WARNING: before executing the Self Study command, check that the cams are arranged in their
correct positions, especially the deceleration cams. Also check that the size of the deceleration cam
is sufficient to stop the control system. Remember that these sequences start and stop according to
the positions of the cams. Cams that are not in their correct position could cause a collision.
The
Self Study sequence
is as follows:
1. The Self Study sequence is activated on the rising edge of the Self Study command.
2. The ZeroFound variable is set to FALSE; the control system must therefore run a zero cycle sequence.
3. The control system moves the lift, at the ZeroSpd speed, in the negative direction until engaging the
lower limit cam.
4. After engaging the lower limit cam, it continues, at the ZeroFound speed, until engaging cam B of floor
zero. On the upper margin of cam B the control system initialises the encoder 0 position and floor
counter.
5. It continues in the negative direction, at the same speed, until engaging cam A of floor 0. After engaging
cam A it stops.
6. Set SelfStudyOK = FALSE.
7. This resets all the positions of the cams: A Low, B High; reset the adjust parameters: Adj Up and Adj
Dw.
8. The lift moves in the positive direction at the Self Study speed ().
9. While moving the system detects the position of the car at the edges of all the cams it meets, including
the deceleration and qualification cams.
10. Upon engaging the upper deceleration cam, Slow Upper Limit, it reduces the speed to the value set in
ZeroSpd.
11. It continues in the positive direction until engaging cam B of the top floor. Once engaged, it stops.
12. It stores the positions detected.
13. It calculates the position of the lower edge of cams A and B of floor 0. The lift car must not reach these
edges, so the control system assumes that the size of cam A at floor zero is identical to that of cam A at
floor one, and thus calculates the lower edge of cam A as follows:
A Low (floor 0) = A High (floor 0) – ( A High (floor 1) - A Low (floor 1))
The same procedure is used to calculate the lower edge of cam B.
14. It calculates the position of the upper edge of cams A and B of the top floor. The lift car must not reach
these edges, so the control system assumes that the size of cam A at the top floor is identical to that of
cam A at the second-to-last floor, and thus calculates the upper edge of cam A as follows:
A Low (top floor) = A High (top floor) – ( A High (second-to-last floor) - A Low (second-to-last floor))
The same procedure is used to calculate the upper edge of cam B.
15. The lift car is moved into position at the top floor.
16. Set SelfStudyOK = TRUE.