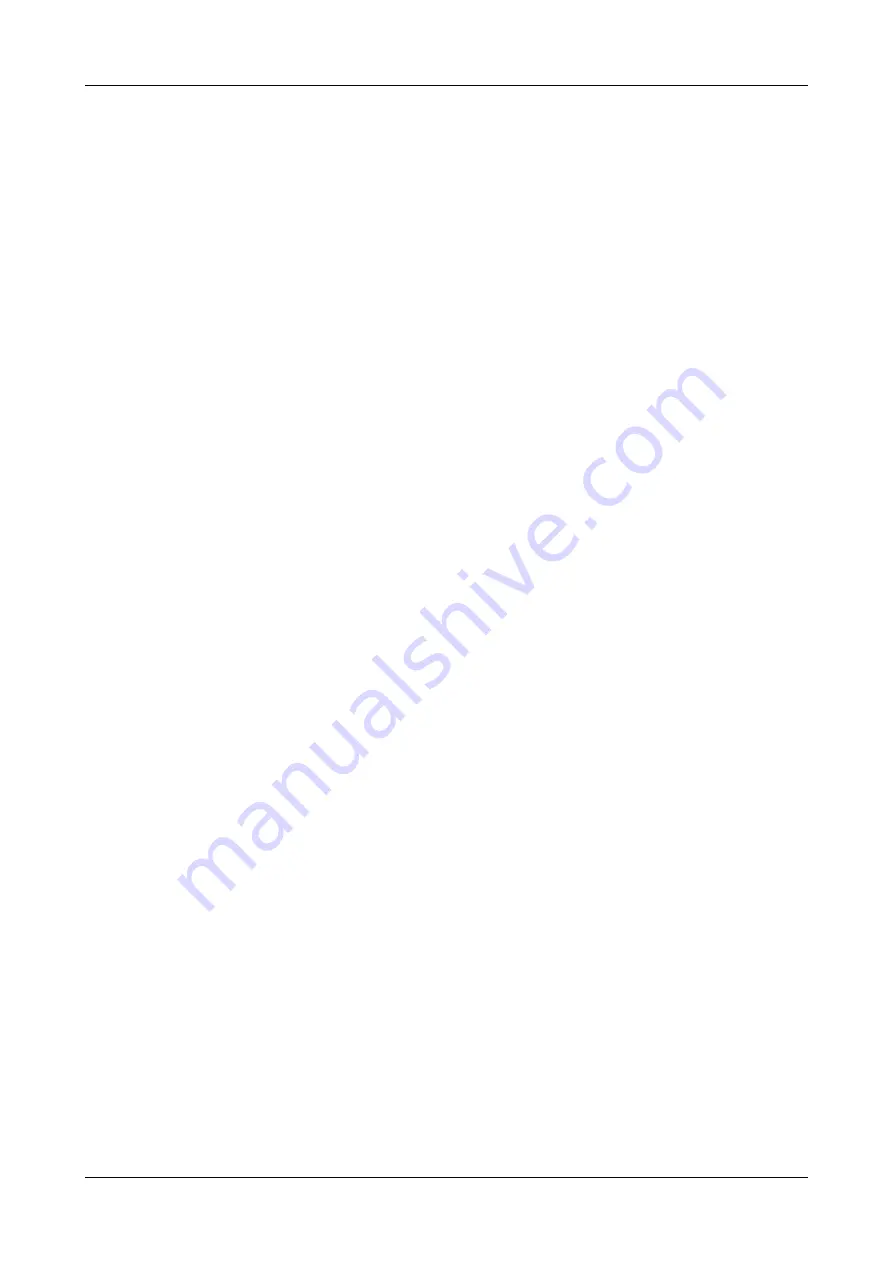
6.8
Test procedure according to PMO for valve type M/ 2.0
Purpose
With test procedure 1, a controller checks if the sensor systems which detect and
confirm the closed position of the upper and lower seats of the PMO - valve (in
accordance with PMO Item 15p (B)- point 1. b. (2)) are correct and are
functioning properly.
With test procedure 2, the controller checks if the superordinate control system
(PLC) of the PMO valve (type M/2.0) is closed effectively during an active CIP
proess.
6.8.1
Test procedure
Please refer to chapter 6.8.2 for an explanation of the required hardware.
Test procedure 1
With test procedure 1, the inspector lifts the seats of the upper and lower valve
disk and checks if the sensor system correctly detects the closed position of the
respective closed valve disk.
Step 1
Requirement:
•
The valve must be in the closed position. This can be recognised by the green
LED of the control head.
Step 2
Carry out the following steps:
1.
Activate the lifting process of the lower seat by controlling the solenoid valve
Y2 via the PLC.
®
When the seat moves downwards (approx. 6 mm), the green LED on the
top of the control top will turn off to indicate that the control top no longer
detects the lower seat as closed position.
®
If the green LED does not turn off, the control top is NOT set correctly and
the adjustment procedure must be repeated as described, see
Section 6.7.1, Page 36.
Step 3
2.
Activate the lifting process of the upper seat by controlling the solenoid valve
Y3 via the PLC.
®
When the seat moves upwards (approx. 2 mm), the yellow LED on the
proximity switch S3 on the lantern will turn off to indicate that the proximity
switch S3 no longer detects the lower seat as closed position.
®
If the yellow LED does not turn off, the proximity switch is NOT set
correctly and the adjustment procedure must be repeated as described,
see Section 6.7.1, Page 36
®
Done
Assembly and installation
Test procedure according to PMO for valve type M/ 2.0
430BAL009261EN_2
17.04.2023
45
Содержание VARIVENT 24/7 PMO
Страница 6: ...430BAL009261EN_2 6 17 04 2023...
Страница 57: ...Fig 25 Requirement Maintenance Disassembly 430BAL009261EN_2 17 04 2023 57...
Страница 107: ...Appendix 430BAL009261EN_2 17 04 2023 107...
Страница 108: ......