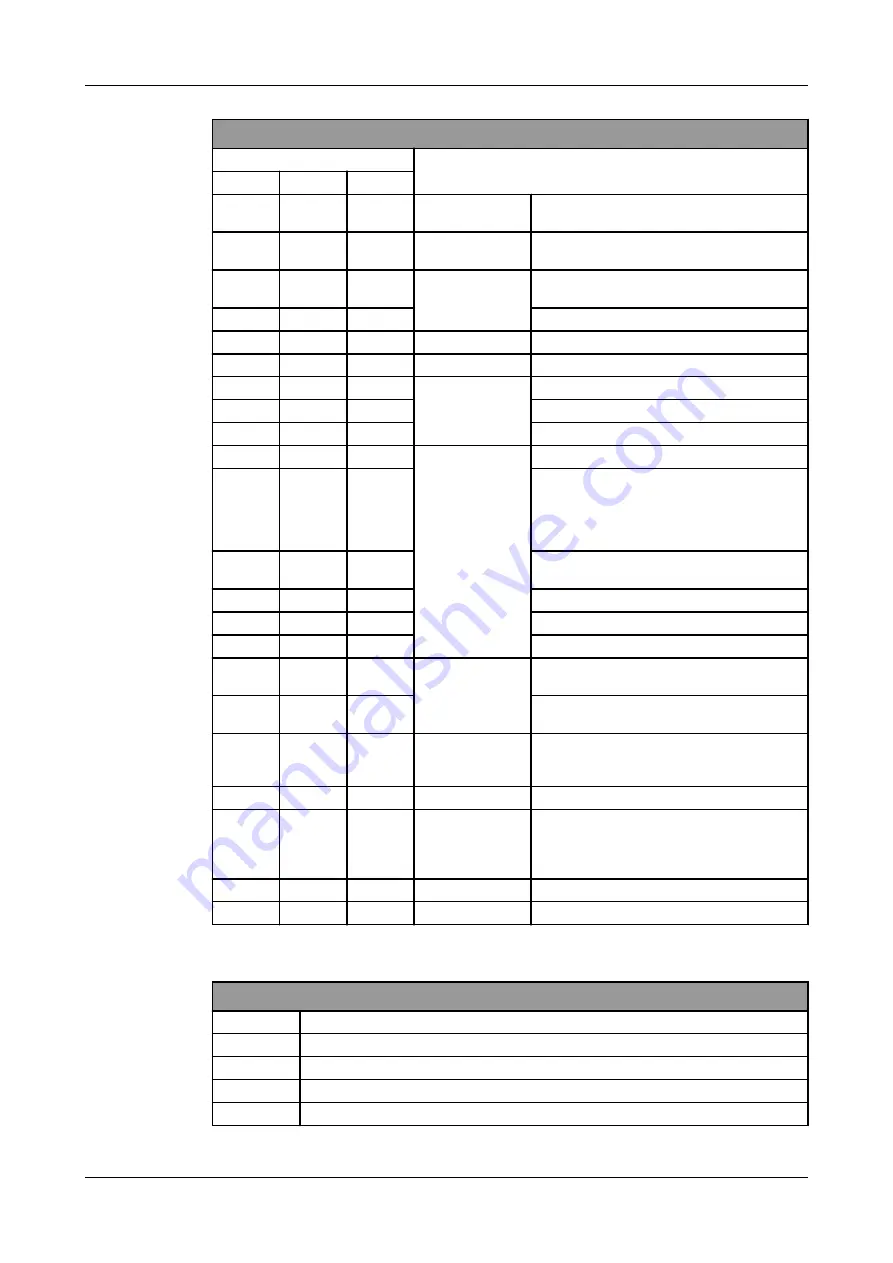
Grasso Maintenance Monitor (GMM) is applied
Maintenance compressor
Description
A
B
C
Visual
inspection
Measure
Big and small end bearing, running surface
Clean
Clean
Clean
Compressor
housing
Inside and outside
Visual
inspection
Measure
Cylinder liners
Cylinder located nearest to the shaft-end of the
compressor
Measure
All cylinder liners
Check
Check
Check
Drive
Coupling alignment
Check
Check
Check
Interstage cooler
Inspections and injection valves
Clean
Clean
Clean
Filters
Oil suction filter
Replace.
Replace
Replace
Oil discharge filter
Check
Clean
Clean
Suction gas
Check
Check
Check
Oil
Oil analysis recommended
If
hygroscop
ic oil is
applied:
Replace
Replace
Replace
Oil refreshment compresssor, oil separator and
oil system
Visual
inspection
Visual
inspection
Oil pump element, oil control and lubrication
pressure regulator
Check
Check
Check
Lubrication and control system
Check
Clean
Clean
Oil separator, test oil return system
Clean
Clean
Clean
Oil cooler fan / heat exchanger
Visual
inspection
Replace
Piston
Rings
Visual
inspection
Measure
Gudgeon pin
Visual
inspection
+ TEST
Visual
inspection
+ TEST
Relief valve(s)
Check
Check
Check
Shaft seal
Oil & Refrigerant leak range
Visual
inspection
Compressor valves
Cylinder located nearest to the shaft-end of the
compressor:
Suction and discharge valves, springs, damper
rings
Check
Replace
Replace
Suction and discharge compressor valves
Check
Thrust bearing
Running surface
3.6.2
Package components
Checklist package components
Description/checkpoint
1
Drive guard
2
V-belts and alignment
3
Coupling alignment
4
Oil level float switch on compressor and oil separator
MAINTENANCE
Description Maintenance ABC when GMM is applied
0089288gbr_11
44
30.10.2017
Содержание Grasso V Series
Страница 6: ...0089288gbr_11 6 30 10 2017 ...
Страница 8: ...0089288gbr_11 8 30 10 2017 ...
Страница 10: ...0089288gbr_11 10 30 10 2017 ...
Страница 61: ...Fig 16 Grasso V 6 Pre lubrication valve APPENDIX Product Information PI 0089288gbr_11 30 10 2017 61 ...