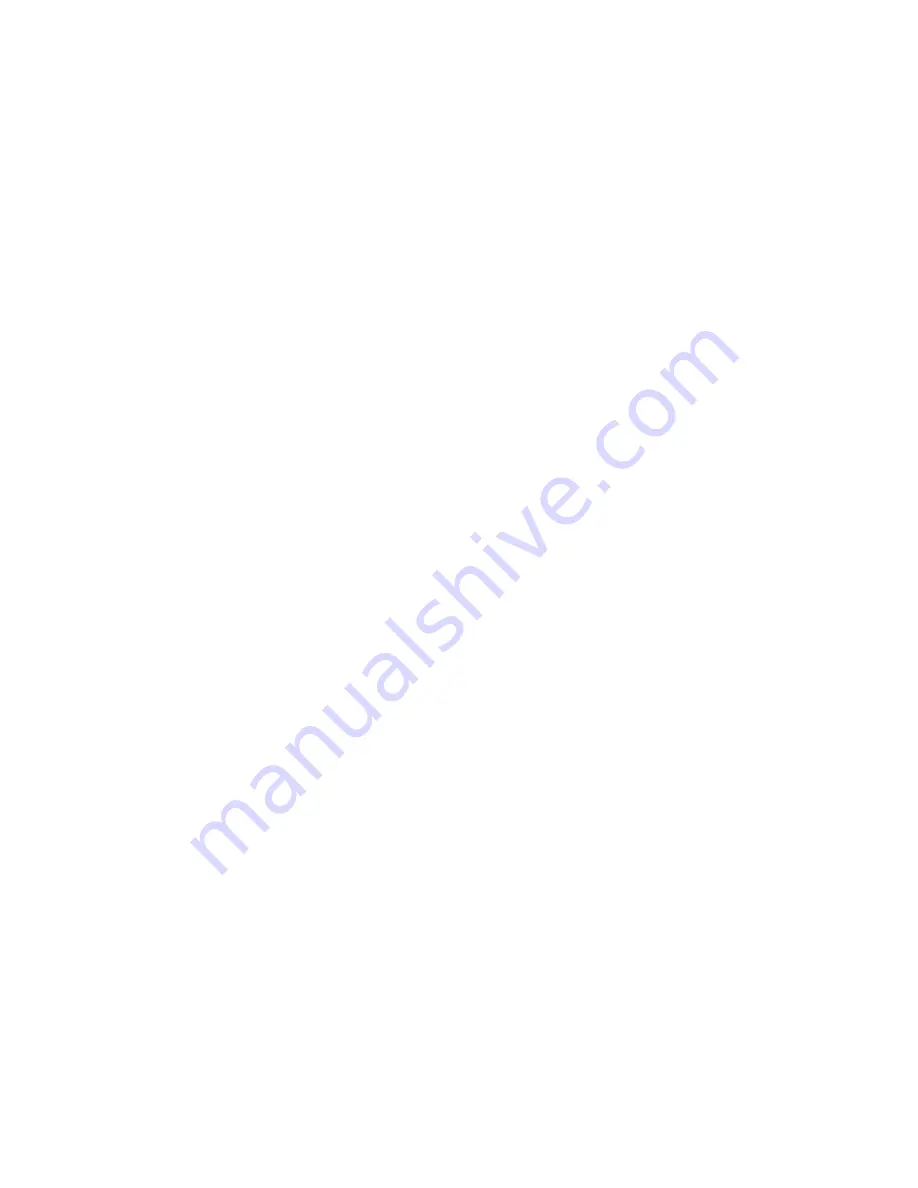
2–4
MM3 MOTOR MANAGER 3 – INSTRUCTION MANUAL
INPUTS AND OUTPUTS
CHAPTER 2: INSTALLATION
2.3.7
Analog Input
The MM3 Motor Manager 3 accepts an analog input from a standard 4 to 20 mA source.
This input can be used for process control monitoring to provide status and/or alarm and
tripping signals related to the input signal level. The analog input messages (
S3 PROCESS
ÖØ
ANALOG INPUT
setpoints page) can be programmed to show user-defined names
and units.
2.3.8
Analog Output
The MM3 Motor Manager 3 is available with a single analog current output for one
parameter. The choice of output is selected with the
S3 PROCESS
ÖØ
ANALOG OUTPUT
Ö
ANALOG OUTPUT TYPE
setpoint. The analog output current scale is 4 to 20 mA.
2.3.9
Auxiliary 2 Coil
The AUX 2 relay can be internally energized by the MM3 Motor Manager 3 or externally
energized by applying a +24 V DC signal to these terminals. Correct polarity is required
(terminal 35 = +24 V DC, terminal 34 = 0 V DC).
2.3.10 Output Relays
There are up to four (4) output relays on the MM3 Motor Manager 3. Contact switching
rating for the output relays as well can be found in
• Contactor A relay (terminals 46 and 47): non-reversing, forward, low speed, etc.
• Contactor B relay (terminals 44 and 45): reversing, high speed, etc.
• AUX 1 relay (terminals 40 to 43): field programmable
• AUX 2 relay (terminals 36 to 39): field programmable or hard-wired 24 V DC coil
2.3.11 Serial Commu-
nication Port
A serial port provides communication capabilities to the MM3 Motor Manager 3. Multiple
MM3 Motor Manager 3 relays can be connected together with a 24 AWG stranded,
shielded twisted-pair with a characteristic impedance of 120
Ω
such as Belden 9841 or
equivalent. The total length of communications wiring should not exceed 4000 feet. Care
should be used when routing the communications wiring to avoid power AC lines and
other sources of electrical noise.
Correct polarity is essential for the communications port to operate. Terminal 25 (“+”) of
every MM3 Motor Manager 3 in a serial communication link must be connected together.
Similarly, terminal 26 (“–”) of every MM3 Motor Manager 3 must also be connected
together. The shield wire must be connected to terminal 27 (485 serial ground) on every
unit in the link to provide a common ground potential for all units. Each relay should be
daisy-chained to the next one. Avoid star or stub connected configurations if possible to
avoid potential communication problems.
A terminating resistor and capacitor network is required to prevent communication errors.
Only the last MM3 Motor Manager 3 and the master computer driver should have the
terminating network to ensure proper matching. Using terminating resistors and
capacitors on all the MM3 Motor Manager 3s would load down the communication
network while omitting them at the ends could cause reflections resulting in
communication errors.
Содержание MM3
Страница 8: ...vi MM3 MOTOR MANAGER 3 INSTRUCTION MANUAL TABLE OF CONTENTS ...
Страница 11: ...CHAPTER 1 INTRODUCTION OVERVIEW MM3 MOTOR MANAGER 3 INSTRUCTION MANUAL 1 3 Figure 1 1 Functional block diagram ...
Страница 18: ...1 10 MM3 MOTOR MANAGER 3 INSTRUCTION MANUAL TECHNICAL SPECIFICATIONS CHAPTER 1 INTRODUCTION ...
Страница 80: ...4 18 MM3 MOTOR MANAGER 3 INSTRUCTION MANUAL CHASSIS MOUNT UNITS CHAPTER 4 SOFTWARE ...
Страница 124: ...5 44 MM3 MOTOR MANAGER 3 INSTRUCTION MANUAL S7 TESTING CHAPTER 5 SETPOINTS ...
Страница 198: ...8 54 MM3 MOTOR MANAGER 3 INSTRUCTION MANUAL MODBUS MEMORY MAP CHAPTER 8 COMMUNICATIONS ...
Страница 220: ...10 14 MM3 MOTOR MANAGER 3 INSTRUCTION MANUAL GE MULTILIN WARRANTY CHAPTER 10 MISCELLANEOUS ...