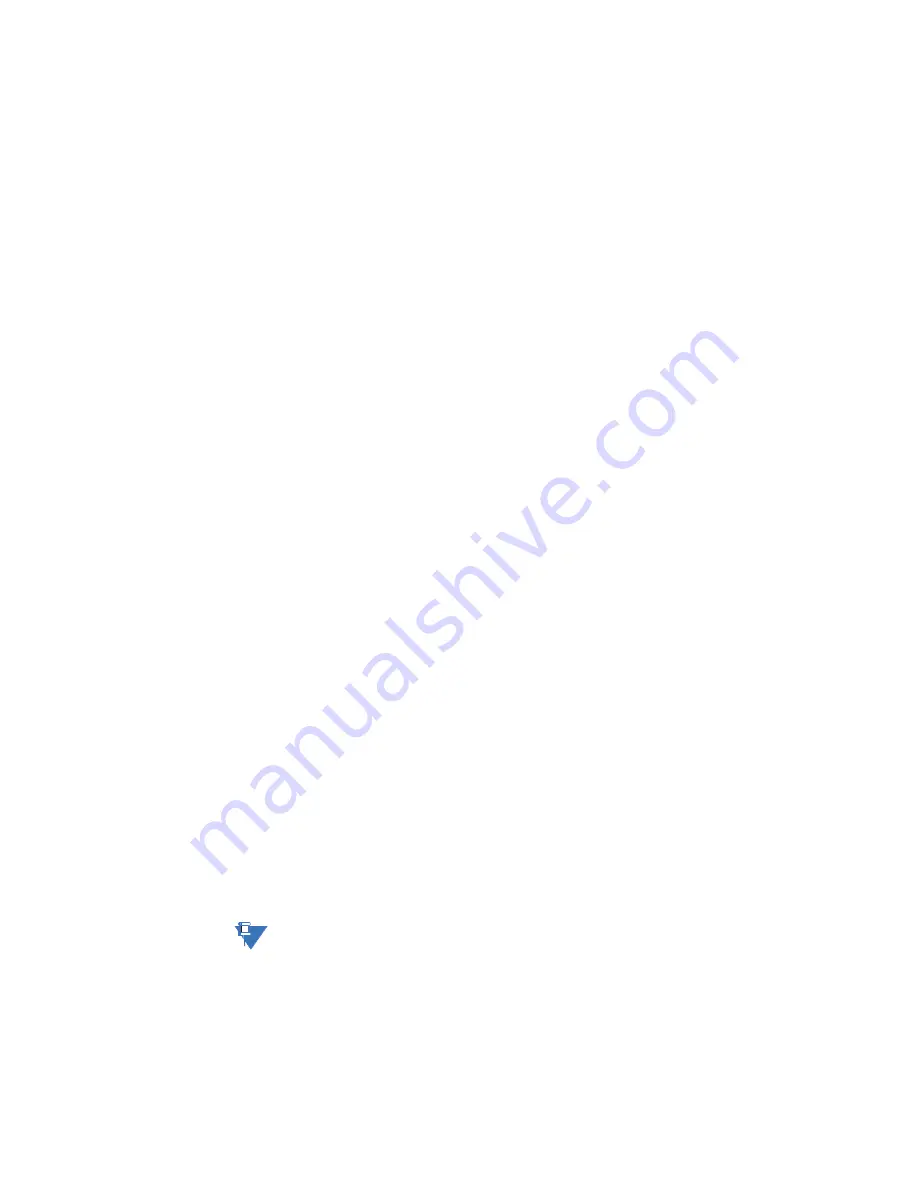
CHAPTER 7: TESTING
FUNCTIONAL TESTS
MM3 MOTOR MANAGER 3 – INSTRUCTION MANUAL
7–5
7.2.3
Ground Fault
Current
Functions
Test the ground fault CT (residual / 50:0.025) in a similar manner to phase currents for
accuracy at various injected current levels. To check alarm and trip levels, make the
following settings.
In the
S1 CONFIGURATION
ÖØ
CT/VT INPUTS
menu, set:
GROUND FAULT CT INPUT
: “RESIDUAL”
In the
S2 PROTECTION
ÖØ
MOTOR PROTECTION GROUND FAULT
menu, set:
GROUND FAULT ALARM LEVEL
: “40 %FLC”
GROUND FAULT TRIP LEVEL
: “80 %FLC”
In the
S2 PROTECTION
Ö
MOTOR PROTECTION THERMAL
menu, set:
FULL LOAD CURRENT
: “100 A”
While displaying the
A1 DATA
Ö
MOTOR DATA
ÖØ
GROUND CURRENT
actual value, begin
injecting current into the 5 A ground fault CT input. The Alarm LED lights and auxiliary relay
1 changes state at 40 A corresponding to the 40% FLC alarm setting. Change the display
back to
GROUND CURRENT
and continue increasing injected secondary current. When the
measured ground current reaches 80 A, a ground fault trip occurs. This trip causes the
MM3 Motor Manager 3 to change its indicators and output relay status. The Running LED
turns off, the Tripped and Stopped LEDs turn on, and the contactor A relay de-energizes.
Auxiliary relay 1 remains energized as long as the alarm is present and auxiliary relay 2
energizes after the ground fault trip. The MM3 Motor Manager 3 displays a ground fault trip
message. Turn the ground fault current off and press the reset key to reset the trip.
7.2.4
Input
Functions
Operation of each MM3 Motor Manager 3 switch input can be verified on the display. Go to
A3 INPUTS
Ö
INPUT CONTACT STATUS
menu view the status of each input one at a time.
Open and close each switch input and note that the display reflects the present status of
the input terminals. The status is shown as either “OPEN” or “CLOSED”.
7.2.5
Thermistor
Input Tests
Begin testing by storing the following thermistor values. In the
S1 CONFIGURATION
ÖØ
THERMISTOR
menu, set
HOT RESISTANCE
: “30 kOHMS”
COLD RESISTANCE
: “0.1 kOHMS”
THERMISTOR ALARM
: “ENABLE”
THERMISTOR TRIP
: “DISABLE”
Place a variable 50 K potentiometer or resistance box across thermistor terminals 17 and
18 as shown in
Secondary Injection Test Setup
on page 7–2. With the input resistance set to
zero, start increasing the resistance until a thermistor alarm occurs. Verify that the Alarm
LED becomes lit and a
THERMISTOR ALARM
message is displayed. Use an ohmmeter to
verify that the thermistor resistance agrees with the
THERMISTOR HOT
setpoint value.
The thermistor will have to be removed from the MM3 Motor Manager 3 to accurately
measure its resistance. When the resistance has decreased below the
COLD RESISTANCE
setpoint value, the alarm will disappear.
To check the thermistor trip function, enable the thermistor trip by making the following
settings changes in the
S1 CONFIGURATION
ÖØ
THERMISTOR
menu:
THERMISTOR ALARM
: “DISABLE”
THERMISTOR TRIP
: “ENABLE”
NOTE
Содержание MM3
Страница 8: ...vi MM3 MOTOR MANAGER 3 INSTRUCTION MANUAL TABLE OF CONTENTS ...
Страница 11: ...CHAPTER 1 INTRODUCTION OVERVIEW MM3 MOTOR MANAGER 3 INSTRUCTION MANUAL 1 3 Figure 1 1 Functional block diagram ...
Страница 18: ...1 10 MM3 MOTOR MANAGER 3 INSTRUCTION MANUAL TECHNICAL SPECIFICATIONS CHAPTER 1 INTRODUCTION ...
Страница 80: ...4 18 MM3 MOTOR MANAGER 3 INSTRUCTION MANUAL CHASSIS MOUNT UNITS CHAPTER 4 SOFTWARE ...
Страница 124: ...5 44 MM3 MOTOR MANAGER 3 INSTRUCTION MANUAL S7 TESTING CHAPTER 5 SETPOINTS ...
Страница 198: ...8 54 MM3 MOTOR MANAGER 3 INSTRUCTION MANUAL MODBUS MEMORY MAP CHAPTER 8 COMMUNICATIONS ...
Страница 220: ...10 14 MM3 MOTOR MANAGER 3 INSTRUCTION MANUAL GE MULTILIN WARRANTY CHAPTER 10 MISCELLANEOUS ...