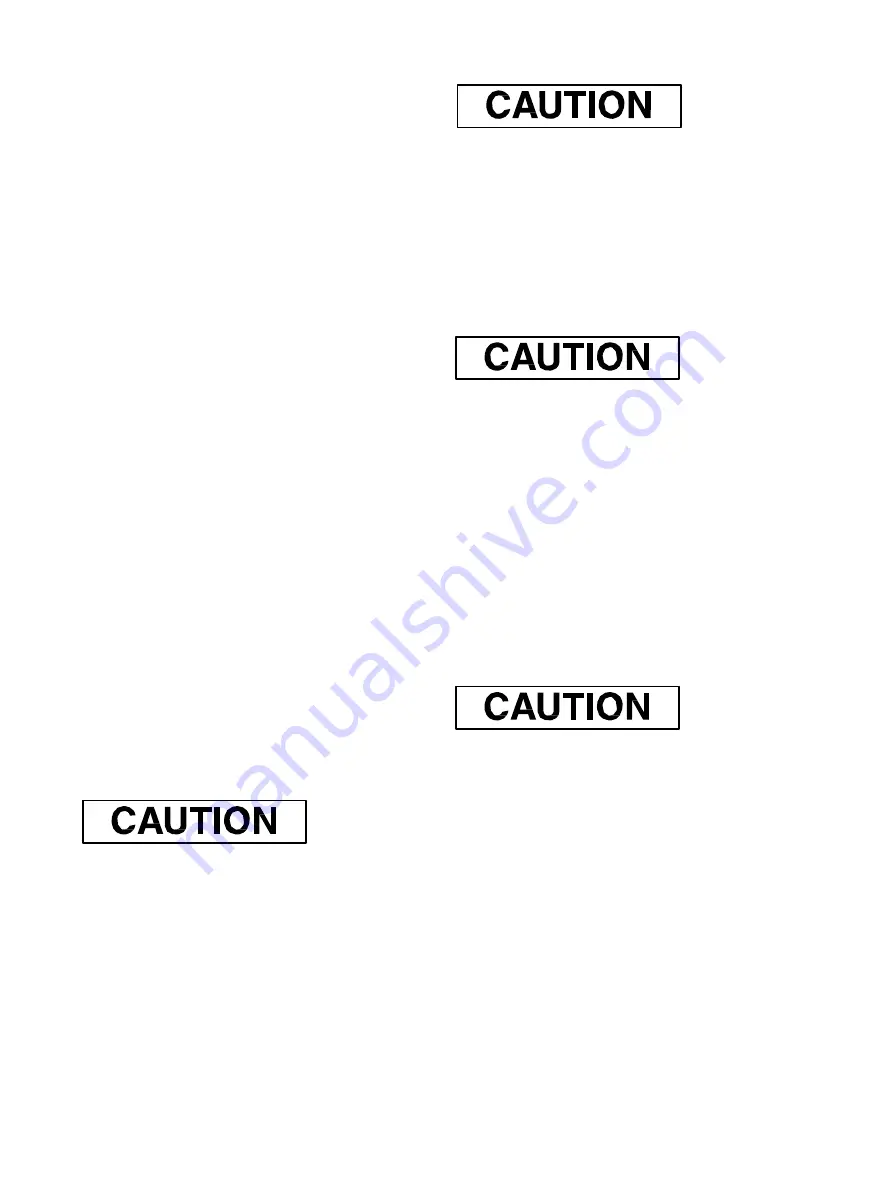
4 | GE Oil & Gas
© 2015 General Electric Company. All rights reserved.
I.
Remove seat ring (12) and seat ring gasket (14).
J.
Remove old packing (6) [and optional lantern ring (20) if a
leak detection connection has been installed]. Refer to
Figure 4.
K.
All components may now be inspected for wear and
service damage. After determining the maintenance
required, proceed to the appropriate Section of this
instruction manual.
8. Maintenance & repair
The purpose of this section is to provide recommended
maintenance and repair procedures. These procedures
assume the availability of standard shop tools and
equipment.
8.1 Lapping Seats
Lapping is the process of working the valve plug against
the seat ring with an abrasive to produce a close fit .
If valve leakage is excessive, lapping becomes necessary.
The plug and seat ring seating surfaces should be free of
large scratches or other defects, and the contact surfaces
of the seats should be as narrow as possible. This may
require dressing both parts in a lathe. The seating surface
angle of the balance plug is 32 degrees, the unbalance
plug is 28 degrees and the seat ring is 30 degrees (relative
to the centerline axis). A good grade of fine grinding
compound is required for the lapping operation.
The compound should be mixed with a small quantity of
lubricant such as graphite. This will slow the cutting rate
and prevent tearing of the seating surfaces. The amount
of lapping required depends on the materials, condition of
seating surfaces, and accuracy of machining. If a short
period of lapping does not visibly improve seating, there is
usually no advantage in continuing as excessive lapping
may result in rough seats. The only remedy is replacement
or re-machining of one or both parts. When lapping new
plugs and seat rings, begin with a medium fine (240grit)
and finish with a finer grade (600grit).
Note
: Lapping should produce a line contact area, not the
entire surface, due to the difference in seat angles.
Before lapping, the plug and stem sub-assembly must be
concentric. (See pinning operation, section 7.2).
1. Clean body gasket surface areas.
2. Ensure that seat ring gasket surface in the body bridge
and the threads are thoroughly cleaned.
Note: Anti-seize compound compatible with the process
should be applied sparingly to the seat ring retainer
threads and bottom surface.
3. Install seat ring and seat ring retainer, and tighten seat
ring retainer by hand.
Do not tighten seat ring retainer to final torque specifications
at this time. The seat ring and seat ring retainer is removed
after lapping seats.
4. Insert the cage into the body.
5. Apply lapping compound on the plug at several spots
equally spaced around the seating area.
6. Insert the stem and plug sub-assembly carefully into
the cage until it is seated.
7. Place bonnet on the body and fasten the bonnet to the
body using four body stud nuts spaced equally apart.
Apply slight pressure and tighten evenly.
Do not tighten nuts to final torque specifications at this time. The
bonnet is used temporarily for guiding purposes only.
8. Insert two or three pieces of packing (6) into the
packing box to assist in guiding the stem and plug
during lapping.
9. Screw a drilled and tapped rod with a T-handle onto
the plug stem and secure with a locknut (see Figure 3).
Note:
As an alternative, drill a hole through a flat steel plate
and fasten to the plug stem using two locknuts.
10. Apply slight pressure on the stem, and rotate the stem
in short oscillating strokes (around 8 to 10 times).
Repeat this step as necessary.
Note:
The plug should be lifted and turned 90° each time
before repeating Step (10). This intermittent lifting is required to
keep the plug and seat ring concentric during lapping.
Avoid over-lapping as this can cause damage to the seating
surface rather than improve leakage performance.
11. After completion of the lapping operation, remove
bonnet and internal parts. The seating area of the seat
ring and the plug must be cleaned of all lapping
compound in preparation for reassembly.
8.2 Plug Stem Pinning
Plug stem pinning in the field may be required for the following:
—
Replacing existing plug and stem, or
—
Replacing existing stem only
Replacing Plug and Stem
If it is necessary to replace the plug, then the plug stem
must be replaced at the same time. The original pin hole in an
existing stem will not provide the necessary fit, and might
seriously impair the strength of the assembly.
Note:
While pinning is being performed, care must be taken not to
damage the seating surface or plug guide. Always use a soft metal
or plastic vice jaws with cylindrical features to hold the plug guide
area (see Figure 6 ).
Содержание Masoneilan 48000 Series
Страница 4: ......