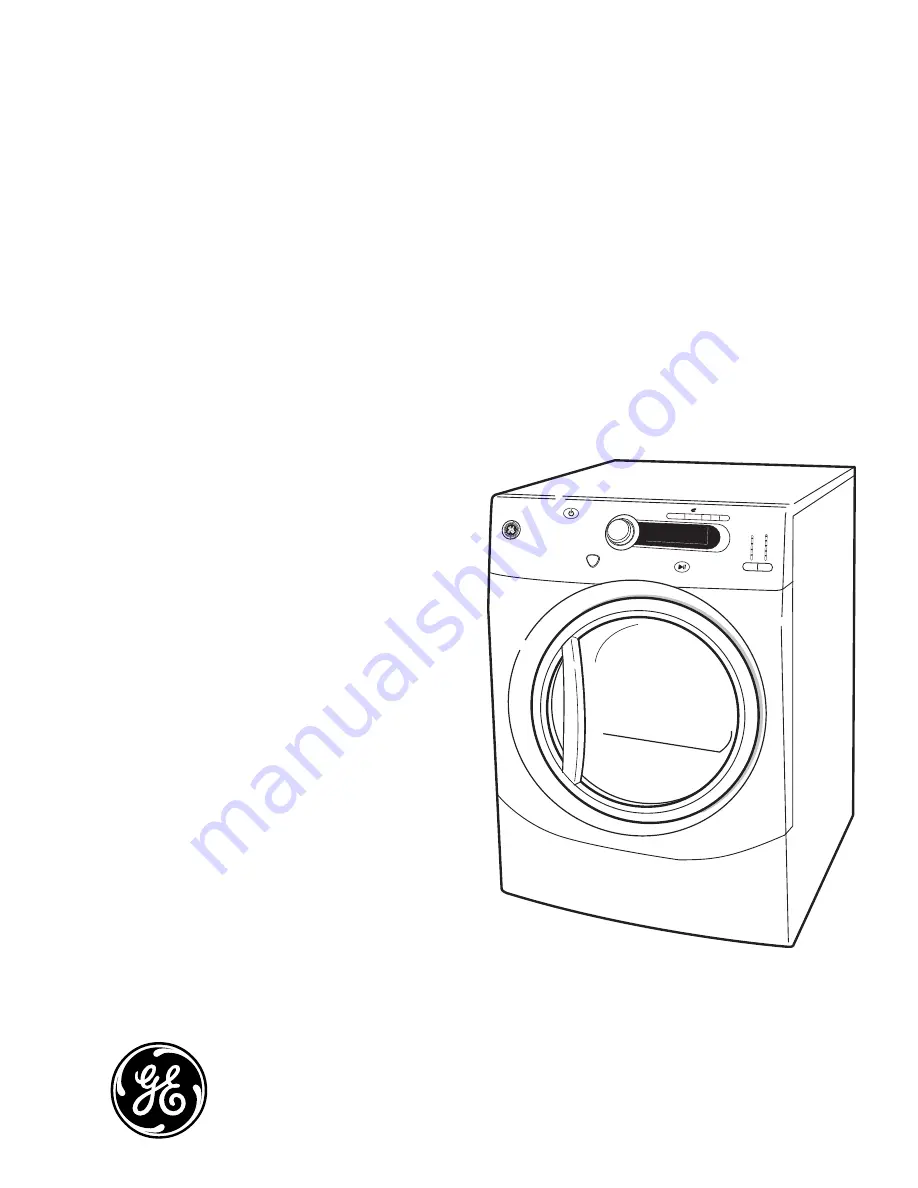
GE Appliances
General Electric Company
Louisville, Kentucky 40225
31-9209
GFDS350
GFDS355
GFDN240
GFDN245
Technical Service Guide
March 2011
GE Appliances
GE HA Dryer With Mist
ACTIVE WEAR
SPEED DRY
PAUSE
COTTONS
NORMAL /
MIXED LOAD
TIME DRY
SENSOR DRY
TIME DRY
WARM UP
AIR FLUFF
DELICATES
P
OWER
L
EVEL
T
EMP
S
TART
EASY CARE
STEAM
REFRESH
STEAM
DEWRINKLE
MY CYCLE
SIGNAL
LOCK
Содержание GFDN240
Страница 12: ... 12 ...
Страница 22: ... 22 Airflow ...