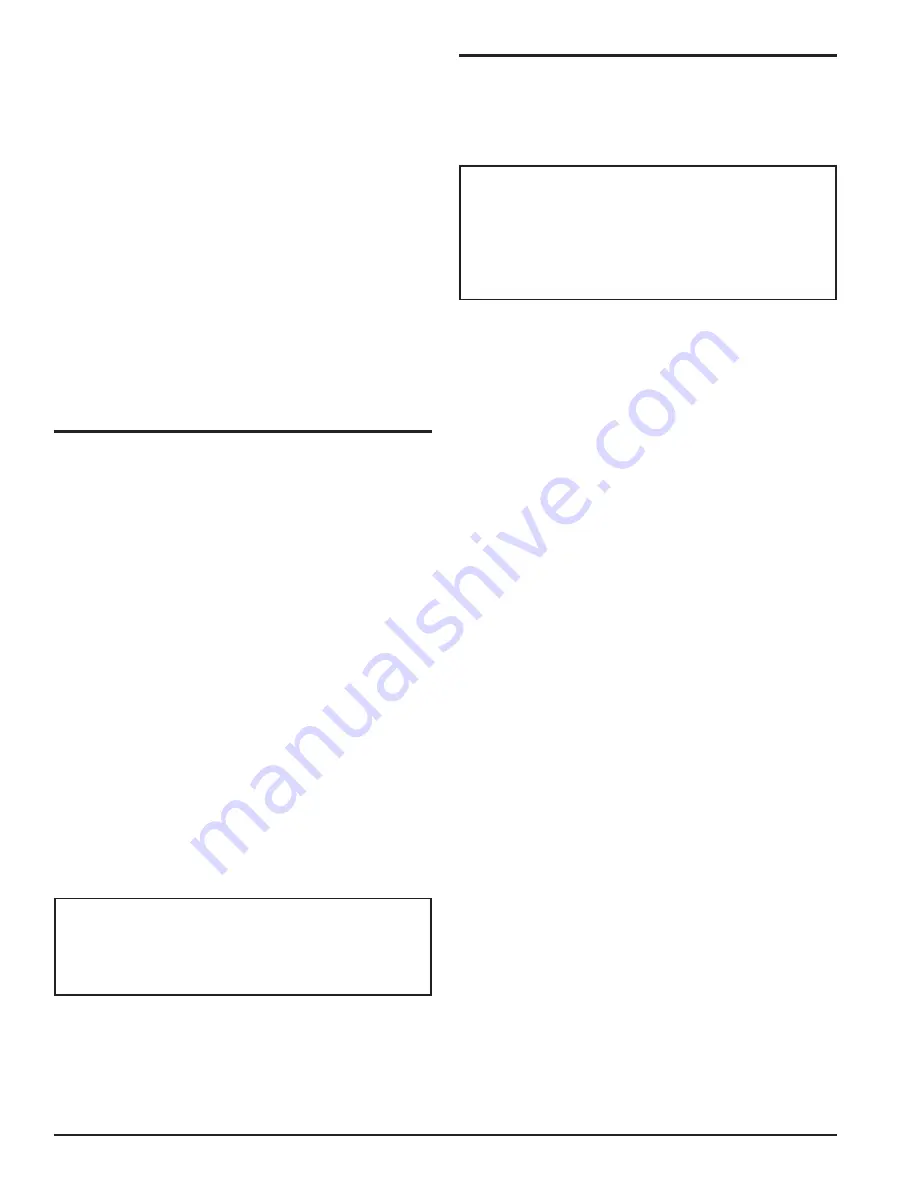
12
• Check the controller display and alarm LEDs for sys-
tem malfunction. Reset as required. If the dryer still
won’t start, call your Deltech distributor for assistance.
5.
With the customer-supplied outlet valve and bypass
valve closed, supply compressed air up to the cus-
tomer-supplied inlet valve.
6.
Slowly open the inlet valve, allowing the dryer to reach
operating pressure. Check for air leaks before con-
tinuing.
7.
Slowly open the customer-supplied outlet valve.
8.
Check drain timing - start with 1-2 minute drain off time
and 3-4 second drain on time. Check timing again af-
ter one hour of operation; when drain is activated, noth-
ing but air should drain for one second before the valve
re-closes. Reset timing if necessary, then check after
another hour of operation. Repeat this procedure until
air vents for one second at the end of the drain period.
SHUTDOWN
Energy Saving Cycling dryers are designed to run continu-
ously. Leave the dryer running even if the requirement for
compressed air is not constant — it will not freeze up. A
warm-up period is required if the dryer is disconnected for
more than 60 minutes.
To stop the dryer:
1.
Push the STOP button. If doing any electrical repairs,
disconnect power at customer-supplied power discon-
nect.
2.
Close the customer-supplied shutoff valve downstream
of the dryer.
3.
Close the customer-supplied shutoff valve upstream
of the dryer.
4.
Open the customer-supplied bypass valve, if installed.
5.
Slowly open the customer-supplied blowdown (inter-
nal pressure relief) valve to vent the internal pressure.
6.
Close the blowdown valve when internal pressure is 0
psig.
DANGER
Portions of the control circuit remain energized
when the dryer is off. Disconnect supply power to
the dryer before performing maintenance on the
electrical system.
Restart the dryer according to the start-up instructions.
MAINTENANCE
Energy Saving Cycling dryers require little maintenance for
satisfactory operation. Good dryer performance can be ex-
pected if the following routine maintenance steps are taken.
DANGER
Dismantling or working on any component of the
compressed air system under pressure may cause
equipment failure and serious personal injury. Be-
fore dismantling any part of the dryer or com-
pressed air system, completely vent the internal
pressure to the atmosphere.
General
For continued good performance of your refrigerated dryer,
all refrigeration system maintenance should be performed
by a competent refrigeration mechanic. Before corrective
maintenance is done during the warranty period, call your
local distributor and proceed according to instructions. Re-
fer to the warranty for limits of your coverage.
Daily Maintenance
Check the operation of the automatic drain valve at least
once during each 8-hour shift. Inspect and clean (if neces-
sary) the drain valve strainer. See the Field Service Guide
for remedies to valve malfunctions. See the Controller sec-
tion for timer adjustment.
Dryers with the Energy Management Controller
Check the following front panel lights:
• Power On LED
• High Temperature Alarm LED
• Low Temperature Alarm LED
If either alarm light is lit, shut down the dryer and refer to
the Controller section to determine the cause.
An accurate record of system operating parameters can
aid in troubleshooting, and can indicate gradual reductions
in system efficiency. Using the DISPLAY SELECT button
on the control panel, check the system temperatures, and
record in the Operator’s Log provided in the back of this
manual.
Monthly Maintenance
For air-cooled condensers, inspect the condenser coils.
Remove dust, dirt or other particles with a soft brush or
with compressed air from an OSHA-approved air nozzle
that limits its discharge pressure to 30 psig. If the coils are
coated with oil, grease or other substances that reduce the
cooling efficiency, clean the coils with a solvent. Follow the
solvent manufacturer’s directions for proper use and dis-
posal, including the use of proper protective equipment.
Содержание RCD1000
Страница 27: ...27 NOTES ...