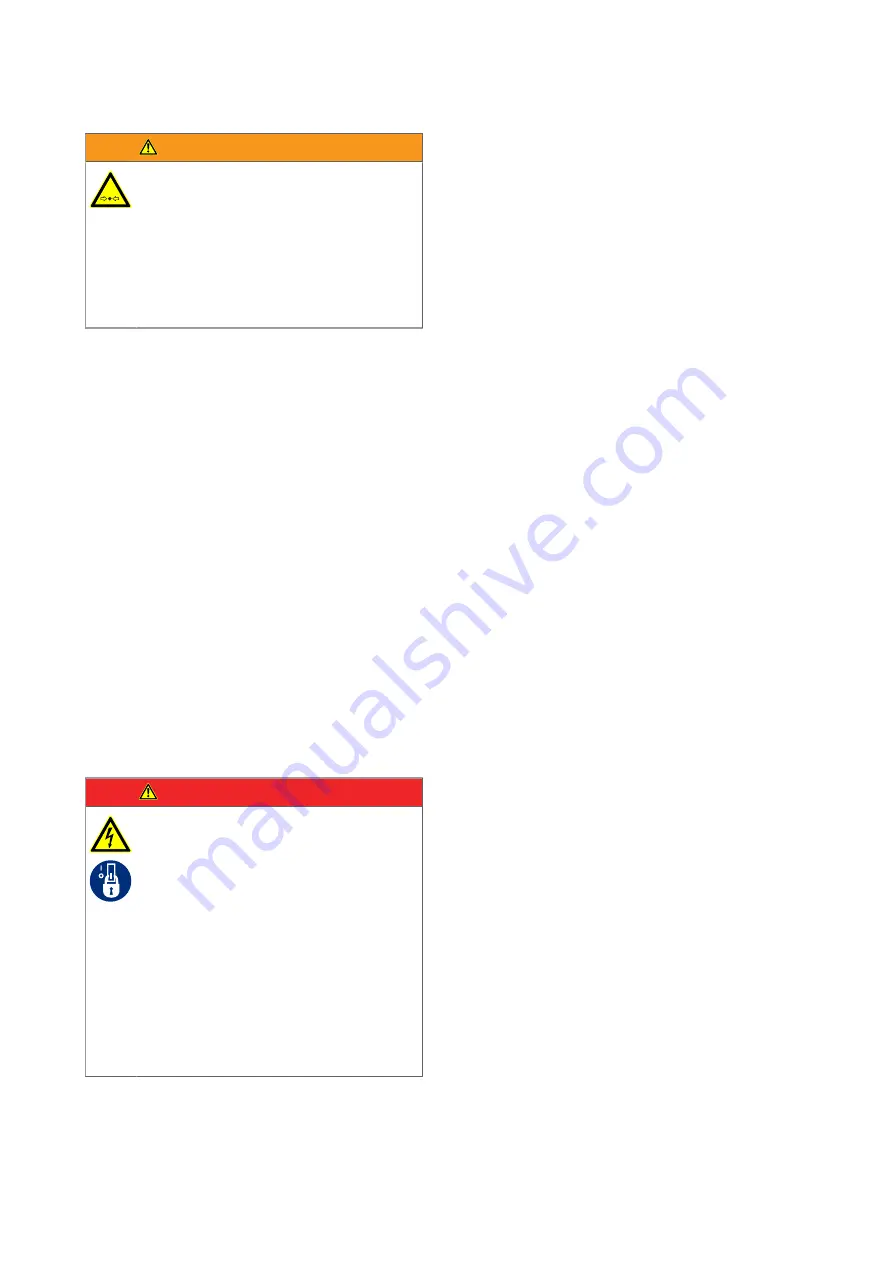
Manual pressure relief
WARNING
Pressure components
Even when the compressor is depres-
surised, the aftercooler remains under
pressure.
➯
Carry out manual pressure dis-
charge before maintenance work is
carried out in the vicinity of the after-
cooler.
1. Connect the (site provided) shut-off valve in the
supply line.
2. Switch the main switch OFF.
3. Open the enclosure, create access.
4. Undo the lock screw on the closed air vent
valve (ball valve at the pressure-retaining
valve).
5. Depressurise the aftercooler by careful opening
of the air vent valve.
6. Close the air vent valve and screw in the air
vent valve.
7. Upon completion of maintenance work, open
the shut-off valve in the supply line.
Test run
A test run should be carried out after all main-
tenance work; this should amongst other things
make possible the detection of any leaks. During
every test run, the low-noise running of the com-
pressor must also be ensured.
Electrical components
DANGER
Electric shock
Life-threatening electric shock
➯
Work on the electrical equipment
must only be carried out by autho-
rised electricians or electrical techni-
cians.
➯
With the speed-controlled types
RS
,
there is a risk of electric shocks due
to charged capacitors!
Switch the compressor voltage-free
and wait 10 minutes before touching
any electrical parts.
➯
Checking the DC bus voltage.
Check the DC bust voltage of the frequency
converter
The DC bus voltage is measured at the mains ter-
minal strip of the frequency converter. The precise
position of the terminals "DC+" and "DC-" can be
taken from the supplied frequency converter oper-
ating instructions.
1. Measure the voltage between the DC+ and
DC- terminals.
2. Measure the voltage between the DC+ terminal
and the chassis.
3. Measure the voltage between the DC- terminal
and the chassis.
The voltage must read zero in all three measure-
ments.
Water-cooled compressors
When operating water-cooled screw compressor
systems, the following points should be noted.
•
A partial quantity of the oil may get into the
cooling water circuit due to leaks in the oil–wa-
ter coolers. Cooling water must not be intro-
duced to the public wastewater systems in an
uncontrolled manner. Uncontrolled overflows
from oil separation tanks into public wastewater
systems are to be prevented. Wastewater regu-
lations must be implemented carefully.
•
Carry out maintenance and repair work care-
fully. Removed tube bundles must be checked
for damage before reinstallation (and replaced
even in case of minor damage). Always use
new seals during installation.
8.2
Service
The global spare parts and customer service net-
work of Gardner Denver is available worldwide.
The local Gardner Denver subsidiary or the re-
sponsible dealer is available for any spare parts
requirements.
It is important that the model name and the serial
number of the compressor are stated in all mes-
sages.
Spare parts orders
Spare parts orders to:
Germany
Tel.: +49 (0)6761/832-136
Fax.: +49 (0)6761/832-411
International