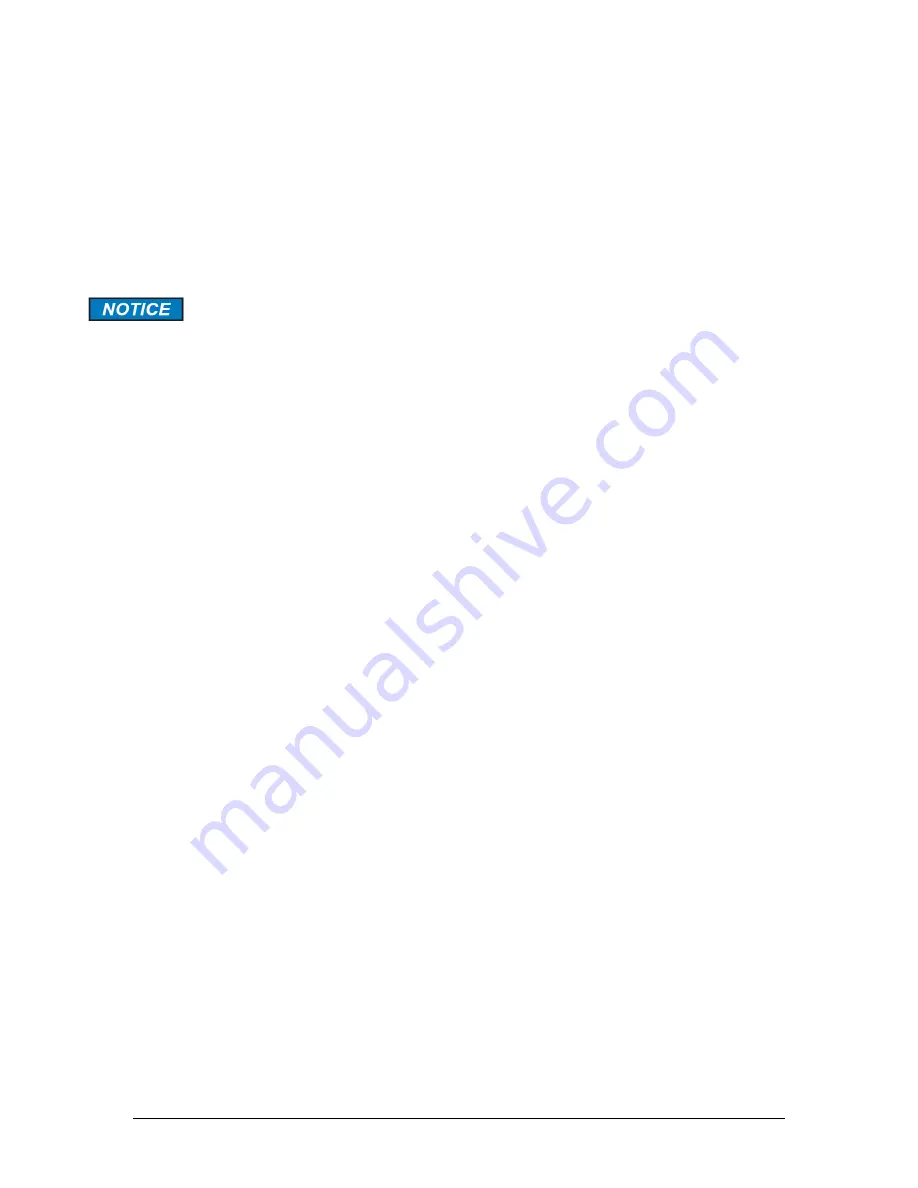
Revision 5
43
August 2021
During a zero-calibration sequence or back purge operation, instrument air is forced into the
sample probe and the analyzer sample handling system, including the measurement cell.
The indicated sulfur vapour concentration during and immediately after a back-purge
operation is NOT representative of the sulfur vapour concentration in the process sample
gas.
The condenser cooling air flow adjust valve is typically opened two turns from fully closed.
The optimal situtation is that the indicated concentration of sulfur vapour in the
process sample gas exiting in the measurement cell is lower with the probe
cooling air on than with the probe cooling air off, without causing plugging of the
sample probe.
3.4.3 Zero Air Flow Adjust Valve
The
Zero Air Flow Adjust Valve
is used to adjust the flow rate of the instrument air used
for back purge and zero calibration operations. The zero calibration is performed when the
analyzer is in back-purge condition, and the probe and sample handling system, including
the measurement cell, are full of zero gas. Under normal operating circumstances, the valve
is adjusted so that the response time from sample conditions to a stable zero reading is
between 2 and 5 seconds, although depending on the sample probe length, this time may
be somewhat longer. The stabilized zero response is determined by monitoring the time
required for the analyzer gas concentration outputs to stabilize at near zero levels once the
analyzer has been switched from sampling to zero (back purge) mode. Excessive zero air
flow rates will overly cool oven components and may lead to cell temperature control issues.
If the zero air flow rate is set too low, inadequate flushing of the measurement cell before a
zero adjustment is made may result. If the analyzer is zeroed before the measurement cell
has been adequately flushed with zero gas, the concentration readings obtained on sample
gas after returning to sampling mode will likely be lower than expected. This valve is typically
opened one turn from fully closed. In extraordinary circumstances, if sample system or
sample probe clogging due to sulfur vapour condensation occurs, the Zero Air Flow Adjust
Valve
may be opened wide to provide a solid back purge pressure. Alternately, the Zero Air
Flow Adjust Valve
may be turned down to a trickle for an extended period (20-30 minutes)
to allow the heat of the oven and probe nozzle to re-liquefy any solid accumulation (plugging)
before increasing the flow rate dramatically to purge out the re-liquefied sulfur. If this is not
successful in clearing a blockage in the probe, a steam purge of the probe will be required.
Refer to section 7.8.
3.4.4 Aspirator Drive Air Flow Adjust Valve
The
Aspirator Drive Air Flow Adjust Valve
indirectly controls the rate of process sample
gas extraction from the tail gas duct. The aspirator drive air is plumbed to a venturi-type
eductor integral to the measurement cell
block, as shown in the exploded view of the
measurement cell in Figure 19.
Содержание 943-TGS-CE
Страница 137: ...Revision 5 137 August 2021 Figure 84 Oven Cabinet Details...
Страница 138: ...Revision 5 138 August 2021 Figure 85 Control Cabinet Door Closed...
Страница 139: ...Revision 5 139 August 2021 Figure 86 Control Cabinet Door Removed...
Страница 140: ...Revision 5 140 August 2021 Figure 87 Power Steam Air Signals Connection Details...
Страница 141: ...Revision 5 141 August 2021 Figure 88 AC Wiring Schematic...
Страница 142: ...Revision 5 142 August 2021 Figure 89 DC Signals and Wiring Diagram...
Страница 143: ...Revision 5 143 August 2021 Figure 90 Flow Diagram...
Страница 144: ...Revision 5 144 August 2021 Figure 91 Control and Oven Cabinets Interconnect Wiring...