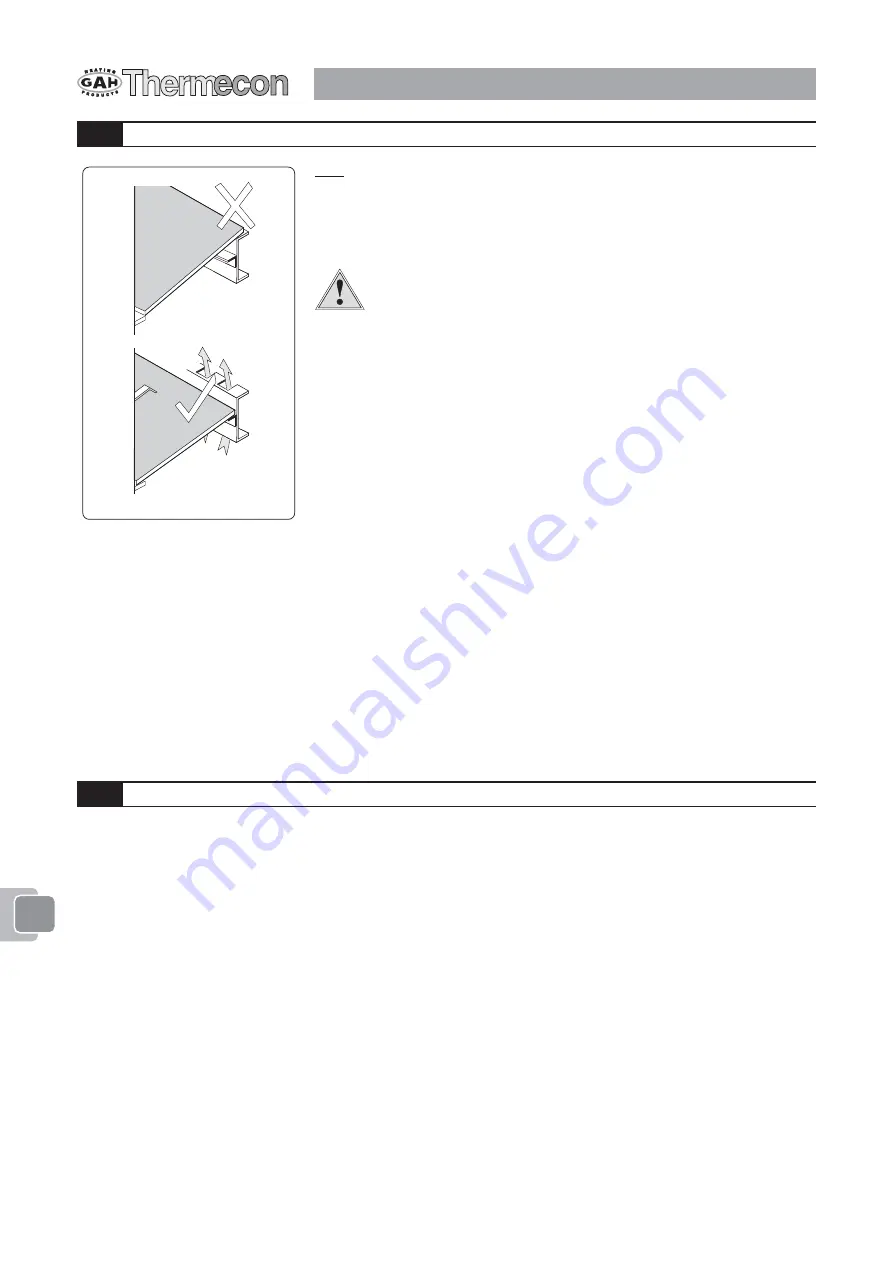
38
SERVICING 11
SERVICING 11
SERVICING 11
SERVICING 11
SERVICING 11
11-1
Routine Service
FUEL
FUEL
FUEL
FUEL
FUEL 28 Second Class C K
28 Second Class C K
28 Second Class C K
28 Second Class C K
28 Second Class C Ker
er
er
er
erosene - ONCE A YEAR.
osene - ONCE A YEAR.
osene - ONCE A YEAR.
osene - ONCE A YEAR.
osene - ONCE A YEAR.
It is good policy to measure the smoke, CO², flue gas temperature and oil pressure,
before carrying out the routine service. At the same time, check for combustion leaks, oil
leaks and any unusual noises from the Burner or system. Comparison of ‘before’ and
‘after’ results is facilitated.
IMPORTANT
Always turn off the oil supply and switch off and disconnect the electricity
supply before working on the Boiler.
Paper type filter elements should be changed.
Elements of mesh type filters should be washed in kerosene. The oil tank should be de-
sludged.
Remove the Burner and thoroughly clean, paying particular attention to the blast tube and
its airways. Electrodes should be checked for wear and crazing of the porcelain. Ensure
nozzle is of type and size for output required, see 13-3.2.
In very dusty conditions, the fan and photocell may need cleaning.
Flexible oil lines should be carefully inspected. It is recommended that flexibles are
renewed every two years. If in any doubt fit new.
11-1.1 Boiler
All Boilers have a flueway door giving access to remove baffles. Baffles should be lifted
out to enable the heat exchanger to be thoroughly vacuumed clean.
It is important that all flueway doors have a good rope seal and are tightened correctly.
Check that the air pipe from the manifold to the Burner is in good condition and properly
connected at both ends (balanced flue only).
11-1.2 Combustion Test
This must equate to the data in the manual, see pages 45 & 46.
11-2
Extra Procedure for System Boilers
In addition to the Routine Servicing detailed in Section 11-1, the following procedure
should be included.
11-2.1 Cold Fill Pressure
Check the cold fill pressure is as recorded, reset the red pointer if required.
A drop in the cold fill pressure indicates that the system requires topping up. If regular
topping up is required it indicates that there may be a leak in the system.
Refer to 5-5.12 Filling the System.
11-2.2 Pressure Relief Valve
Check as detailed in 5-5.5.
Fig. 11-1a Baffles Position
11
11
11
11
11