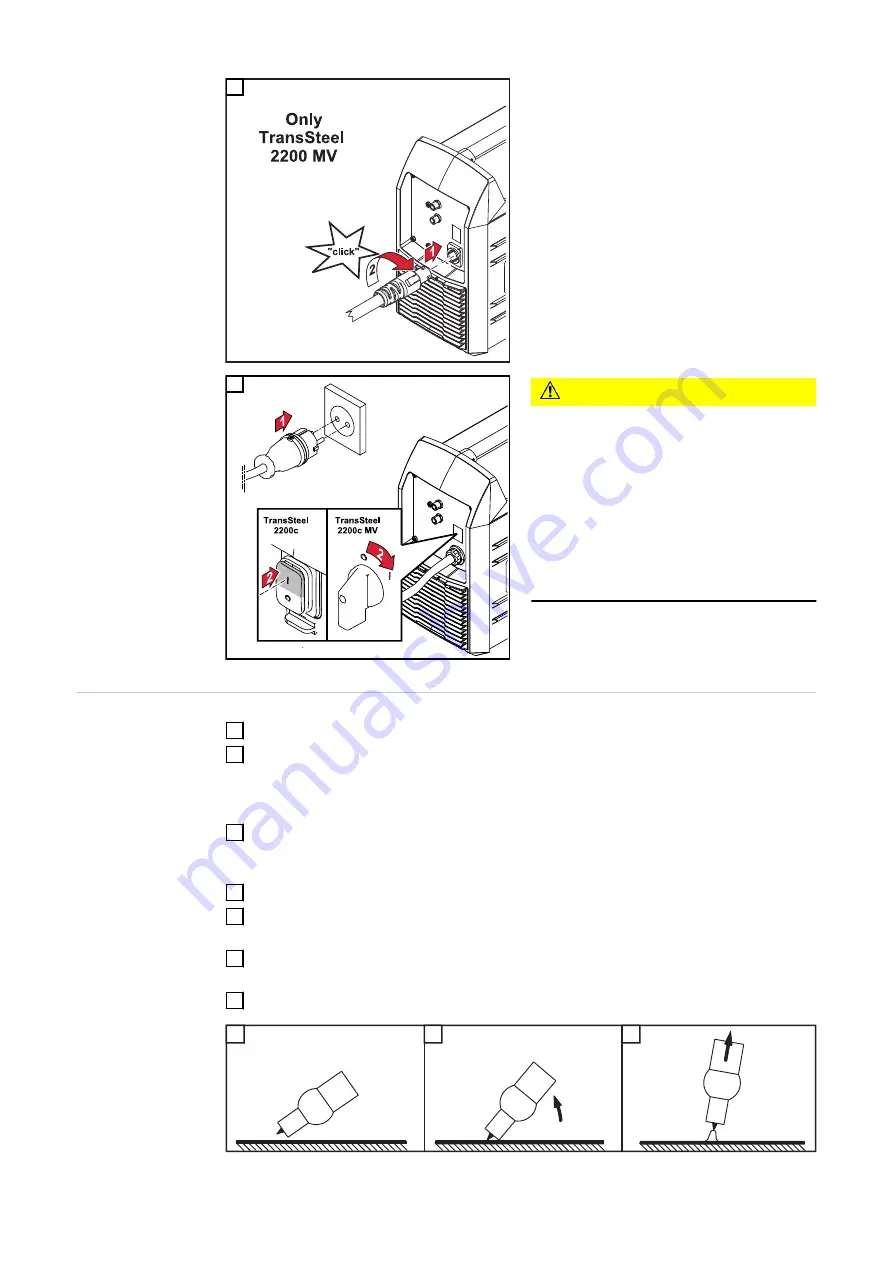
6
It is only necessary to connect the mains
cable to the power source for multivoltage
power sources.
7
CAUTION!
Danger due to welding processes start-
ing unintentionally.
Personal injury and damage to property
may result.
▶
As soon as the power source is
switched on, ensure that the tungsten
electrode does not accidentally, or in
an uncontrolled manner, touch any
electrically conductive or grounded
parts (e.g., the housing, etc.).
TIG welding
1
Press the "Process" button to select TIG
2
Set the desired welding current
When using a welding torch with a torch trigger and TIG Multi Connector plug
(with 2-step mode factory setting):
3
Position the gas nozzle at the ignition point so that there is a distance of approxim-
ately 2 to 3 mm (0.078 to 0.118 in.) between the tungsten electrode and the work-
piece
4
Gradually tilt the welding torch up until the tungsten electrode touches the workpiece
5
Pull back the torch trigger and hold it in this position
-
Shielding gas flows
6
Raise the welding torch and rotate it into its normal position
-
The arc ignites
7
Carry out welding
3
4
6
76
Содержание TransSteel 2200
Страница 2: ......
Страница 18: ...18...
Страница 19: ...General information 19...
Страница 20: ...20...
Страница 22: ...Application areas MIG MAG welding TIG welding Manual metal arc welding 22...
Страница 29: ...Operating controls and connections 29...
Страница 30: ...30...
Страница 40: ...40...
Страница 41: ...Before installation and initial opera tion 41...
Страница 42: ...42...
Страница 50: ...Fitting the Carrying Strap Fitting the carry ing strap to the power source 1 2 3 4 5 6 50...
Страница 51: ...MIG MAG 51...
Страница 52: ...52...
Страница 55: ...Inserting the D100 wirespool 1 2 Inserting the D200 wirespool 1 2 3 55 EN US...
Страница 73: ...TIG 73...
Страница 74: ...74...
Страница 75: ...Commissioning Start Up 1 2 3 4 5 75 EN US...
Страница 83: ...Rod Electrode 83...
Страница 84: ...84...
Страница 88: ...For a parameter description see section Parameters for MMA Welding from page 99 88...
Страница 89: ...EasyJobs 89...
Страница 90: ...90...
Страница 92: ...92...
Страница 93: ...Setup Menu 93...
Страница 94: ...94...
Страница 104: ...104...
Страница 105: ...Optimizing Weld Quality 105...
Страница 106: ...106...
Страница 110: ...110...
Страница 111: ...Troubleshooting and Maintenance 111...
Страница 112: ...112...
Страница 124: ...124...
Страница 125: ...Appendix 125...
Страница 126: ...126...
Страница 134: ...134...
Страница 135: ...135 EN US...