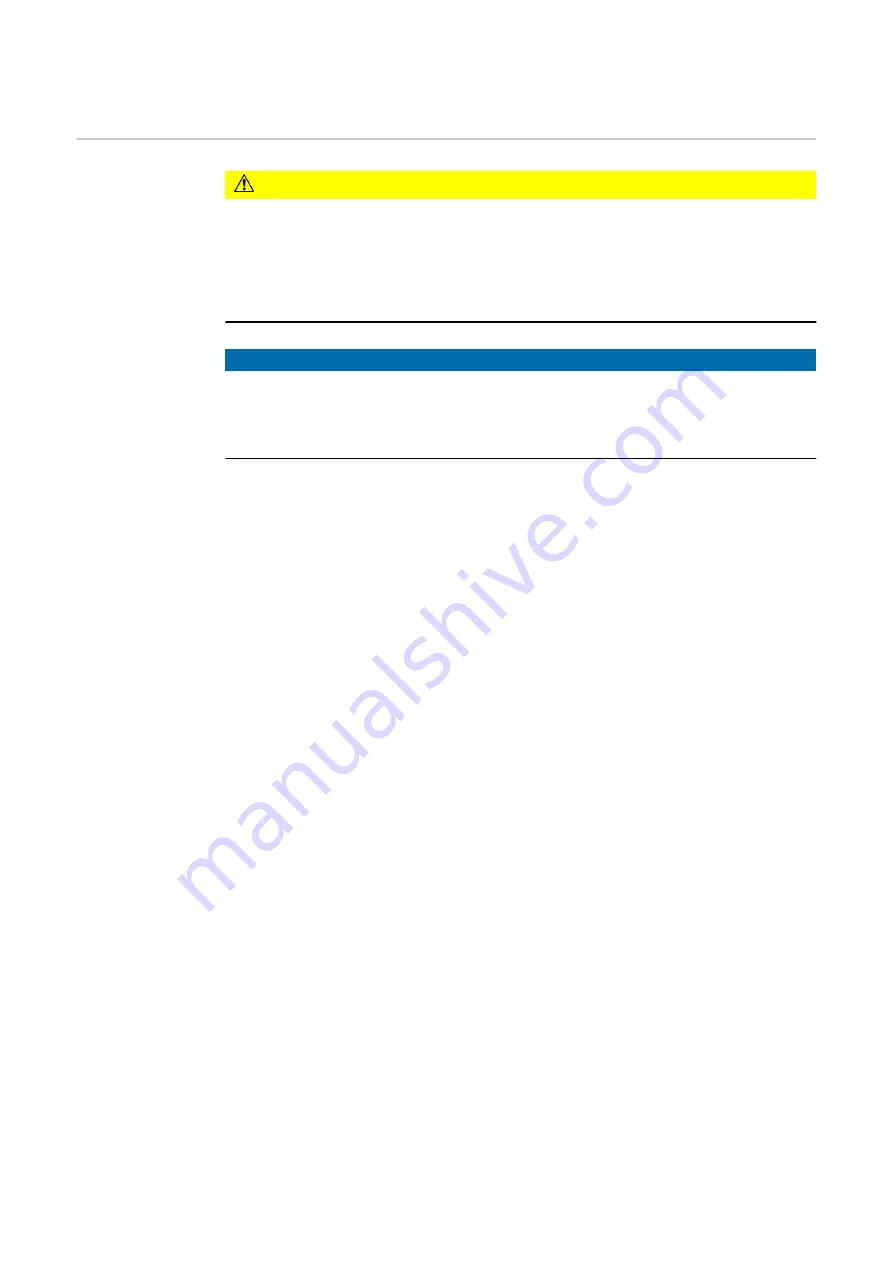
Cleaning programme
Safety
CAUTION!
Danger due to improper installation and commissioning.
This can result in damage to property.
▶
The cleaning device's functions must be manually checked before starting
automatic operation.
▶
Do not start in automated mode until the cleaning device has been properly
installed and started up.
NOTE!
Not coating the interior of the welding torch may result in permanent soiling of
the torch when welding begins.
▶
Always wet the interior of the welding torch with the manufacturer's parting
agent before starting automatic operation.
54
Содержание Robacta Reamer V Twin
Страница 1: ...Operating Instructions Robacta Reamer V Twin 42 0426 0142 EN 024 29082022 EN Operating instructions...
Страница 2: ......
Страница 12: ...12...
Страница 13: ...General 13...
Страница 14: ...14...
Страница 18: ...Wear eye protection Notice warning of automatic start up of the device 18...
Страница 20: ...20...
Страница 21: ...Controls connections and mechan ical components 21...
Страница 22: ...22...
Страница 27: ...Installation and commissioning 27...
Страница 28: ...28...
Страница 40: ...8 7 8 8 8 8 7 Fit the housing cover 8 Secure the housing cover with five M4 x 8 mm Allen screws size 3 mm 40...
Страница 67: ...Care maintenance and disposal 67...
Страница 68: ...68...
Страница 72: ...Disposal Dispose of in accordance with the applicable national and local regulations 72...
Страница 76: ...76...
Страница 77: ...Troubleshooting 77...
Страница 78: ...78...
Страница 83: ...Technical data 83...
Страница 84: ...84...
Страница 86: ...86...
Страница 87: ...Appendix 87...
Страница 88: ...88...
Страница 92: ......