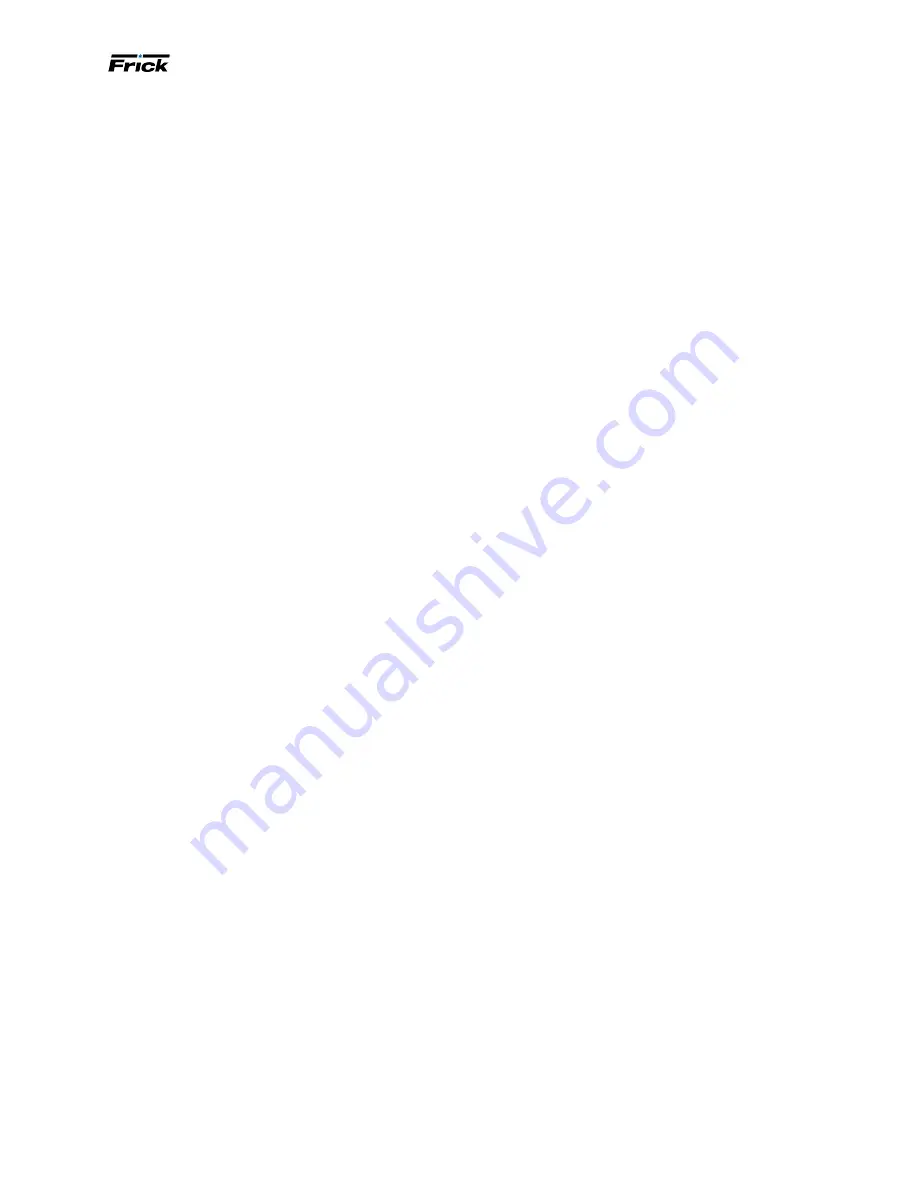
070.655-IOM (FEB 22)
Page 5
SBTP Rotary Screw Compressor
Installation - Operation - Maintenance
Oil pump
A full-time lube oil pump is required for all sleeve bear-
ing compressor applications. Refer to CES 6608 for basic
oil pump requirements and basic piping diagrams. Actual
system operating conditions may necessitate the need for
piping systems other than those addressed by CES 6608.
Contact Johnson Controls-Frick Service for assistance.
The pump must be run before starting the compressor to
ensure adequate oil pressure and temperature is being
supplied to the machine. Do this by using an automated
diverting valve that bypasses oil flow back to the oil sepa
-
rator until the correct oil conditions are verified. After this
the diverter valve switches to direct oil to the compressor,
at which point you can start the compressor. At shutdown,
the oil pump must continue to run until the compressor
has stopped rotating. Failure to provide adequate oil pres-
sure and temperature to the compressor while it is running
may lead to equipment damage.
Construction details
Housing:
all SBTP screw compressor castings are steel
to ensure structural integrity and mechanical and thermal
stability under all operating conditions.
Rotors:
the rotors are machined from AISI-1141 or Y40Mn
steel to the exacting tolerances of the latest Frick profile.
The male rotor is directly connected to the driver while
the
female rotor is driven by the male on a thin oil film.
Bearings:
SBTP compressor models use API compliant
journal bearings and tilting pad thrust bearings to absorb
radial and axial loads respectively. The cylindrical sleeve
bearings are oil grooved for optimal lubrication and higher
radial load capability. The tilting pad thrust bearing uses
offset pads and directed lubrication to minimize power
loss and maintain lower bearing temperatures at lower oil
flows for maximum bearing life
.
Shaft seal:
the compressor is supplied with a single-
face type mechanical shaft seal with metallic stationary
and rotating faces. Materials vary to suit the application.
Tandem style seals can also be supplied at additional cost
if required The seal is capable of withstanding static pres-
sure up to 700 psig.
Volumizer variable volume ratio control:
the Frick com-
pressor includes a method of varying the internal volume
ratio to match the system pressure ratio. Control of the in-
ternal volume ratio eliminates the power penalty associated
with over- or under-compression. Volume ratio control is
achieved by the use of a slide stop which is a movable por-
tion of the rotor housing that moves axially with the rotors
to control discharge port location. The slide stop is moved
by hydraulic actuation of a control piston.
Stepless capacity control:
capacity control is achieved
by use of a movable slide valve. The slide valve moves
axially under the rotors to provide fully modulated capac-
ity control from 100% to approximately 12% minimum
load capacity. Approximate minimum load capacity varies
slightly with compressor model, pressure ratio, discharge
pressure level, and rotor speed.
The slide valve is positioned by hydraulic movement of its
control piston. When in the unloaded position, gas is by-
passed back to suction through a recirculation slot before
compression begins and any work is expended, providing
the most efficient
unloading method available for part-
load operation of a screw compressor.