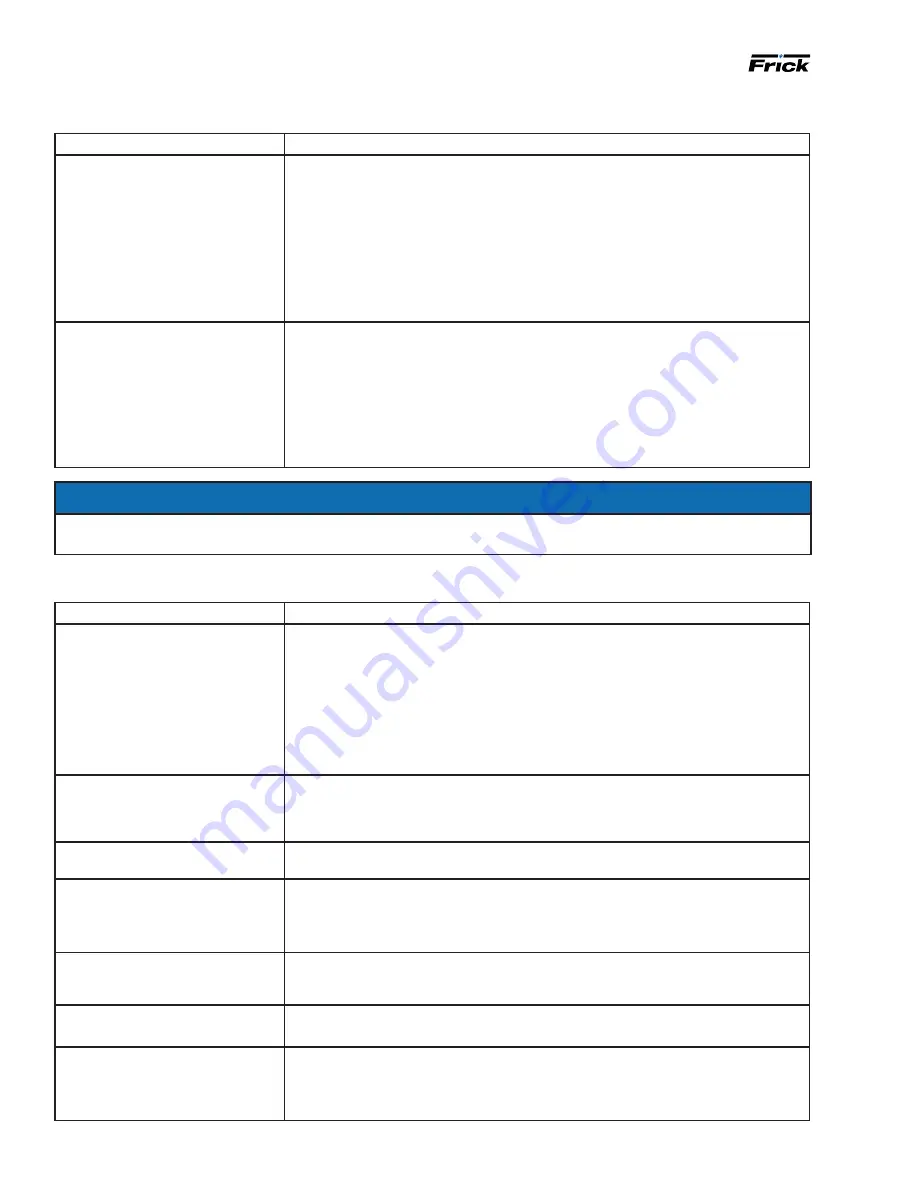
070.610-IOM (JUL 21)
Page 50
RWF II Rotary Screw Compressor Units
Maintenance
Troubleshooting the RWF II compressor
Symptom
Probable causes and corrections
Excessive noise and vibration
Main oil injection valve may be closed. Open valve.
Main oil injection valve may be open too far. Adjust.
Bearing damage or excessive wear. Contact Frick Factor or Frick service.
Slide valve/slide stop out of calibration (over- or undercompression)
Coupling loose on shaft. Tighten coupling. Replace if damaged.
If motor or compressor have been reinstalled, check that installation done according to 070.660-SM
Refrigerant flood-back. Correct system problem.
Slide valve and/or slide stop will not
move
4-way hydraulic control valve failed. Repair or replace.
Slide stop indicator rod stuck. Contact Frick Factor or Frick service for assistance.
Check both S.V. and S.S. feedback devices for wiring and resistance.
Compressor must be running with sufficient oil pressure.
Unloader piston stuck. Contact Frick Factor or Frick service for assistance.
Slipper seals worn out or damaged. Contact Frick Factor or Frick service for assistance.
Troubleshooting the demand pump system
Symptom
Probable causes and corrections
pump will not produce enough oil
pressure to start compressor
Check pump rotation.
Check that service valves are open.
Filter cartridges may be blocked. Check PSID across filters.
Strainer may be blocked. Clean.
Oil pressure regulator set too low or stuck open. Readjust or repair.
Pump worn out. Repair or replace.
Oil pressure rapidly drops
off when compressor starts
results in compressor
differential alarm
Main oil injection throttling valve too wide open or oil pressure
regulating valve improperly adjusted. Readjust both valves.
Oil pressure fluctuates
Liquid injection overfeeding or refrigerant flood back from system. Make
necessary adjustments or correc tions
Noise and vibration
Pump strainer blocked. Clean.
Liquid refrigerant overfeed. Adjust liquid injec tion.
Pump worn out. Repair or replace.
Grease leaks from vent port
in the side of the pump body
Normal leakage which will cease after initial operation. Black oil leaking
from this vent indicates oil seal wear or failure. If leakage exceeds normal allowable
rate of 7 drops per minute, replace seal.
Oil pressure drops as head
pressure increases
Normal behavior. Set main oil injection and oil pressure for maximum head
pressure condition.
Main filter psid is too high
Filters clogged with dirt. Replace.
Oil is too cold. Allow oil to warm up and check again.
Service valve on filter outlet is partially closed. Open valves fully.
NOTICE
Troubleshooting the compressor is limited to identifying the probable cause. If a mechanical problem is suspected
contact the Service Department. Do not attempt to disassemble the compressor.