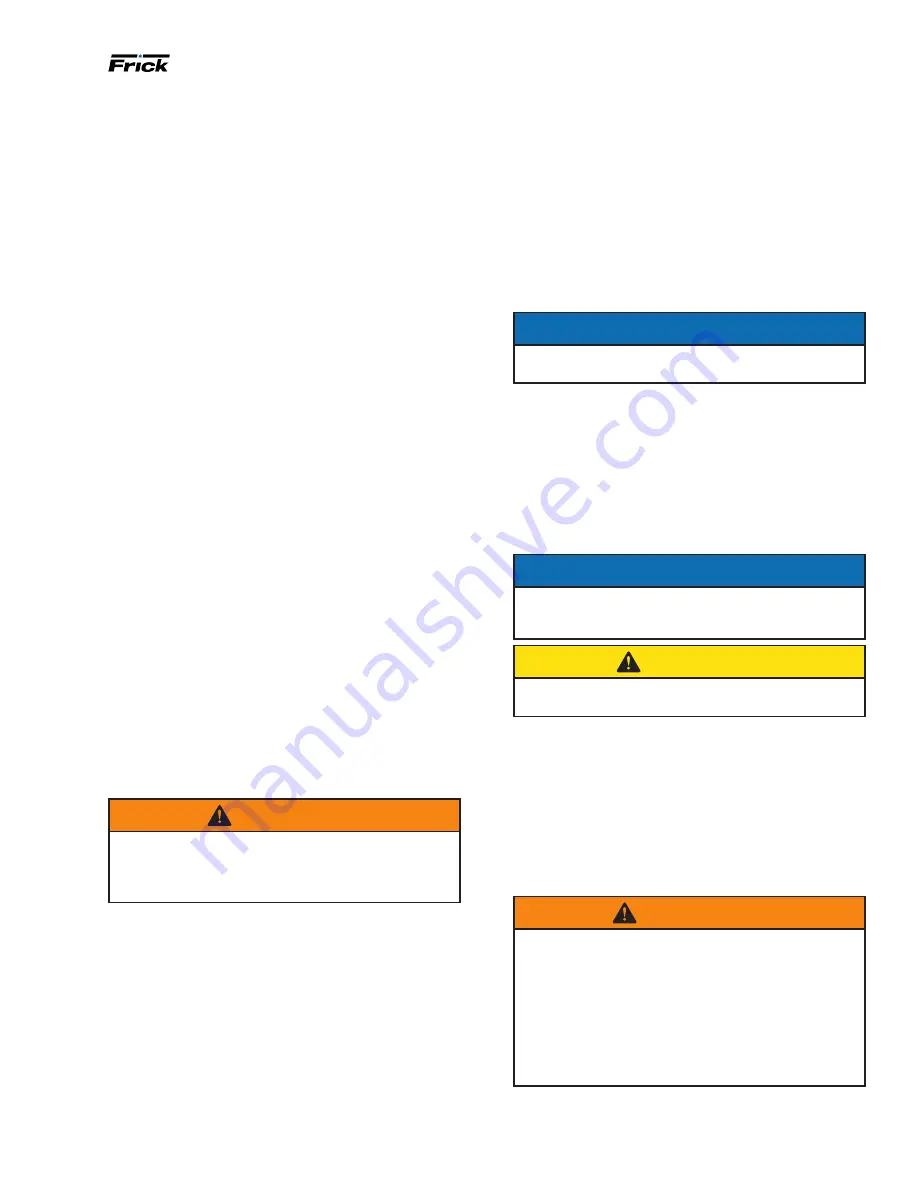
070.610-IOM (JUL 21)
Page 35
RWF II Rotary Screw Compressor Units
Maintenance
Replace the gasket and reinstall the canister cover. Torque
cover bolts first to finger tight, then 65 ft-lb, then 130
ft-lb.
7.
Evacuate (pull a vacuum on) the filter canister to elimi
-
nate non-condensibles.
8.
Fill the canister with new Frick
refrigeration oil as
needed.
9.
Open outlet service valve and leak test.
10.
Filter is ready to place in service.
Strainer – demand oil pump
To clean the demand oil pump strainer, the unit must be
shut down. The procedure is as follows:
1.
Push
[STOP]
key on microprocessor panel to shutdown
unit, then open disconnect switches for compressor and
oil pump motor starters.
2.
Close strainer inlet service valve.
3.
Open
drain valve located in the strainer cover and
drain oil into a container.
4.
Remove capscrews securing strainer cover, strainer
cover, gasket and element. Retain gasket.
5.
Wash element in solvent and blow clean with air.
6.
Wipe strainer body cavity clean with a lint-free clean
cloth.
7.
Replace cleaned element, gasket and reattach cover
using retained capscrews.
8.
Close drain valve and open strainer inlet service valve.
9.
Check for leakage.
10.
Close disconnect switches for compressor and oil pump
motor starters.
11.
Start the unit.
Strainer – liquid injection
To clean the
liquid injection strainer the unit must be shut
down. The procedure is as follows:
1.
Push
[STOP]
key on microprocessor panel to shut
down unit, then open disconnect switches for compressor
and oil pump motor starters.
2.
Close liquid supply service valve located before liquid
solenoid.
WARNING
Excessive pressure from expanding refrigerant
trapped between stop valve and solenoid may cause
gasket and O-ring failure and uncontrolled refrigerant
release.
3.
Close service valve located between the compressor
and the liquid injection thermovalve.
4.
Carefully loosen capscrews securing the
strainer cover
to the strainer. Allow pressure to relieve slowly.
5.
When all
entrapped refrigerant has been relieved,
carefully remove loosened capscrews (as liquid refriger-
ant is sometimes caught in the strainer), strainer cover and
strainer basket.
6.
Wash the strainer basket and cover in solvent and blow
clean with air.
7.
Reassemble strainer.
8.
Open service valve between compressor and liquid
injection thermovalve and check for leakage.
9.
Screw out manual solenoid valve stem.
10.
Carefully open liquid supply service valve.
11.
Leak test.
12.
Close disconnect switches for compressor and oil pump
motor starters.
13.
Start unit.
Coalescer filter element
When changing the coalescer filter element(s) it is recom-
mended that the oil be changed, cartridge(s) in oil filters
OF-1 and OF-2 if applicable be changed and the following
applicable strainer elements be removed and cleaned.
NOTICE
Use of
filter elements other than Frick may cause
warranty claim to be denied.
1.
, Steps 1 through 8.
2.
Loosen
manway cover retainer bolts, remove retainers,
manway cover and cover gasket. Discard cover gasket.
3.
Remove and retain nut securing coalescer filter re
-
tainer.
4. Remove retainer, coalescer filter element and 2
O-rings. Discard filter elements.
5.
Install new coale
scer filter element(s).
NOTICE
Frick SuperCoalescer
™
element (with drain feature) must
be installed with the "DRAIN DOWN" tag on the bottom
at the 6 o'clock position.
CAUTION
Seat element in center of locating tabs on separator
bulkhead.
6.
Replace coalescer filter retainer and nut. Tighten the
nut to 21 ft-lb torque.
Do not overtighten nut. Excessive
torque can damage the element and result in oil car-
ryover.
Install jam nut and tighten.
7.
Install new manway gasket and replace manway cover.
8.
While unit is at atmospheric pressure, tighten the two
12 in. x 16 in. elliptical head
manway bolts to 180 ft-lb.
9. Ensure manway bolts remain finger tight after the
compressor unit is in operation, as the manway bolts
will loosen as a result of pressurization.
WARNING
Overtightening components could result in a fire,
serious injury or property damage.
Do not apply the manway bolt torque specified for
an unpressurized unit while the unit is pressurized.
Applying this torque when the manway is pressur-
ized can overstress the manway gasket. Overstressing
the gasket can lead to gasket failure and/or a system
leak.
Trained technicians are required for servicing.
10.
See
,
Steps 9 through 14.