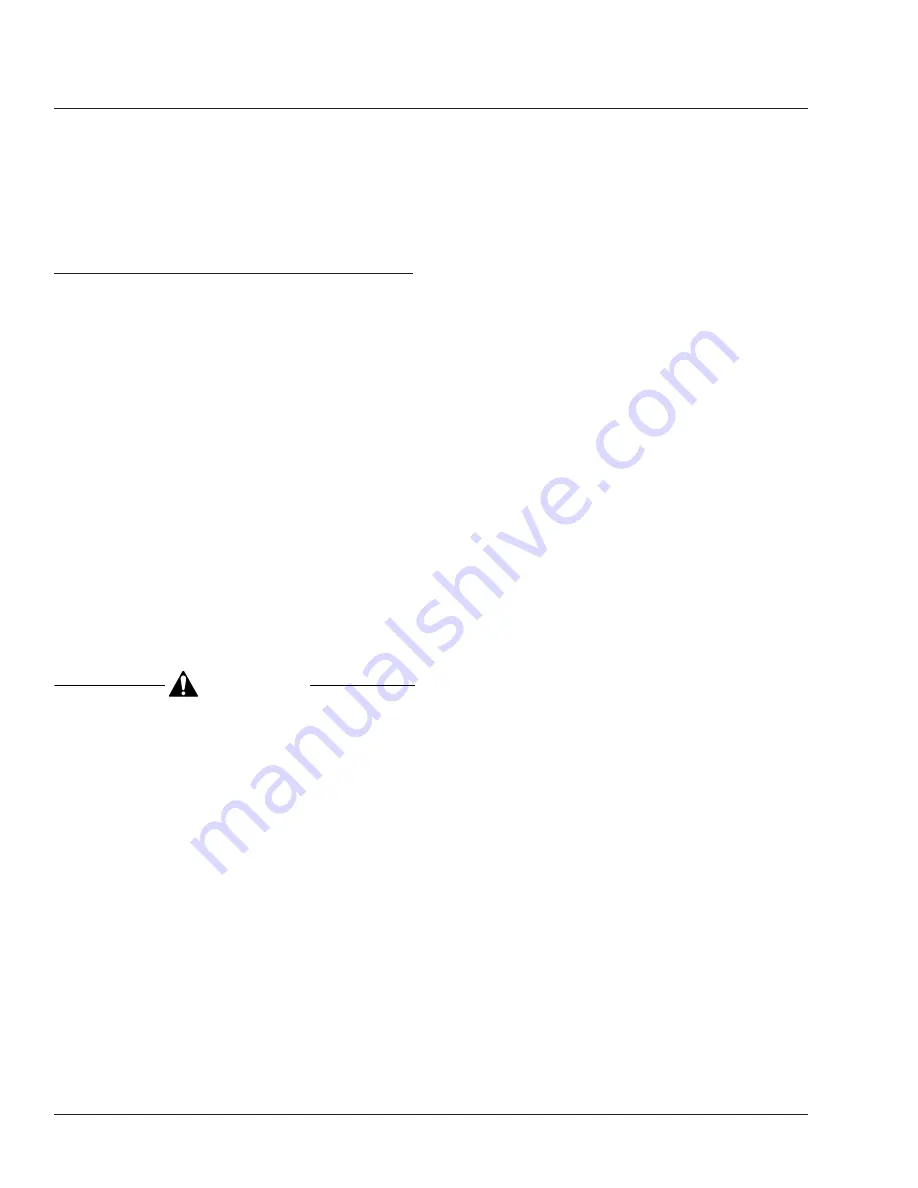
35–02 Axle Lubricant Changing
and Magnetic Plug
Cleaning
A regular schedule for changing the axle lubricant in
a particular vehicle and operation can be accurately
determined by analyzing oil samples taken from the
axle at specified intervals or mileages. Lubricant sup-
pliers frequently make their laboratory facilities avail-
able for determining the useful life of their product
under actual service conditions. The final schedule
that is recommended may, for economic reasons, be
correlated with lubricant changes that are governed
by climatic conditions and magnetic plug mainte-
nance. Change lubricant type and viscosity as cli-
matic temperatures demand, regardless of vehicle
mileage or established change schedule.
The normal operating temperature of compounded
lubricants during the summer season is about 160°
to 220°F (71° to 104°C). The chemicals and addi-
tives that give these lubricants increased load-
carrying capacity, oxidize faster at temperatures
above 220°F (104°C), contributing to more rapid lu-
bricant deterioration. For this reason, lubricants of
this type, that operate continuously at high tempera-
tures, must be changed more frequently.
CAUTION
Failure to change the axle lubricant at more fre-
quent intervals, when adverse operating condi-
tions require, could result in axle damage.
Alliance Brand Product (ABP) Axle
1.
Remove the filler plug, then the drain plug (in the
center bottom of the axle housing), and allow the
differential to drain completely.
2.
Install the drain plug and tighten it securely.
3.
Fill the differential with 80/90 hypoid gear oil
through the rear axle fill hole. See
for
axle lubricant capacities.
NOTE: A normal oil change does not include the
hubs. Drain the differential and add 5.8 qts. (5.5
L) of SAE 80/90 hypoid gear oil through the rear
axle fill hole. The lubricant level should be at the
bottom of the fill hole.
IMPORTANT: The entire axle capacity (axle
completely dry) is 7.4 qts. (7 L). Each hub con-
tains 0.80 qt. (0.75 L) of lubricant. To protect the
outer bearings from oil starvation, jack up (ar-
ticulate) each side of the axle a minimum of 4
inches (10 cm) to ensure that oil flows to the
outer bearings. Articulate the short-side arm for
45 seconds and the long-side arm for 90 sec-
onds. After articulating the axle, add 0.80 qt.
(0.75 L) of lubricant through the fill hole (in addi-
tion to the 5.8 qts. [5.5 L] of a normal oil
change) for each hub that has been removed.
Check the oil level again and ensure that the
axle is neither under nor overfilled.
4.
Install the fill plug and tighten it securely.
Meritor Axle
Axle Draining and Flushing
1.
Remove the plug at the bottom of the housing
and drain the lubricant while the unit is warm.
Allow enough time for all of the old lubricant to
drain completely.
2.
Flush the unit with clean flushing oil, then drain it
completely.
IMPORTANT: Do not flush axles with solvent,
such as kerosene.
3.
Clean the drain plugs. For magnetic drain plugs,
a piece of key stock or any other convenient
steel slug may be used to short the two magnetic
poles and divert the magnetic field.
NOTE: Meritor recommends using magnetic
plugs with elements having a minimum pickup
capacity of 2 pounds (1 kg) of low-carbon steel,
in plate or bar form. Magnets will rapidly lose
effectiveness as collected material bridges the
gap between the two poles. Clean or change
the plugs before this occurs. It may be neces-
sary to clean or change the plugs one or more
times between lubrication change intervals.
4.
After cleaning the drain plugs, install and tighten
them 35 lbf·ft (47 N·m).
Rear Axle
35
School Bus Chassis Maintenance Manual, July 2003
35/2