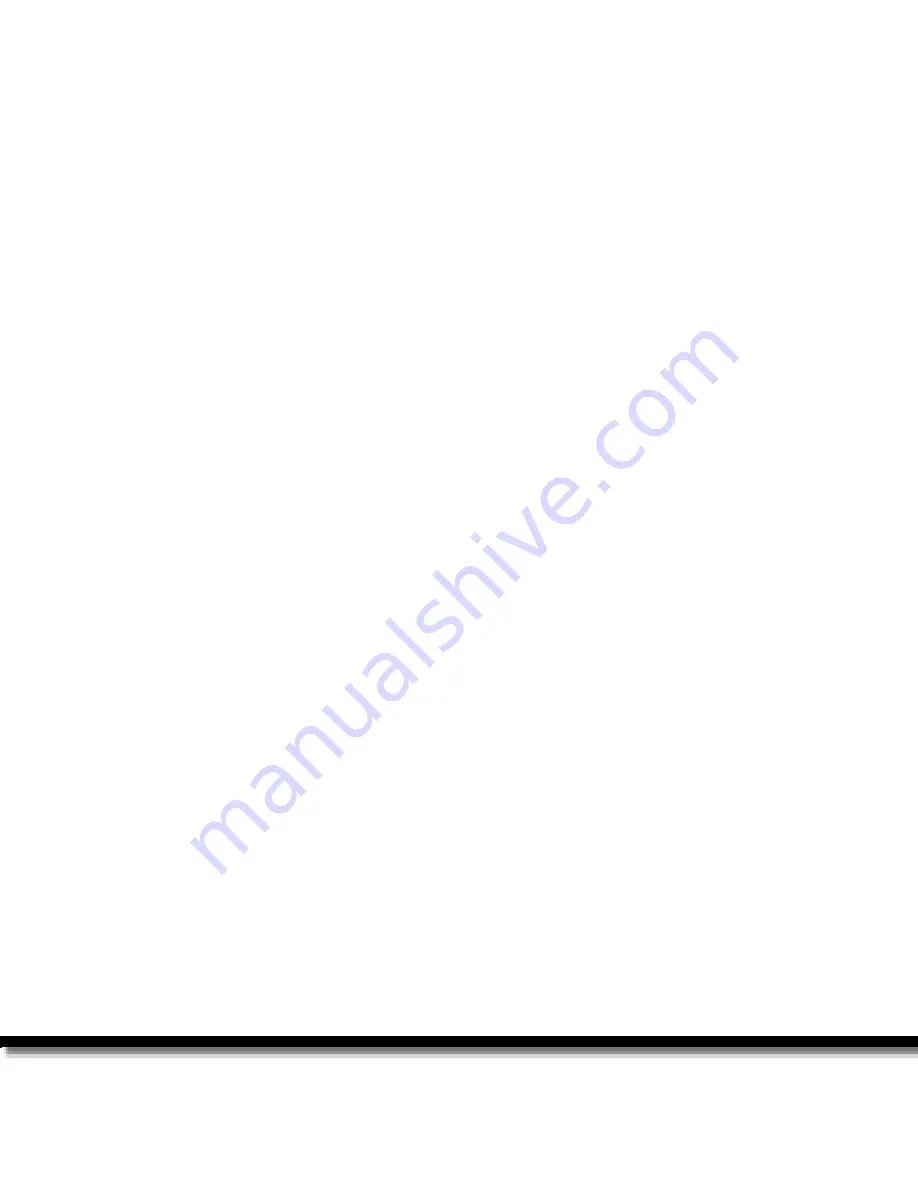
FRANKLIN
MANUFACTURING CORPORATION
Reprinted by AFM Engineering, Inc. -1- Phone 714.547.0194
1313 E. Borchard Ave.
Fax 714.542.2728
Santa Ana, CA 92705 Email [email protected]
MODEL 8000 and 5000
SERIES (Linear Wedge Drive Machines)
OPERATING INSTRUCTIONS
HOT STAMPING MACHINES