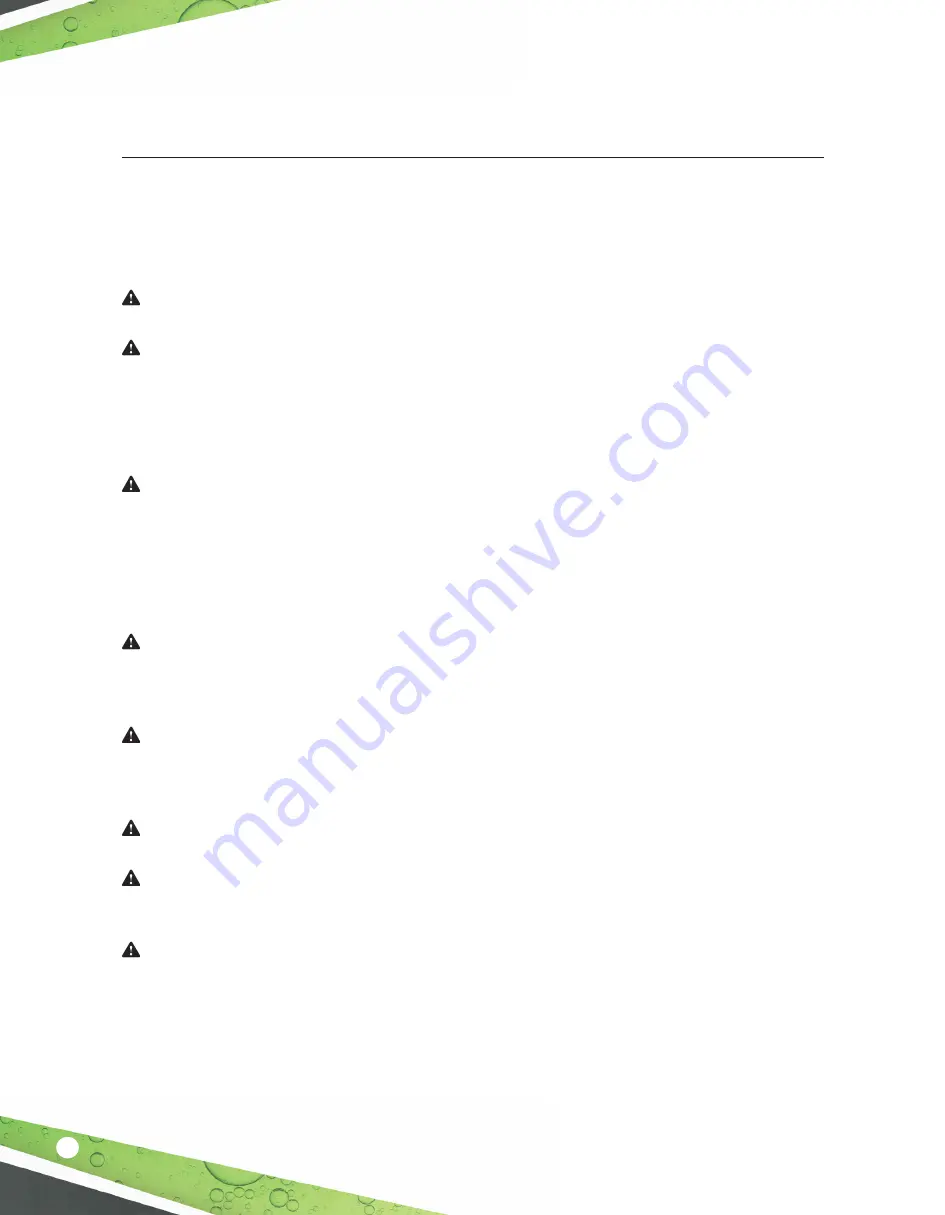
2
Operating precautions
Franklin Fueling Systems (FFS) equipment is designed to be installed in areas where volatile
liquids such as gasoline and diesel fuel are present. Working in such a hazardous environment
presents a risk of severe injury or death if you do not follow standard industry practices and the
instructions in this manual. Before you work with or install the equipment covered in this manual,
or any related equipment, read this entire manual, particularly the following precautions:
CAUTION
: Use only original FFS parts. Substituting non-FFS parts could cause the device to
fail, which could create a hazardous condition and/or harm the environment.
WARNING
: Follow all codes that govern how you install and service this product and the
entire system. Always lock out and tag electrical circuit breakers while installing or servicing
this equipment and related equipment. A potentially lethal electrical shock hazard and the
possibility of an explosion or fire from a spark can result if the electrical circuit breakers are
accidentally turned on while you are installing or servicing this product. Refer to this manual (and
documentation for related equipment) for complete installation and safety information.
WARNING
: Before you enter a containment sump, check for the presence of hydrocarbon
vapors. Inhaling these vapors can make you dizzy or unconscious, and if ignited, they can explode
and cause serious injury or death. Containment sumps are designed to trap hazardous liquid
spills and prevent environmental contamination, so they can accumulate dangerous amounts
of hydrocarbon vapors. Check the atmosphere in the sump regularly while you are working in
it. If vapors reach unsafe levels, exit the sump and ventilate it with fresh air before you resume
working. Always have another person standing by for assistance.
WARNING
: Follow all federal, state, and local laws governing the installation of this product
and its associated systems. When no other regulations apply, follow NFPA codes 30, 30A, and 70
from the National Fire Protection Association. Failure to follow these codes could result in severe
injury, death, serious property damage, and/or environmental contamination.
WARNING
: Always secure the work area from moving vehicles. Reduced visibility puts service
personnel working in danger from moving vehicles that enter the work area. To help prevent
this safety hazard, secure the work area by using a service truck (or some other vehicle) to block
access.
WARNING
: Before you install the equipment, discharge static electricity from it to ground,
and make sure the equipment is properly grounded while in service.
WARNING
: Make sure you check the installation location for potential ignition sources such as
radio waves, ionizing radiation, and ultrasound sonic waves. If you identify any potential ignition
sources, you must make sure safety measure are implemented.
WARNING
: To avoid an electrical hazard that could create a risk of severe injury or death,
always make sure both power supplies (120-240 VAC hook and 200-250 VAC input) are
disconnected before anyone installs or services the equipment.
Содержание GUARDIAN SPGC-220.
Страница 1: ...GUARDIAN SERIES TM SINGLE PHASE CONTROLLER INSTALLATION GUIDE...
Страница 8: ...4 Intentionally Blank...
Страница 31: ...27 SPGC 220 StandAlone wiring diagram...
Страница 32: ...28 SPGC 220 Primary Secondary wiring diagram...
Страница 33: ...29 SPGC 220Alternating Circuit wiring diagram...
Страница 34: ...SPGC 220 Primary Secondary Alternating Circuit wiring diagram...
Страница 35: ...SPGC 220 replacement parts Lower power relay board Part 225005932 Upper control user input board Part 225000932...
Страница 36: ...223987103 r3...