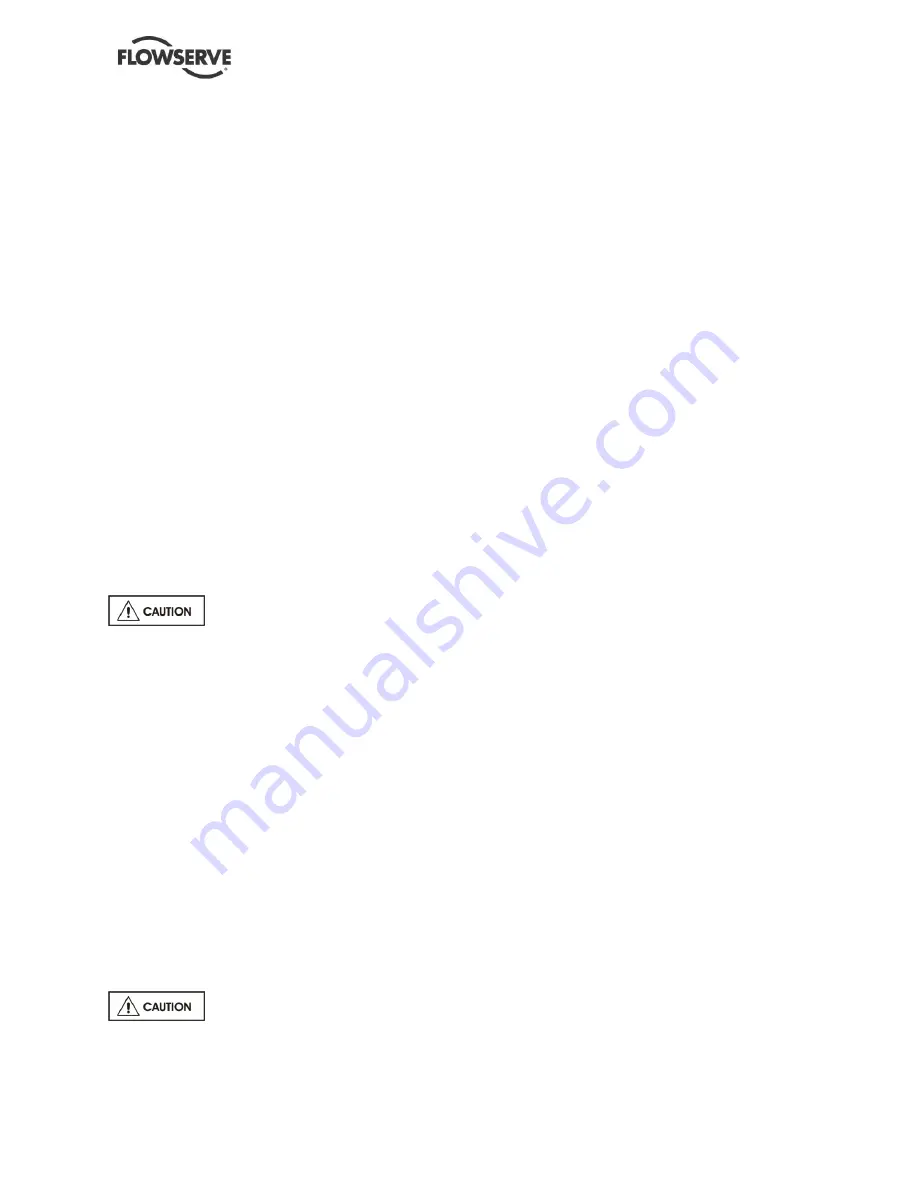
WIK USER INSTRUCTIONS ENGLISH BO2662 5/09
Page 59 of 76
table; total runout shall not exceed
maximum given in section 10.3.
8) Install new wear ring locking keys [6700.3] and
tack weld them to metal of parent part using
gas-tungsten arc and appropriate wire. Note:
some installations use interference fit only to
secure ring. Then repeat step 7.
9) If the replacement bushing [1610] has been
furnished with finish stock left on the running
surface, true cut the bushing [1610] using the
following procedure, or an equivalent:
a) Center the parent part on a vertical lathe
by following steps 7a through 7c above.
b) Machine the finish stock from the inside
diameter of the bushing [1610] to meet the
clearances specified in section 10.3.
10) Verify trueness of bushing-to-part fit as
outlined in step 7 above.
11) See that there is no damage to the bushing
surface.
6.8.2.7.9
Replacing Impeller Wearing Rings
Unless the impeller skirt wearing surface has been
ground down, the standard size wearing ring
should be used for replacement. To replace an
impeller wearing ring [2300] proceed as follows:
Striking or cutting into parent metal
of impeller will make replacement necessary.
1) Remove wearing ring retainers:
a) Machine off or using rotary file grind off,
tack welds that hold wear rings [2300] to
impeller [2200].
b) If tack welds were used machine or grind
off welds.
2) Block or suspend impeller face down. Apply
heat to ring only, evenly and quickly, using a
torch with a Rosebud head. The wear ring
[2300] will normally fall off. If not, tap wear ring
[2300] off or use two pry bars at diametrically
opposite points and pry it free of impeller
[2200]. Alternately, wear ring [2300] can be
machined off impeller [2200].
3) See that requirements under visual inspection
(section 6.8.2.7.1) above, which apply to
impeller wearing rings [2300], are complied
with for the new ring.
Do not bind or otherwise cause
undue stress on wearing rings [2300].
4) Determine that impeller [2200] has cooled to
ambient temperature by feeling with hand then
heat wearing ring as described in step 2 until
ring will slip into place on skirt.
5) If the replacement wearing ring [2300] has not
been furnished with finish stock left on the
running surface, then verify trueness of
wearing-ring-to-impeller fit as outlined below
or by an equivalent technique:
a) Set impeller [2200] face down on table of
vertical lathe and parallel with face of table.
b) Align centerline of part with centerline of
table using register face of part as true
side of dial indicator; alignment shall be
within limit given in section 10.3.
c) Clamp around part to hold it in centered
and parallel position.
d) Set up dial indicator to run on outside
diameter of wearing ring [2300] and rotate
table; total runout shall not exceed
maximum given in section 10.3.
6) Install new retainer and tack weld them to
metal of parent part using gas-tungsten arc
and appropriate wire. Note: some installations
use interference fit only to secure wear ring
[2300]. Then repeat step 7.
7) If the replacement wearing ring [2300] has
been furnished with finish stock left on the
running surface, true cut the wearing ring
using the following procedure, or an
equivalent:
a) Center the parent part on a vertical lathe
by following steps 7a through 7c above.
b) Machine the finish stock from the outside
diameter of the wearing ring [2300] to
meet the clearances specified in section
10.3.
8) Verify trueness of wearing-ring-to-part fit as
outlined in step 7 above.
9) See that there is no damage to the wea ring
[2300] surface.
6.9
Pump Assembly
6.9.1 Internal Assembly
To assemble the internal assembly, proceed as
follows:
6.9.1.1
Interference Fit Part Installation
To install an interference fit part, proceed with the
following general procedure:
1) Before installing part, ensure that:
a) The shaft [2100], impeller [2200] and
sleeve [6230] bores, split rings [2531], and
keys [6700] are kept clean and smooth:
scratched surfaces or dirt increase the
chance of parts seizing
b) Temperature of shaft [2100] is kept within
11°C (20°F) of ambient temperature by