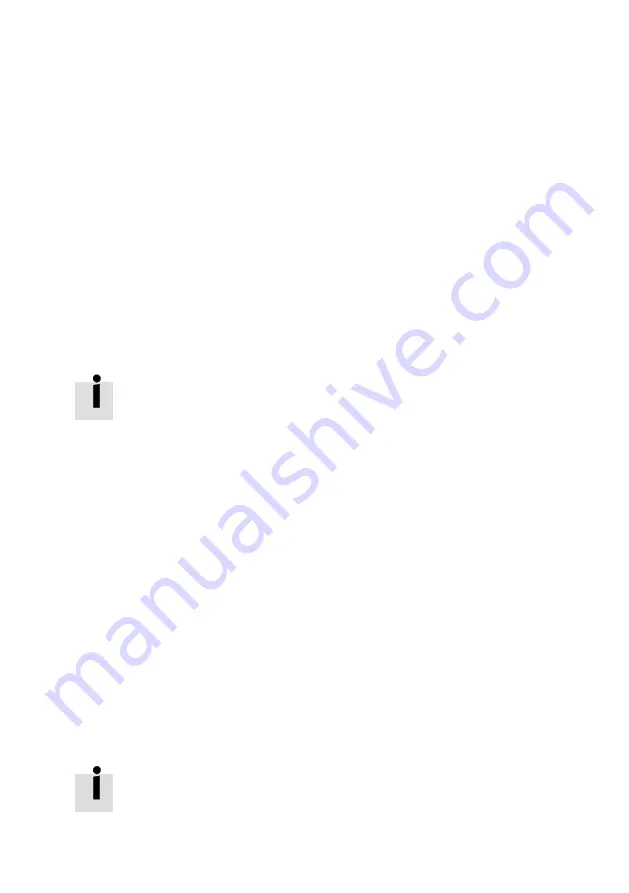
4
Commissioning with the FCT
Festo – EXCM-30/-40-...-PF-EN – 1603 – English
35
4.4.2
Gantry
1. Enter all required values.
Dimension system
2. Choose a coordinate system by determining the position of the axis zero point
(
è
3. Specify the project zero point and the SW end positions (positive/negative) of both axes
(
è
Homing
4. Enter all required speed and acceleration values.
4.4.3
Controller
1. Select in the [Project] [Component] menu the entry [Controller].
Here, the firmware version and network settings of the connected CMXH are visible in the online
mode. The network settings can be adjusted as needed (
è
Fieldbus
This page is only visible if CANopen or SCE have been selected as the control interface.
Control interface CANopen:
Select the bit rate
Specify the node number (range of values 1 … 127, default: 1)
Control via Ethernet (CVE) control interface:
Determine the port, if necessary (range of values 1 … 65535, default: 49700)
4.5
Settings of the operating parameters
4.5.1
Record Table
The parameters of positioning jobs are created via the FCT and saved in a record table in the form of
records. A record table consists of a maximum of 31 records.
The records are selected individually in the “Record selection” operating mode using the record num
ber.
Each record consists of the following parameters:
– Record type: Positioning absolute (PA), relative to the setpoint position (PRN) or relative to the
actual position (PRA)
– Target position X and target position Y
– Speed, acceleration and jerk
– Comments (optional)
Records are parameterised exclusively via the Festo Configuration Tool (FCT).