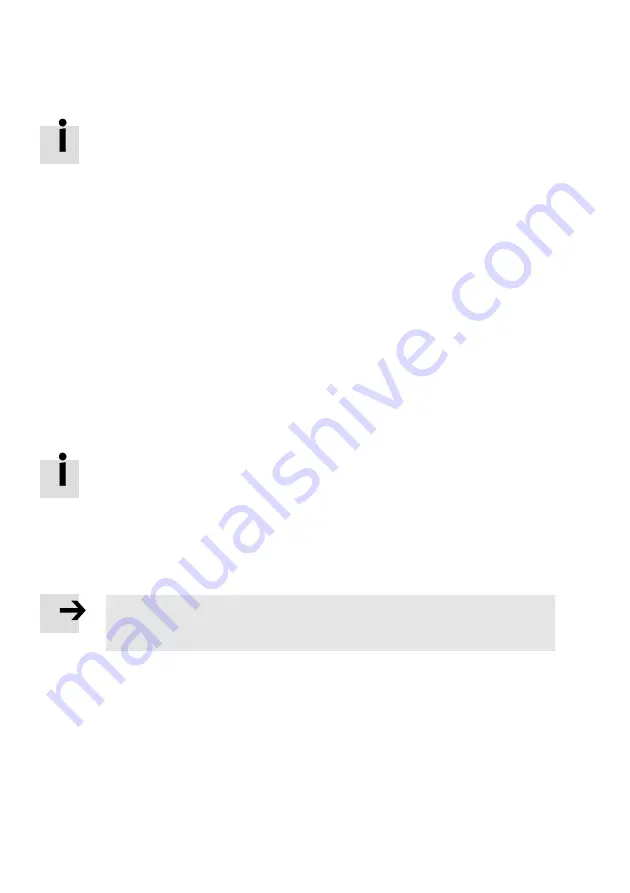
2
Overview
12
Festo – EXCM-30/-40-...-PF-EN – 1603 – English
2.5.2
Safety function Safe Torque Off - STO
The safety function STO (“Safe Torque Off ”) is described in detail in the document
“CMXH description STO” and may only be used in the manner described there.
(
è
Tab. 1.2 Documentation for the system EXCM-30/-40 with CMXH)
The safety function enables two-channel shut-down of the voltage supply to the motors connected to
the CMXH and therefore a safely switched-off torque (Safe Torque Off, STO) via the connection [X4].
Two channels are achieved through the inputs STO1 and STO2. The power supply to the motor is se
curely interrupted through shut-down of the output stage. At the same time, the brake control is activ
ated.
2.6
Drive functions
2.6.1
Jogging
During jogging, the slide of the planar surface gantry moves as long as a corresponding signal is
present. Jogging can always take place only in one direction, either in the direction of the X-axis or in
the direction of the Y-axis, whereby differentiation is made between creeping run and normal run. The
CANopen or Ethernet interface can be used as a control interface, but the I/O interface cannot.
This function is normally used to run the slide manually into a defined basic position.
As long as a valid reference point has not been reached, the software end positions are
deactivated and the slide can also be positioned behind the software end positions
through jogging.
2.6.2
Homing
In homing, the reference point of the dimension system is determined. The reference point is the abso
lute reference point for the axis zero point. Orders can only be started if homing has been completed
successfully (exception: jogging).
Note
The reference point is saved temporarily in the controller. When there is an open circuit
in the logic power supply, the homing point is lost.
Homing can be started through selection of record 0 or through the control byte CPOS
(
è
5.2.2 Description of the control bytes CCON/CPOS) and always takes places to the stop at the
origin of the selected coordinate system (
è
2.8.2 Selection of the coordinate system). The stop is
detected by a motor standstill in combination with a sharp rise in the motor current. After the fixed
stop is reached, a movement to zero is automatically performed in order to reach a permanently
defined and unchangeable minimum distance from the mechanical stop.