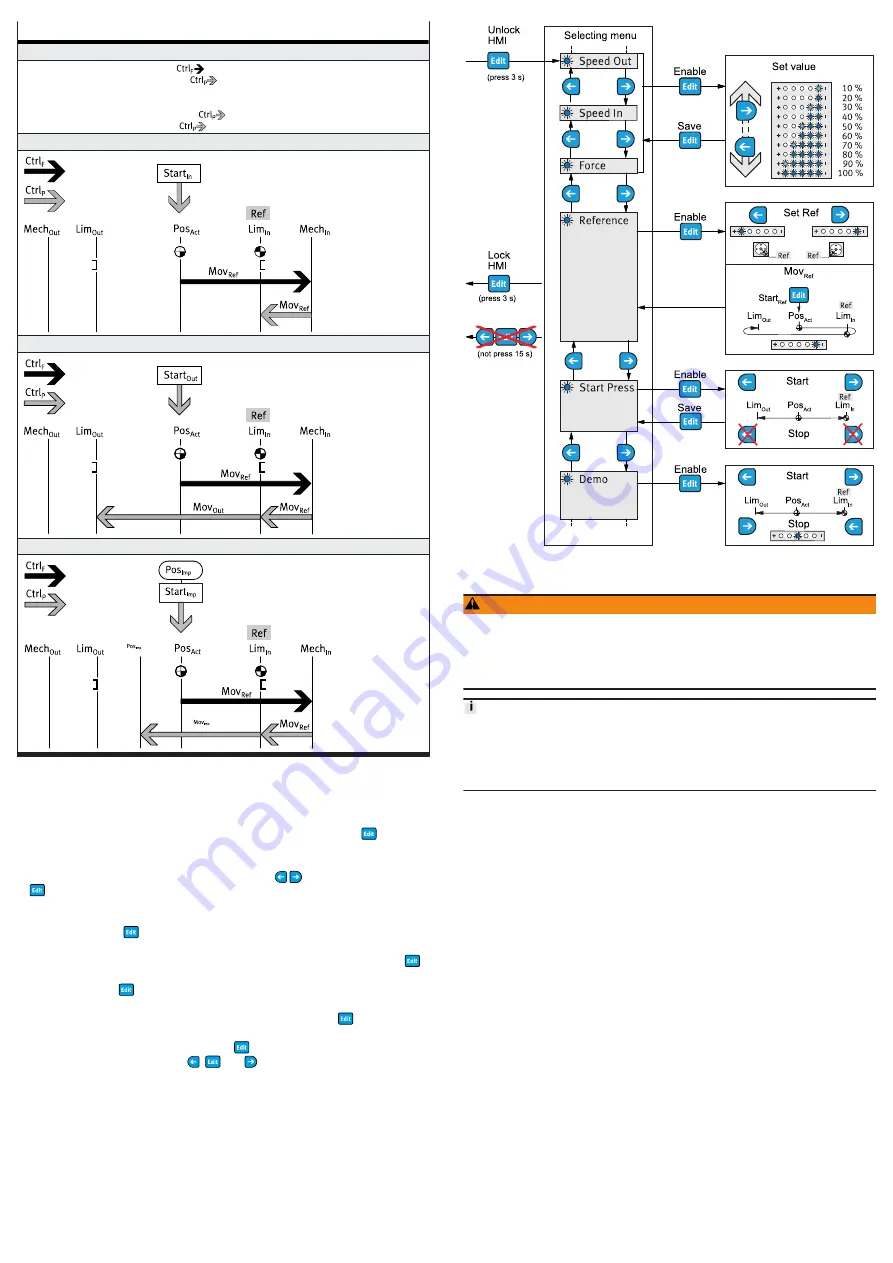
Homing after a restart as a function of the positioning task
Sequence
–
Mov
Ref
: force-controlled movement
against mechanical stop "Mech
In
"
–
Mov
Out
: position-controlled movement
to the reference end position "Ref"
–
Travel to the target position as a function of the positioning task
–
No travel, end position "Lim
In
" reached
–
Mov
Out
: position-controlled movement
to the end position Lim
Out
–
Mov
Imp
: position-controlled travel
to the intermediate position Lim
Imp
(IO-Link only)
Start
In
positioning task to the end position Lim
In
Start
Out
positioning task to the end position Lim
Out
Start
Imp
positioning task to the intermediate position Pos
Imp
(IO-Link only)
Tab. 9: Initialise restart sequence with reference end position "Ref"
9.4
Display and operating components (HMI)
The display and operating components (HMI) can be used to perform the fol-
lowing functions in the HMI menu:
–
Unlock pushbutton actuators (Unlock HMI), press and hold for 3 s
— an
active positioning task in DIO or IO-Link mode is stopped
(Condition for IO-Link operation: IO-Link parameter 0x000C.4 = false)
–
Select menu function with pushbutton actuators (selecting menu), press
–
Parameterise Speed Out, Speed In and Force setpoint values
(Set value: 10, 20, ..., 100% of the maximum value
save (Save), press
–
Parameterise the position of the reference end position "Ref" (Set Ref) and run
the referencing movement Mov
Ref
(Start
Ref
: Pos
Act
è
Lim
In
è
Lim
Out
), press
–
Run Start Press movement (Start/Stop) and save Start Press Position Pos
Start
Press
(Save), press
–
Execute demo run (Start/Stop)
–
Lock pushbutton actuators (Lock HMI), press and hold for 3 s
or no push-
button actuator input for 15 s
–
To acknowledge an error, press and hold
for 3 s
–
Reset to factory settings, press ,
and simultaneously for 10 s and then
carry out a Power OFF/ON on the logic power supply 24 V DC [pin 1].
Fig. 7: HMI menu
9.5
Homing with end position determination
WARNING
Risk of injury due to unexpected movement of components.
When starting the homing run, the drive is disconnected from the power supply
for a short time. This can cause unexpected movements of the connected
mechanics and crush parts of the body.
• Bring moving parts of the connected mechanical system into a safe position.
• Referencing with end position determination is only required again if the refer-
ence end position "Ref" or the useful range needs to be changed.
• During referencing with end position determination the intermediate position
Pos
Imp
and the start press position Pos
Start Press
is set equal to the new end
position Lim
Out
.
During referencing with end position determination the positions of the mechan-
ical stops Mech
In
/Mech
Out
are recorded in order to calculate the end positions
Lim
In
("Ref")/Lim
Out
for the dimension reference system.
Before running referencing with end position determination to a new reference
end position "Ref", the drive is de-energised for a required re-initialisation. Then
the power is restored and the process is started.