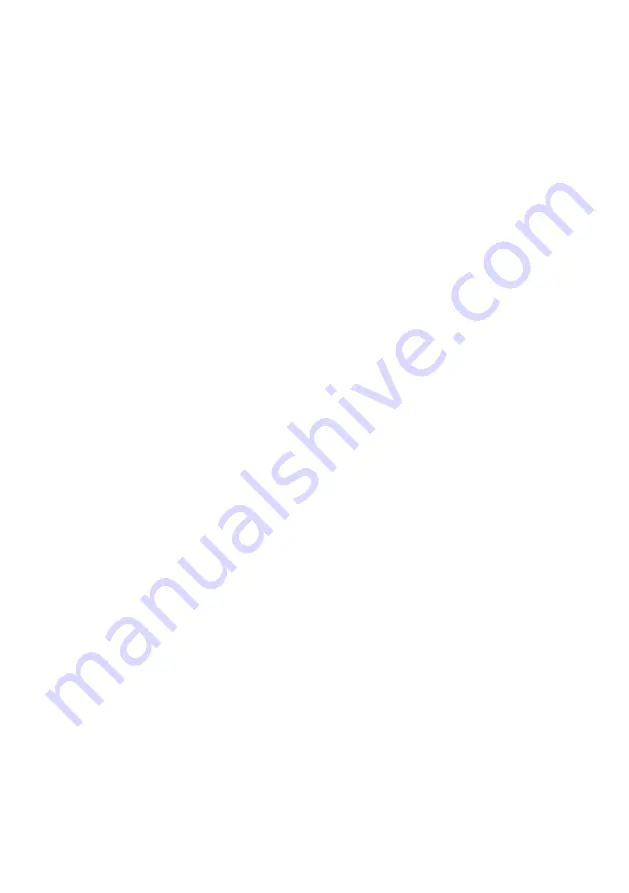
–
The maximum permissible cable length between the safety relay unit and the connector of the I/O
interface is 3 m.
–
During installation, fulfil the requirements of the EN 60204-1. In case of error, the voltage must
not be greater than 60 V DC. The safety relay unit must switch off its outputs in case of error.
–
Carry out wiring between the safety relay unit and the I/O interface of the servo drive so that both
a short circuit between the conductors or to 24 V as well as a cross circuit are excluded
è
EN 61800-5-2, Table D.3.1. Otherwise, the safety relay unit must plan for a cross circuit detec-
tion and, in case of error, switch off the control signals in 2 channels.
–
Use only suitable counter plugs and connection cables
è
textvar object does not exist.
–
Avoid conductive pollution between neighbouring plug pins.
–
Make sure that no bridges or the like can be inserted parallel to the safety wiring. For example,
use the maximum wire cross section of mm or appropriate wire end sleeves with plastic collars.
–
To cross wire safety-relevant inputs and outputs, use twin cable end sleeves. In case of cross wir-
ing by inputs and outputs, a maximum of 10 devices may be cross-wired
è
textvar object does
not exist.
–
The safety relay unit and its inputs and outputs must meet the required safety classification of the
respectively required safety function.
–
Connect each of the control inputs in 2 channels with parallel wiring directly to the safety relay
unit.
–
Use only permitted motor cables for the connection BR+/BR– .
–
If the diagnostic output of the used safety functions has to be evaluated: Connect diagnostic out-
put directly to the safety relay unit. The evaluation of the diagnostic output is required or option-
al, dependent on the desired safety classification.
–
If a cross wiring of diagnostic outputs is performed for a device compound: Wire diagnostic out-
puts as a ring. Guide the two ends of the ring to the safety relay unit and monitor for discrepancy.
Basic concept of the wiring
–
Safe sensors, e.g. emergency stop switches, light curtains, are guided to the safety relay unit (or
the safety PLC).
–
The safety relay unit queries the safety functions at the servo drive through 2 channels and evalu-
ates the related feedback signals.
–
It is not permitted to connect sensors, e.g. emergency stop devices, directly to the servo drive
because no sensor monitoring takes place.
5.2
Installation STO
Inputs and outputs for the STO safety functions
The 2-channel request of the safety function is made over the digital inputs #STO-A and #STO-B. The
STA diagnostic output displays whether the safe status has been reached for the STO safety functions.
Installation
22
Festo — CMMT-AS-...-S1 — 2018-02