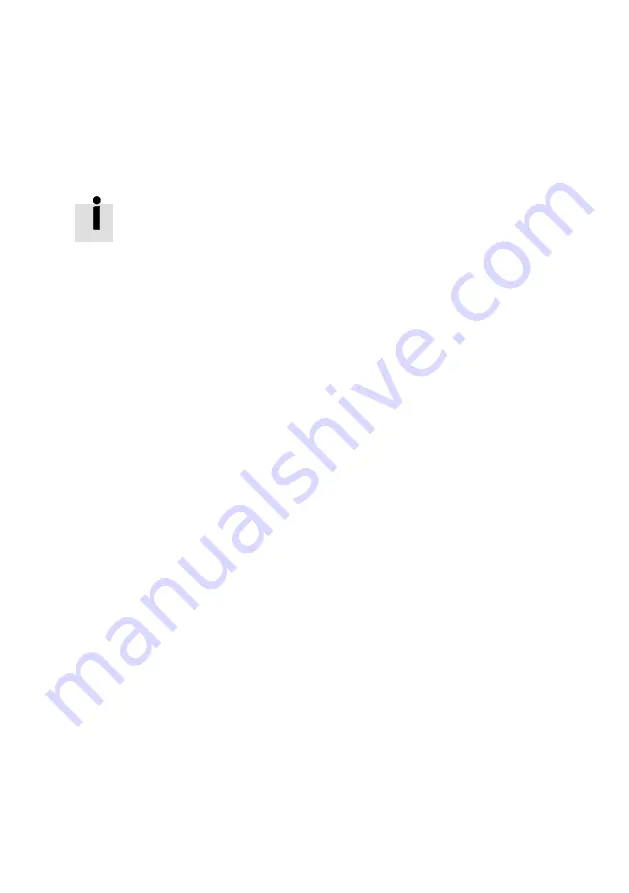
5
Setting parameters
Festo – GDCP-CMMP-M3/-M0-C-CO-EN – 1510b – English
75
5
Setting parameters
Before the motor controller can carry out the desired task (torque regulation, speed adjustment,
positioning), numerous parameters of the motor controller must be adapted to the motor used and the
specific application. The sequence in the subsequent chapters should be followed thereby. After set
ting of the parameters, device control and use of the various operating modes are explained.
The display of the motor controller shows an “A” (Attention) if the motor controller has
not been parametrised appropriately yet. If the motor controller is supposed to be para
metrised completely over CANopen, you must write over the object 6510
h
_C0
h
in order to
suppress this display (
Besides the parameters described in depth here, the object directory of the motor controller contains
other parameters that have to be implemented in accordance with CANopen. But they normally do not
include any information that can be used in designing an application with a motor controller
CMMP‐AS‐...‐M3/-M0 in a sensible way. If required, read about this in the specifications of CiA.
5.1
Loading and Saving Parameter Sets
Overview
The motor controller has three parameter sets:
–
Current parameter set
This parameter set is located in the volatile memory (RAM) of the motor controller. It can be read
and written on as desired with the parametrisation software or via the CAN bus. When the motor
controller is switched on, the application parameter set is copied into the current parameter set.
–
Default parameter set
This is the parameter set of the motor controller provided standard by the manufacturer and is
unchangeable. Through a write process into the CANopen object 1011
h
_01
h
(restore_all_default_parameters), the default parameter set can be copied into the current
parameter set. This copying process is only possible when the output stage is switched off.
–
Application parameter set
The current parameter set can be stored in the non-volatile flash memory. The storage process can
be triggered with a read access to the CANopen object 1010
h
_01
h
(save_all_parameters). When the
motor controller is switched on, the application parameter set is automatically copied into the cur
rent parameter set.