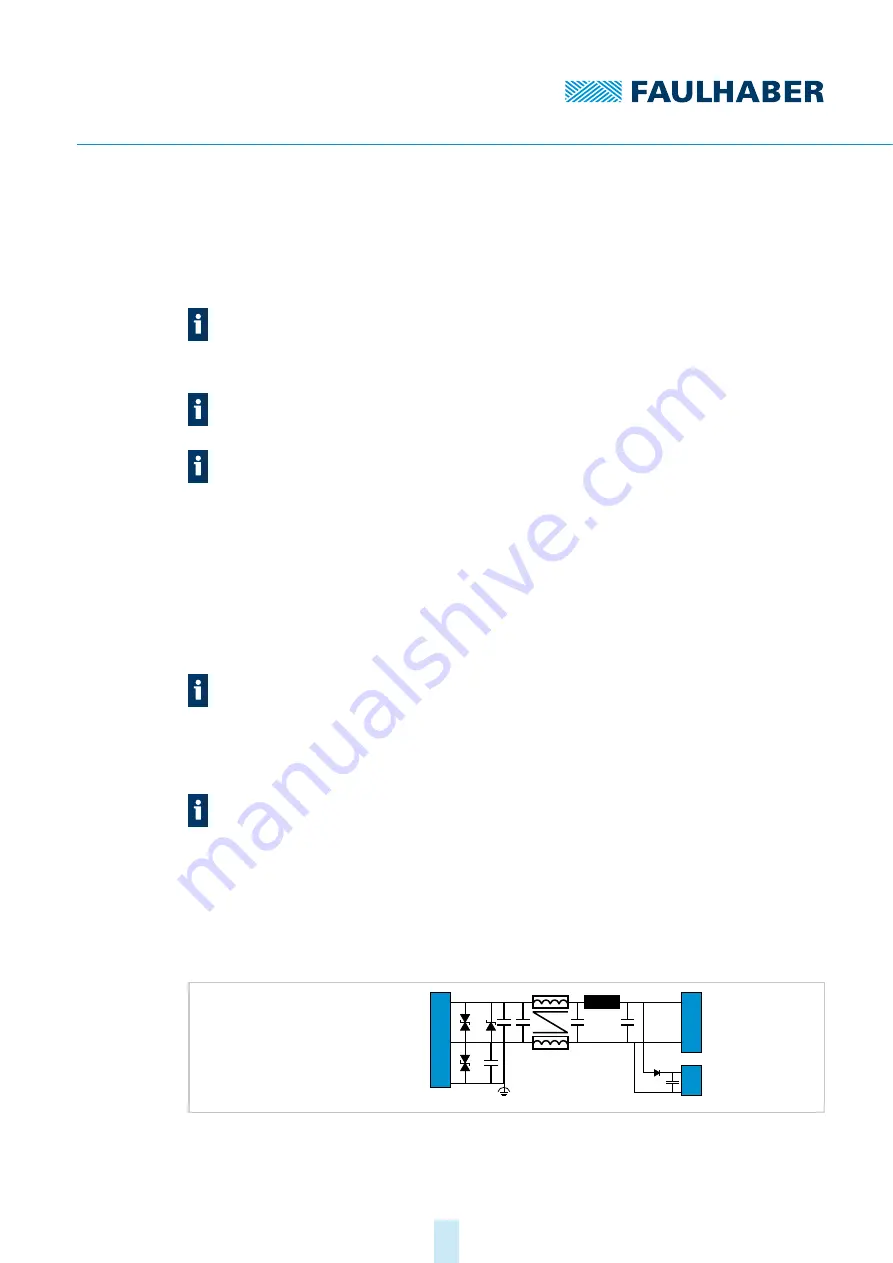
1st edition, 12.02.2021
7000.05071, 1st edition, 12.02.2021
7000.05071
Installation
73
4.3.5.1
Analogue sensors and analogue Hall sensors
Where possible, shield analogue sensor cables and lay them apart from (shielded)
motor cables.
Connect the shield on one end, ideally on the motor side.
4.3.5.2
Incremental encoders / Digital Hall sensors / Digital sensors
4.3.5.3
Encoders with absolute interface
Connect the shield of the encoder lines on both ends.
On the controller side near the encoder plug connector, a terminal resistance of 120
Ω
is
highly recommended between Data+ and Data–. Depending on the version, terminating
resistors are present on the motherboards and can be activated via DIP switch S2.
Alternatively, a so-called split termination can be used instead of the 120
Ω
to increase the
interference resistance. See also technical manual AEMTL (manual no. 7000.0x070).
4.3.6
Using filters
The filters are divided into various function and current ranges.
Filter types:
Input-side filters: filters on the power supply side
Motor-side filters: filters that are connected between controller and motor in the motor
phases
Fig. 33: Filter categories from FAULHABER
The signal quality can be improved with a capacitor (470 nF, dielectric strength > 100 V)
between device shield and sensor supply (+5 V).
Due to the increased signal hysteresis, digital Hall sensors are more robust than ana-
logue Hall sensors.
Incremental encoders are robust due to a four-edge evaluation in the controller.
In the case of an absolute encoder interface, signal interference immediately results in
invalid position values during the interference. A more interference-immune, differen-
tial data transmission is therefore advantageous.
Further information on the layout and design of passive filters is available on request.
EFS 3004
6501.00367