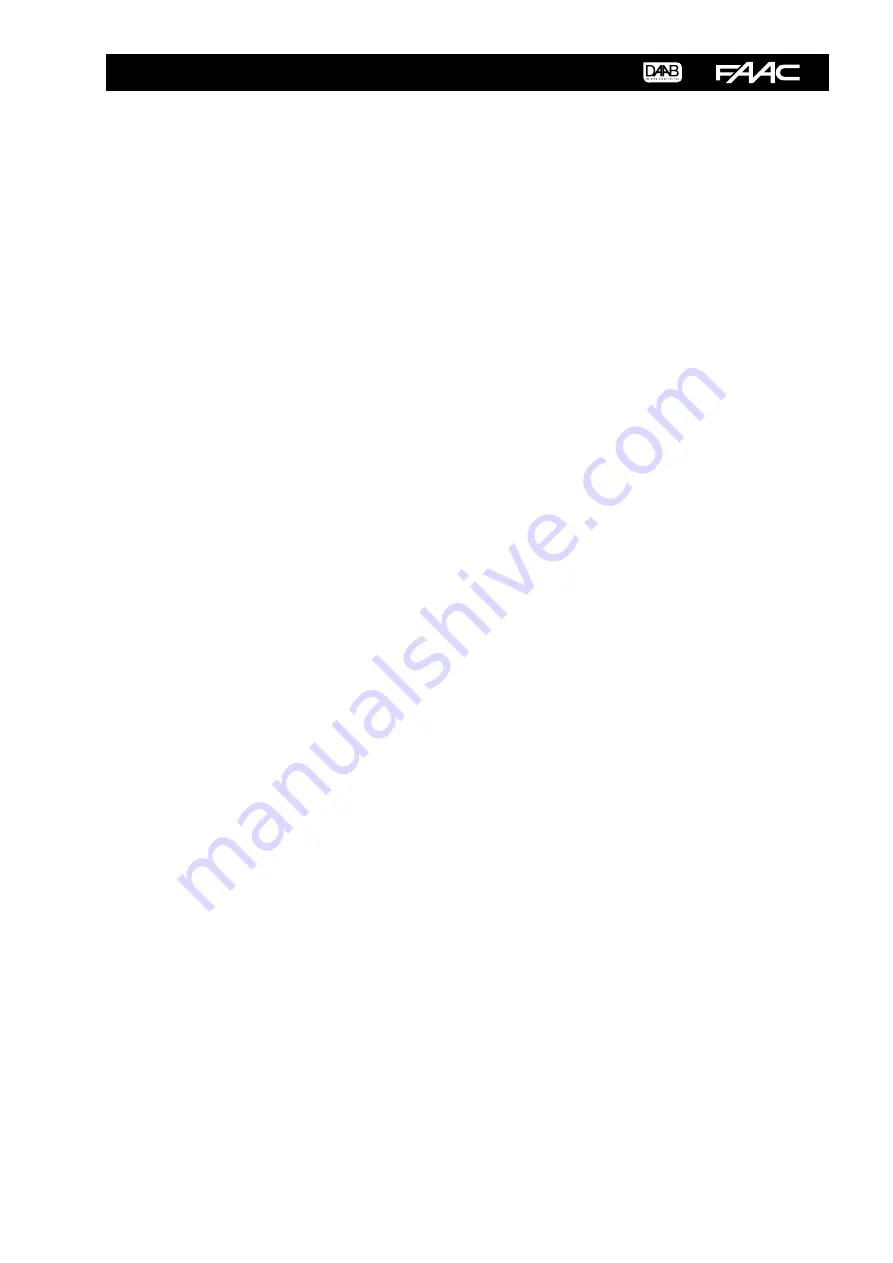
INSTRUCTION MANUAL DAAB AUTOMATIC CONTROL UNIT EP105
31
Revision 3
Automatic closing after stop
All control signals except stop and power failure restart the countdown for automatic closing. This means that automatic
closing is not affected in the event of a stop signal. This applies to conventional inputs and to programmable inputs.
If you want the countdown to restart automatically even after stop has been activated, you must set a delay in channel C520
and C500.
Select channel C520 and set a 20 - 600 seconds delay for automatic closing after stop has been activated. Set the value to
000 to disable automatic closing.
Automatic closing after photocell activation
This function enables automatic closing after a photocell is activated.
Use channel C351 to activate the function.
Select channel C351 and set the value to 1 to activate or 0 to deactivate.
Use channel C354 to specify how the door closes once the photocell is no longer activated.
Select channel C354 and set the value to 1 to close immediately, or 2 to close only after opening fully.
To delay closing after photocell activation, select channel C510 and set a time between 0 and 99 seconds.
Note that the delay configured in channel C510 is also used for automatic closing after the vehicle loop is activated.
If the photocell is not activated, automatic closing occurs as described above.
Automatic closing after vehicle loop activation
This function enables automatic closing after the vehicle loop is activated. The function is present on both loops, but is
shown below for loop 1.
To access the function, select channel d151.
Select channel d151 and set the value to 1 to activate or 0 to deactivate.
Use channel d154 to specify how the door closes once the vehicle loop is no longer activated.
Select channel d154 and set the value to 1 to close immediately, or 2 to close only after opening fully.
To delay closing after loop activation, select channel C510 and set a time between 0 and 99 seconds.
Note that the delay configured in channel C510 is also used for automatic closing after a photocell is activated.
If the vehicle loop is not activated, automatic closing occurs as described above.
Direction sensing for an internal closing pulse
Using channel C591 and the DB402 add-in card for vehicle loops, you can configure the internal close signal depending on
the preferred direction sensing mode in LOOP1 and LOOP2 and the PHOTO input.
See the channel reference for all possible values.
• Run-on time with mechanical limit switches
The run-on time is the set time that the control continues to run the motor after the limit switch has been tripped. By
making a rough setting of the mechanical limit switch, so that it trips earlier, the final position of the gate or door can then
be finely adjusted using the run-on time. This avoids the need to climb up to the drive unit for fine adjustment of the limit
switch. The run-on time can also be used if you want a door to close securely against the frame without triggering the load
guard or safety edge.
To see how stop is to take place during the run-on time, see also the section “
Stop function during run-on time in closing
” below.
NOTE! The run-on time must never be set so long that there is a risk of the limit switch cam bypassing the limit switch.
Run-on time for closing
Run-on time means that when the limit switch in the closed position has been activated the gate or door continues closing
during the set run-on time and the movement is then stopped. Choose channel L213 for run-on time in closing for motor
1 and channel L223 for motor 2.
Run-on time for opening
Run-on time means that when the limit switch in the open position has been activated the gate or door continues opening
during the set run-on time and the movement is then stopped. Choose channel L212 for run-on time in opening for motor
1 and channel L222 för motor 2.
Stop function after run-on time in closing movement
There are two events that can activate the closing movement during run-on time. Either a safety edge is activated or
the load guard trips. If neither of these occurs, movement will stop when the run-on time expires. What is to activate
movement is controlled by the settings in C436, C448 and C449. Channel C436 determines if safety edge or load guard is
to be able to stop a closing movement during the run-on time.
If C436 is set to 0, neither safety edge nor load guard will stop movement, and reversing or nothing will take place
depending on the settings in C448 and C449. In both these channels 0 means that nothing happens in activation of safety
edge or load guard, and the closing movement continues during the run-on time. If C448 and/or C449 are set to 1, the
closing movement will reverse.
Содержание DAAB EP105
Страница 1: ...INSTRUCTION MANUAL DAAB AUTOMATIC CONTROL UNIT EP105...
Страница 58: ...INSTRUCTION MANUAL DAAB AUTOMATIC CONTROL UNIT EP105 58 Revision 3 Notes...
Страница 59: ...INSTRUCTION MANUAL DAAB AUTOMATIC CONTROL UNIT EP105 59 Revision 3 Notes...
Страница 60: ...Revision 3 FAAC Nordic AB Box 125 SE 284 22 Perstorp 46 435 77 95 00 www faac se support faac se...