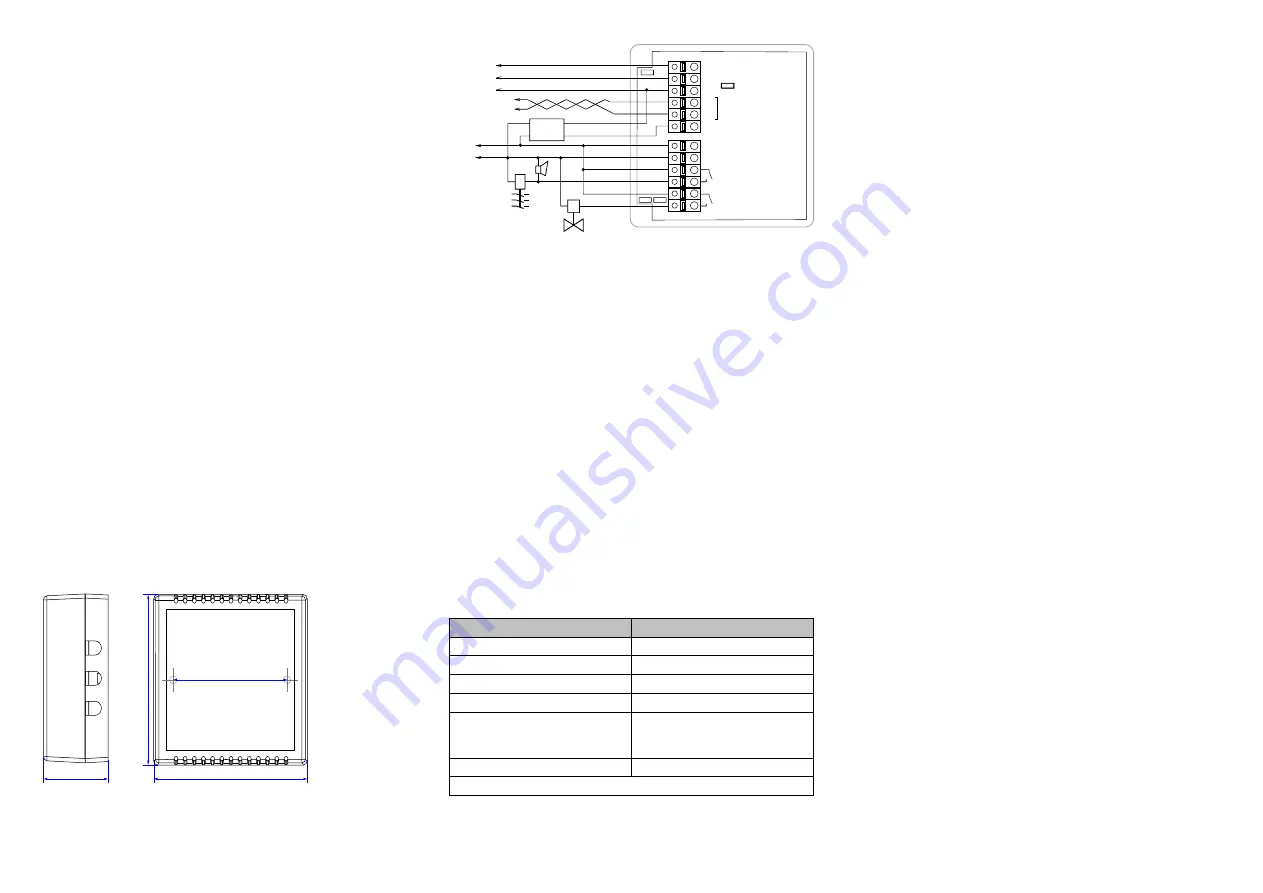
Halocarbon Refrigerants Detector-TransmitterE2611-HFC
is intended for early
detection of leakages or accumulation of halocarbon refrigerants in indoor spaces.
The instrument is based on fully calibrated and temperature compensated
semiconductor metal oxide sensor with high repeatability, stability and long lifetime.
E2611 provides two independent analog outputs OUT1 and OUT2, user-selectable
to 4-20 mA or 0-10 V, proportional either to gas concentration or temperature.
RS485 Modbus RTU digital communication interface allows easy instrument
configuration and integration into various automation systems. Two relays RE1 and
RE2 with closing contacts can be used to switch 24 V or 230 V powered alarm
sirens, ventilation fans, shut-off valves or other actuators.
Safety requirements
Always adhere to the safety provisions applicable in the country of use.
Do not perform any maintenance operation with the power on. Do not let water or
foreign objects inside the device.
Operating conditions
The device should be used in explosion-safe (non ATEX -rated) indoor areas at the
atmospheric pressure ±10%, <95 %RH, without condensation, and temperature
within the range -30...+70 °C.
Metal oxide sensor cannot properly operate in a zero or low oxygen content
atmosphere. Normal ambient oxygen concentration is recommended.
Avoid exposure to highly corrosive gases (H
2
S, SO
2
, HCl, Cl
2
etc), and volatile
silicon containing materials (silicone rubber/putty, hair grooming materials,
adhesives).
Avoid mechanical shock or strong vibrations.
Avoid sources of electromagnetic interference
Installation and connections
The gas detector should be mounted on a wall at a place located not more than 5
m from a possible leakage source and not very close to ventilation openings or
strong air currents. Avoid the areas without air circulation (corners, niches) as well.
Since halocarbon refrigerants are heavier than air, it is advisable to place the
detector not higher than a potential leakage source. Consider, if the vapors are
heated or not, if the detector is used for fire safety (LEL range) or air quality control
(ppm range) etc. Take into consideration the geometry of the room and the speed
and direction of air currents.
Make sure that the installed detector is available for maintenance and repair.
To install and connect the device, proceed as follows:
1. Detach the base of the enclosure by gently pulling along four guiding pins.
2. Attach the base to the wall with two screws. (see dimensional drawing below).
3. Connect power supply and external devices to the terminal blocks on the PCB
according to the connection diagram below.
To power the instrument from an external 24 VDC source, connect terminals 0 V
and +U to the source. If an integrated mains power supply module is used, connect
terminals L and N to the mains.
NB!
If the instrument is powered from mains, connect to 0 V and +U terminals only
light external loads, which consume less than 30 mA in total, as the integrated
mains supply module capacity is limited.
To use analog outputs, connect the terminals OUT1 and/or OUT2 and 0 V to the
input of the secondary instrument (indicator or controller).
NB!
The outputs are not galvanically isolated from 24 V power supply and share
common 0 V. Allowed load resistance limits are stated in Specifications table.
The type of each analog output can be independently changed between 4-20 mA
and 0-10 V with jumpers J1 (OUT1) and J2 (OUT2).
With closed jumper the output is 0-10 V, with open jumper the output is 4-20 mA.
By default, both outputs OUT1 and OUT2 are assigned to gas concentration. The
device has built-in temperature sensor which may be tied to any of the outputs. The
output assignments and scales can be changed by Modbus commands.
We recommend to set the difference between the upper and bottom limits of the
output scale not narrower than 20% of detection range. In any case, do not set the
output scale below the tenfold resolution of the device.
To use relay outputs, connect the chosen actuators to the relay terminals RE1
and/or RE2.
NB!
Actuator short-circuits shall be avoided, to protect the instrument relays use
external fuses or safety switches.
4. Turn on the power. It may take up to five minutes after switching on for the
sensor to stabilize. During this period relays, analog outputs and Modbus interface
are off. A LED placed on the PCB of the device allows to control the connection
process. The LED response to different processes is presented in the table below.
Process
LED mode
Sensor heating period
Blinking 0.5 Hz (50% on, 50% off)
Sensor absence or malfunction
Blinking 0.5Hz (90% off, 10% on)
Relay 1 turned on
Blinking 1 Hz (50% on, 50% off)
Relay 2 turned on
Blinking 2 Hz (50% on, 50% off)
Modbus response
The signal is modulated with short on off
pulses, even single Modbus cycle is
traceable*
Normal measurement
Continuous light
* Pulse corresponding to Modbus response is visible only when diode light is on
5. Push enclosure to the base.
Operation
For best stability the gas detector should be powered permanently. If the instrument
is left for a long time in unpowered state, then after initial power-on the metal-oxide
gas sensor needs some time to heat up and burn adsorbed contaminants. So for
first tens of seconds of few minutes an alarm activation may be possible. After this
heating-up period the instrument turns into normal mode.
When the concentration of the detected gas reaches the LOW alarm level, the
control LED starts blinking and the buzzer starts beeping with 1 Hz frequency.
When the HI alarm level is reached, the frequency of blinking/beeping is 2 Hz. The
alarm signal turns off automatically, if gas concentration decreases to 80% of the
alarm set point.
Configuring
Gas detector E2611 shares all functionalities of the PluraSens® multifunctional
transmitter platform. The features and options include:
- digital output change rate limiting filter
- digital integrating (averaging) filter
- temperature measurement channel with internal sensor
- free assignment of each analog output to chosen parameter
- flexible setting of analog output scales for each output
- output shift and slope adjustment for calibration
- free assignment of each of two relays to chosen parameter
- several relay control logic modes (HI or LO with hysteresis, U or П)
- switch delays and minimum on/off state durations for each relay
- Modbus controlled forced state option for analog outputs and relays.
E2611 can be configured through its RS485 interface by Modbus RTU commands.
A standard configuration kit includes Model E1087 USB-RS485 converter and
E26XX Configurator software.
For procedure details please contact your Seller or Manufacturer.
Calibration and maintenance
The device has been calibrated by Manufacturer with standard gas mixtures before
delivery. The instrument requires at least annual field recalibration with a portable
calibration kit. For procedure details please contact your Seller or Manufacturer.
The calibration should be preferably performed by Manufacturer's authorized
representative.
Return to default settings
To reset the device’s Slave ID, baud rate and sbit number to factory settings,
proceed as follows:
1. De-energize the device
2. Connect the J3 jumper
3. Turn on the device
4. De-energize the device
5. Disconnect the J3 jumper
6. Turn on the device
Warranty
This product is warranted to be free from defects in material and workmanship for a
period of one year from the date of original sale. During this warranty period
Manufacturer will, at its option, either repair or replace product that proves to be
defective. This warranty is void if the product has been operated in conditions
outside ranges specified by Manufacturer or damaged by customer error or
negligence or if there has been an unauthorized modification.
85
37
8
5
63
Input 1 4-20 mA / 0-10 V
Input 2 4-20 mA / 0-10 V
0V / GND
Controller
OUT1
OUT2
0V
A
B
RS485
+U = 11...30 VDC
L
N
90...265 VAC
RE1
RE2
Fieldbus
S
PSU
24 VDC
+
-
J1 J2
230 VAC
J3
Control LED