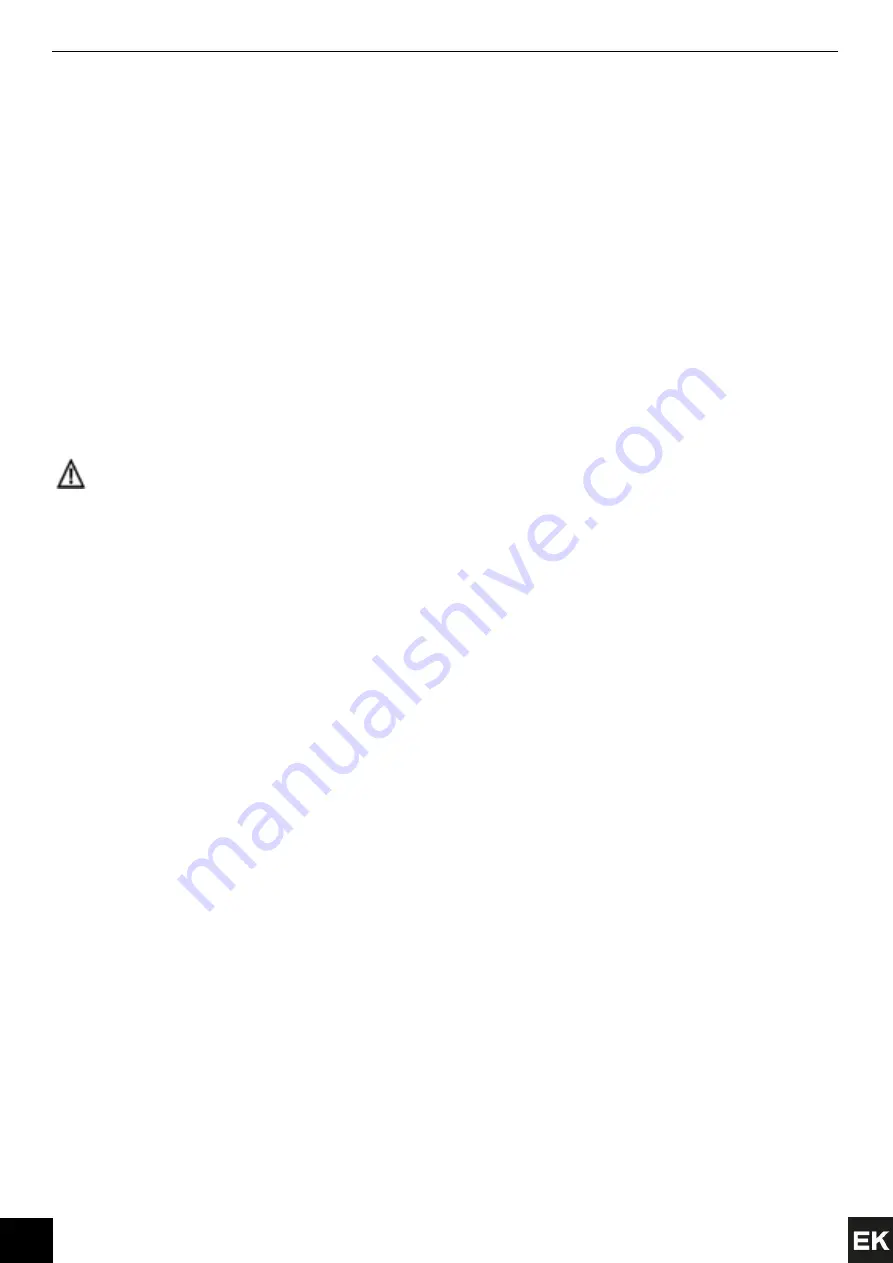
46
www.euroklimat.it
6.3
SUPPLEMENTARY MAINTENANCE
In general, supplementary maintenance varies considerably and frequently depends on how often the equipment is used and the environmental
working conditions (atmospheric conditions, context of use, etc.). In particular, it is important to assess what the supplementary activities to be
carried out are and plan the operations appropriately with the correct frequency. Only highly specialised members of personnel can truly
comprehend the needs of the machine and are authorised to operate on it. In the event of further
queries, contact the Manufacturer’s Technical
Assistance Office. Fundamental operations to keep the system fully operational and efficient must be carried out during Routine Maintenance.
However, besides the specific evaluations stated previously, below are a few general activities that we believe should be pointed out in advance.
•
WASHING CONDENSING COIL
–
Carry out the operation using a jet of water to be propelled in the opposite direction to the air flow.
Check cleaning between the wings. (frequency every 12 months)
•
INSPECTION PRESSURE CONTAINERS
–
Make a visual inspection. In the event of deformations, turn off the machine and immediately
contact the Manufacturer’s Technical Assistance Office
(frequency every 12 months)
•
UNEXPECTED FAULTS
–
In the event of unusual situations,
do not hesitate to contact the Manufacturer’s Technical Assistance Office
(the fault is unexpected so report it as soon as it is detected)
In conclusion, we wish to stress the importance of a constant maintenance strategy with the necessary planning and, in particular, attention on
the part of users, who are the first to detect malfunctioning.
Lubrication and oil removal
NOTE
–
Possible chemical reaction and/or compressor failure.
Do not mix ester oils with mineral oils and/or alkyl-benzene oils when using HFC refrigerants.
The compressor is supplied with an initial oil charge. Scroll compressors for R410A are charged with a standard charge of polyester oil (POE)
EMKARATE (TM) RL 32-3MAF.
The litres of oil charged at the start are specified on the compressor plate.
When charging the system with oil, we suggest you use a POE oil that has a humidity content of no greater than 50 ppm. This will keep the
humidity level in the circuit below 50 ppm.
6.4
CALIBRATIONS AND TROUBLESHOOTING
This manual refers to machines from the EKS series. This range of chillers is designed and built for various uses: air-conditioning systems and
industrial process cooling. For this reason, the internal programming parameters of the variables may differ depending on their use. The same
chiller may have different calibrations depending on the type of installation, country of use, functions and other technical parameters.
Consequently, we believe it is pointless to include a list of parameters in this section with the respective calibration values (which, amongst other
things, are numerous and could cause confusion). These settings are extremely specific and delicate and we therefore ask you to abide by the
following principles:
•
To change the factory calibrations, contact highly qualified members of staff.
•
Some of the parameters are the manufacturer’s own and their modification must be
authorised by the Manufacturer.
•
Request the document from the Manufacturer with a list of the specific calibrations carried out on the machine in use.
•
Any unauthorised operations could result in serious damage and invalidate the terms of the Guarantee of the equipment.
The machine’s control, management and operating settings
(in terms of hydraulics, aeraulics, refrigeration and electrics) are made with the
calibration values entered in the various parameters on the microprocessor. It is extremely dangerous to change the settings without knowing
the specific cause that may also depend on complex and multi-faceted functional reasons.
YOU ARE STRONGLY ADVISED TO CONTACT THE
MANUFACTURER BEFORE CHANGING THE SET PARAMETERS.