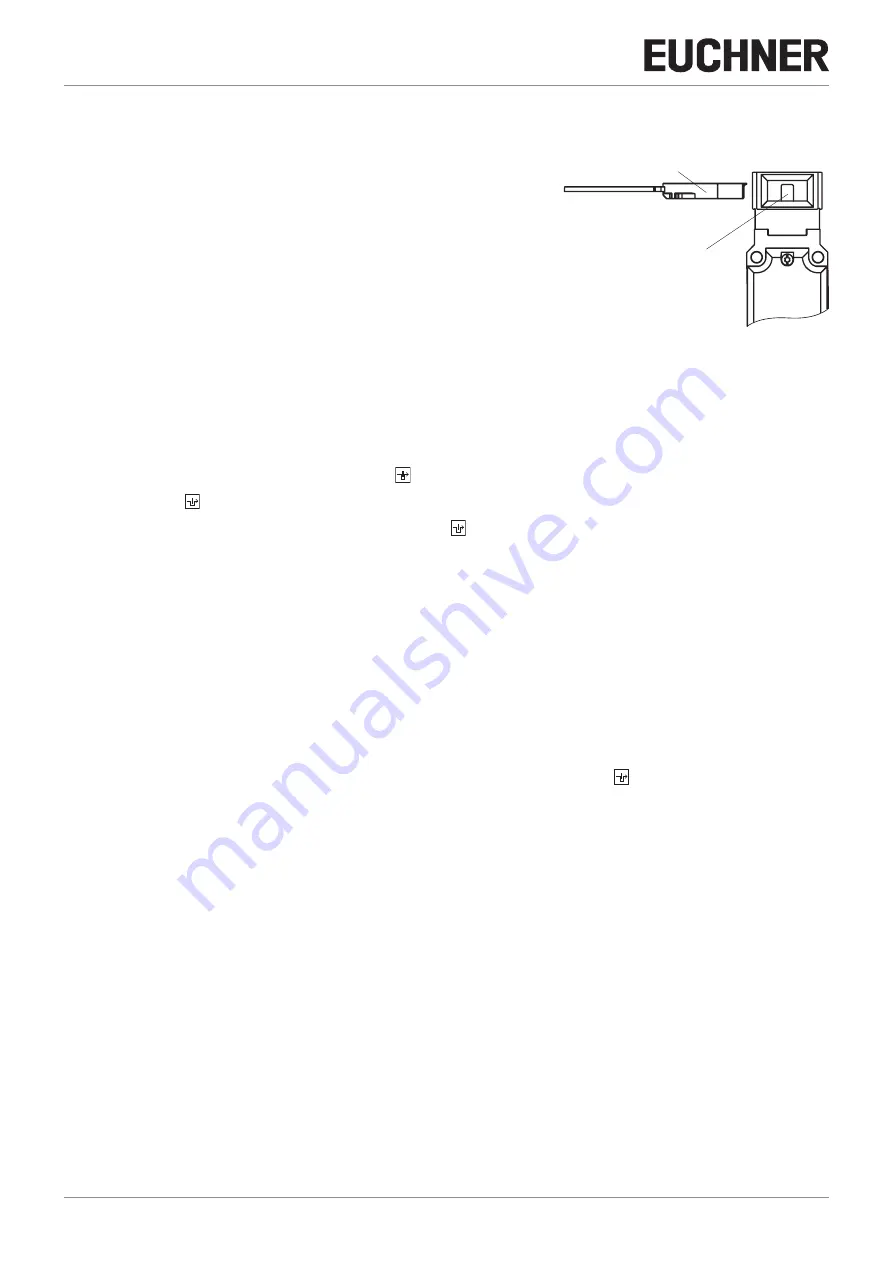
Operating Instructions
Transponder-Coded Safety Switch CTP-LBI-AP
8
(translation of the original operating instructions) 2136918-04-05/19
6. Function
The device permits the locking of movable guards.
The system consists of the following components: coded actuator (transponder)
and switch.
Whether the device learns the complete actuator code (unicode) or not (multi-
code) depends on the respective version.
Ì
Devices with unicode evaluation
: The actuator must be assigned to the
safety switch by a teach-in operation so that it is detected by the system.
This unambiguous assignment ensures a particularly high level of protection
against tampering. The system thus possesses a high coding level.
Ì
Devices with multicode evaluation
: Unlike systems with unique code
detection, on multicode devices a specific code is not requested but instead it is only checked whether the actuator is
of a type that can be detected by the system (multicode detection). There is no exact comparison of the actuator code
with the taught-in code in the safety switch (unique code detection). The system possesses a low coding level.
When the guard is closed, the actuator is moved into the safety switch. When the switch-on distance is reached, power is
supplied to the actuator by the switch and data are transferred.
If a permissible code is detected, the safety outputs
are switched on.
The safety outputs
and the monitoring output (OL) are switched off when the guard is unlocked.
In the event of a fault in the safety switch, the safety outputs are switched off and the DIA LED illuminates red. The oc-
currence of faults is detected at the latest on the next demand to close the safety outputs (e.g. on starting).
The switch has, in addition to the mechanical/electromagnetic guard locking, fixing for the guard locking pin. The guard
locking pin is held in its current position if the operating voltage is not present. The guard locking pin can be moved only
by applying the operating voltage.
If the guard locking pin is extended and the guard is still open when the power supply is interrupted, the guard locking pin
will be pushed down and held in this position the next time the door is closed.
In case of interruption of the power supply (operating voltage) for the switch or if the machine is switched off for servicing,
for example, the guard locking pin is held in its last position. As a result the safety door is either permanently locked or it
can be closed and opened as often as required without the guard locking pin locking.
6.1.
Guard locking monitoring
All versions feature two safe outputs for monitoring guard locking. The safety outputs (FO1A and FO1B) are switched
off when guard locking is released.
6.2.
Door monitoring output (OD)
The door monitoring output is switched on as soon as the actuator is inserted in the switch head (state: guard closed and
not locked). The door monitoring output also remains switched on when guard locking is active.
6.3.
Diagnostics output (OI)
The diagnostics output is switched on in the event of a fault (switch-on condition as for DIA LED).
6.4.
Guard locking monitoring output (OL)
The guard locking monitoring output is switched on when guard locking is active.
Transponder-coded
actuator
Guard locking pin