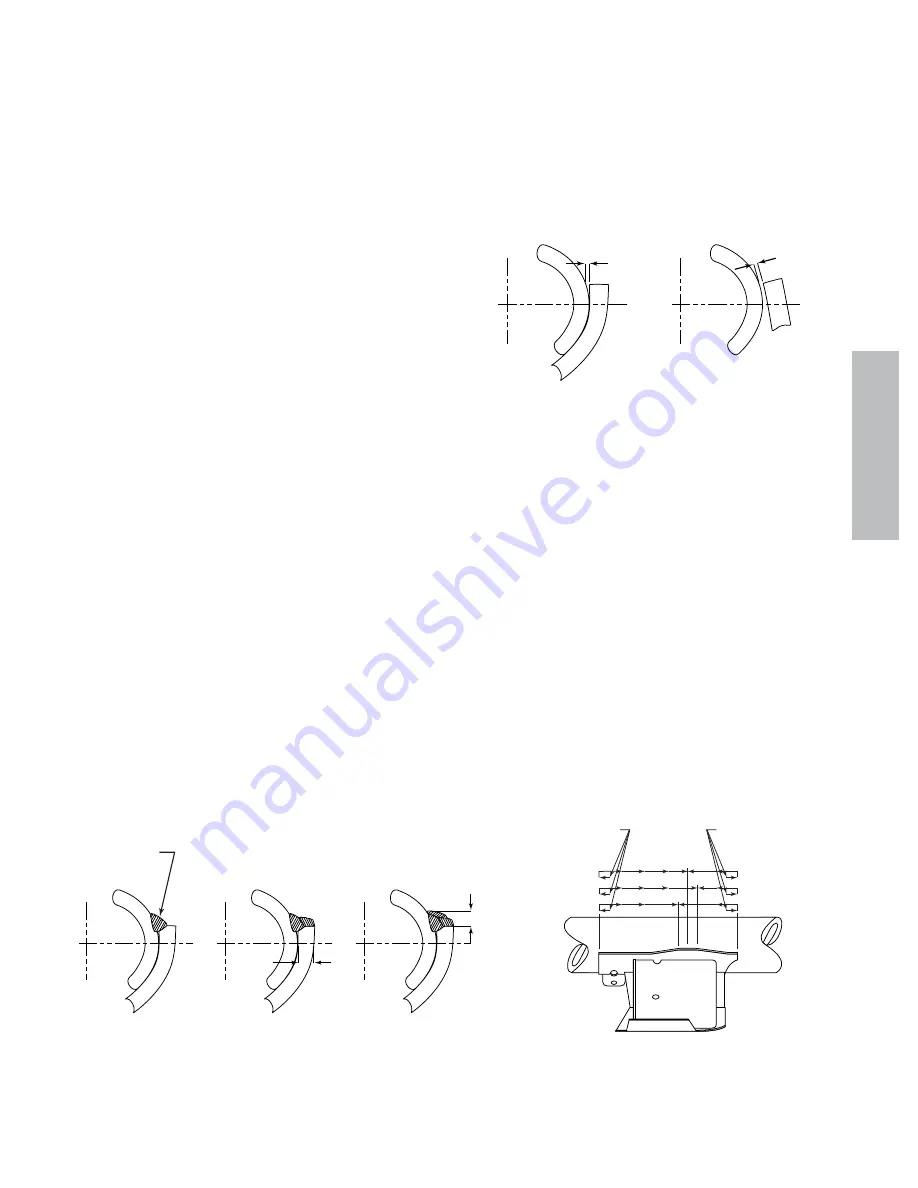
23
MAINTENANCE
Welding Guidelines
The following precautions and recommendations
must be read and understood by qualified personnel
prior to weld installation of Ridewell Air-Ride Trailer
Suspensions to trailer axles. Any welding procedures
or materials that do not clearly fall within these guide-
lines could compromise the integrity and safety of the
installation.
Welding Methods, Materials & Personnel
A) All welders and welding operators should be
certified per A.W.S (American Welding Society) D1.1
Section 5 Procedures or equal.
B) Recommended welding methods are shielded
metal arc (stick), gas metal arc (solid wire) or flux cored
arc (tubular wire) welding. Whatever electrode and
method used must develop a minimum weld tensile
strength of 70,000 P.S.I. Refer to the electrode
manufacturer's recommendation for voltage, current and
shielding medium for the diameter electrode to be used
so the best fusion and mechanical properties can be ob-
tained.
C) All electrodes used should meet A.W.S. Section
5 Specifications and Classifications for welding car-
bon and low alloy steels.
D) If shielded metal arc electrodes (stick) are used,
they must be new and unused, dry, free of contami-
nants and come from a stock that has been purchased
and stored per A.W.S. Section 4.5.2., Low Hydrogen
Electrode Storage Specifications.
Weld Joint Preparation
A) All grease, dirt, paint, slag or other contami-
nants must be removed from the weld joint without
gouging the axle tube.
B) Insure the lower beam assembly fits the axle with
a weld root gap of 1/16" to 1/8" maximum between the
welding wings or uprights as illustrated. (See Figure
16.)
Figure 16. Root Weld Gap
Welding Procedure
A) Ground the axle to one of the attached axle parts
such as the air chamber brackets, cam brackets, or the
brake spider. Never ground the axle to a wheel or
hub as the spindle bearing may sustain damage.
B) The axle assembly should be at a minimum tem-
perature of 60º F (15º C) prior to welding. Pre-heating
the weld zone to the axle manufacturer's recom-
mended pre-heat temperature is recommended. This
will minimize the formation of martensitic or brittle
metal structures in the fusion line or the heat affected
zone which may contribute to a premature fatigue fail-
ure in service.
C) The joint to be welded should be positioned in
the flat or horizontal position if possible.
1/16 to
1/8 Max
1/16 to
1/8 Max
FIRST
PASS
SECOND
PASS
THIRD
PASS
1/2
3/8 FILLET
WELD
1/2
THIRD PASS
ARC START
ARC START
SECOND PASS
FIRST PASS
THIRD PASS
SECOND PASS
FIRST PASS
Figure 17. Multiple Pass Recommended Method