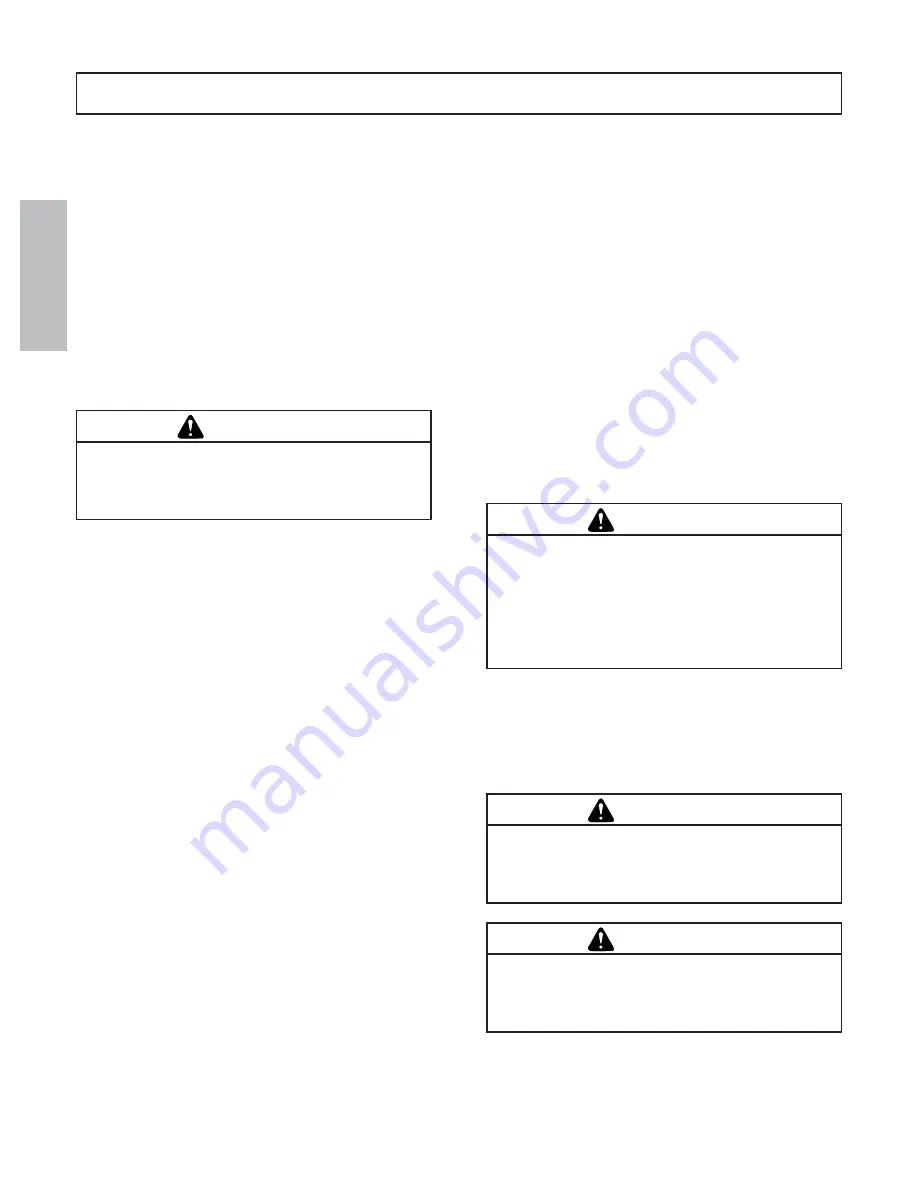
18
OPERA
TION
Tank Capacity
The Shooter II Distributor is designed to pump and
spray a variety of asphalt products in an efficient and
user friendly manner with great accuracy. The Shooter
II Distributor utilizes a computer to sense the vehicle’s
ground speed and control the hydrostatically driven
asphalt pump to maintain the set application rate, re-
gardless of variations in vehicle speed or spray bar width
in use.
For a complete description of each of the controls
and how to set up the machine, refer to the set up sec-
tion of this manual.
WARNING
To prevent possible personal injury: Do not
load the vehicle beyond the GAWR or GVWR.
The maximum load volume must be calculated
based on material density
The Shooter II Distributor tank has a built-in air
space, or expansion space, above the “Tank Full” level.
This air space is designed to minimize the chance that
the tank will overflow if the material in the tank ex-
pands due to heating or foaming. This air space should
not be used to carry product. The “Tank Full” level is
based on the vehicle’s axle ratings, and, GVWR at a
material density of 7.7 lbs/gallon. A lower “tank full”
must be calculated if a product with a density greater
than 7.7 lbs/gallon is to be loaded. The lower “tank full”
is calculated by multiplying the original “tank full” by
7.7 and dividing the result by the new heavier product
density.
If you suspect there may be moisture or emulsion in
the tank, Dow-Corning DC-200 additive can be used
to reduce foaming if a product being pumped is at a
temperature in excess of 200ºF. Additional DC-200 ad-
ditive may be obtained from E. D. Etnyre & Co. or
your Etnyre dealer.
Mixing Dow-Corning DC-200 Anti Foam
Agent
Mix the contents of one can (16 oz.) with one (1)
gallon of diesel fuel or kerosene. Add one (1) ounce of
this diluted mixture to each 1000 gallons of asphalt.
The correct amount may be poured through the man-
hole. This will assist in reducing foaming, particularly
if moisture is present or if an emulsified asphalt was
used in a previous load.
If you suspect that there may be moisture in the spray
bar or circulating system, the filling operation should
be stopped when the tank is no more than 25% full.
The product should then be circulated from the tank
through the spray bar for a minimum of 2 minutes at a
rate of 80 to 110 GPM before continuing the filling
operation. After circulating product in the spray bar,
suck back the material from the bar and then return to
the loading configuration and continue loading.
If foaming does occur, continue circulating until the
foaming stops, and then suck back the product from
the spray bar into the tank before continuing the load-
ing operation.
Filling Through the Fill Line
WARNING
To prevent possible burns from foaming or
violent eruption, do not load tank with material
temperature over 200ºF if water or
condensation is present in tank, or if emulsion
was used in the previous load. Do not heat
material over 200ºF if moisture or emulsion is
present in tank.
Connections and Preliminary Checks
WARNING
To prevent possible burns from leaking
material: Be sure all pipe, cap and hose
connections are secure before opening valves
or beginning any operation.
WARNING
To prevent possible burns to operators or
bystanders, or possible equipment damage,
do not start any operation if any control
settings are unknown.
General
Содержание Black-Topper Shooter II
Страница 3: ...2 ...