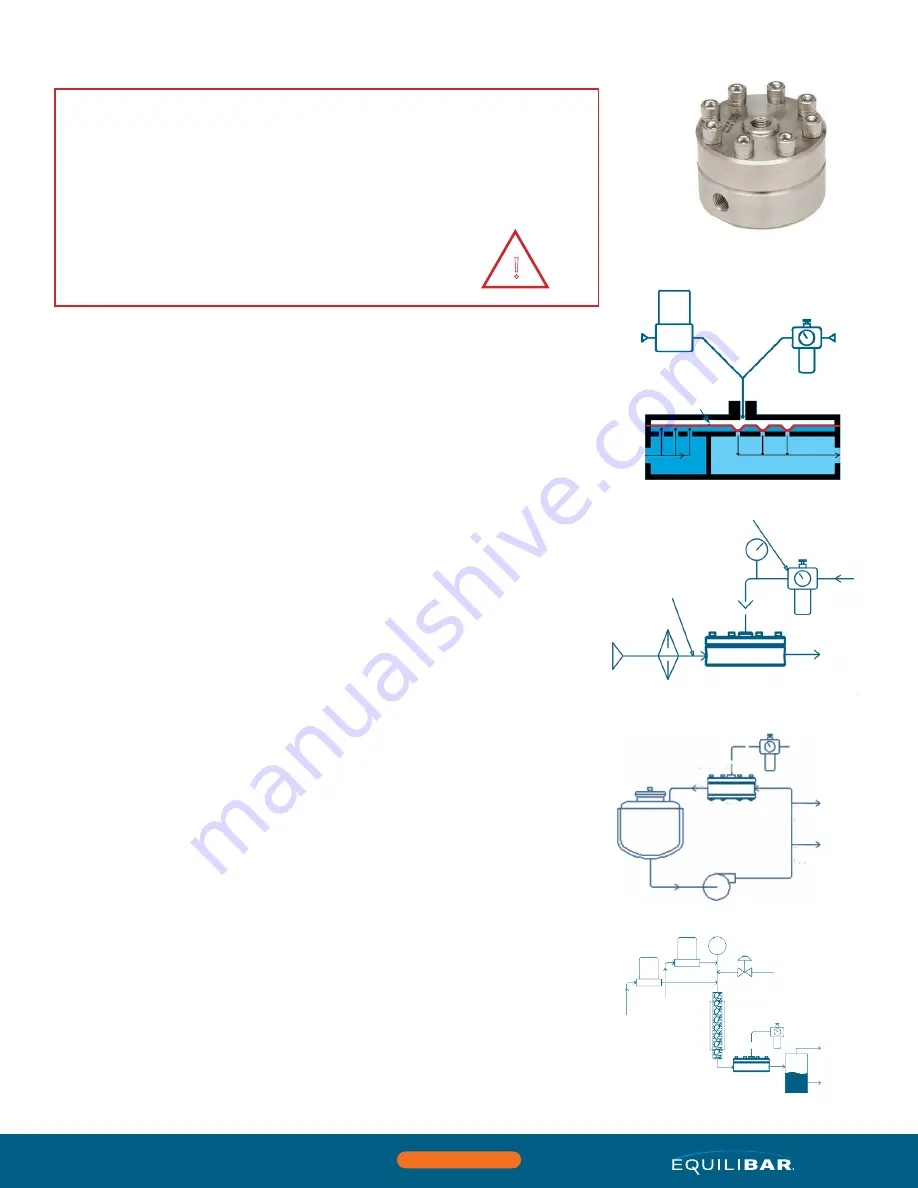
Page 1 of 6
www.equilibar.com
828.650.6590
©2010-2020 Equilibar, LLC
25/08/20 R6
Fig. 4
To
Application
To
Application
Any Pump
R
O
I
Reference
Pressure
Source
Liquid Rectant #3
Set-Point
Pressure
Reactant #1
Reactant #2
MFC
PG
MFC
Catalyst
Research
Reactor
Seperator
Equilibar® Back
Pressure Regulator
Equilibar
©
Back Pressure
Regulator
Pilot Regulator can
be remotely located
Pressure Reducing
Regulator, Relieving
Compressed
Gas Supply
Media is
vented
from the
outlet port
Media Pressure
is controlled here
Incoming
Media
Filter or
Strainer
Equilibar
©
Back Pressure
Regulator
Gauge
Research Series Precision Back Pressure Regulator
Fig. 1
Fig. 2
Fig. 3
WARNING:
Make sure that you have read and understand these directions before using, installing, or
maintaining the Equilibar pressure regulator. Take steps to ensure this instruction manual reaches
the operator of this regulator and stays with the regulator throughout its lifetime. Use, installation,
operation, and maintenance of all pressurized products including this regulator must be performed
by personnel who are properly trained and qualified through experience or specific training.
Failure to properly observe the instructions contained in this document may result in, but is not
limited to:
•
Serious personal injury or death
•
Unconstrained release of the pressurized media
•
Permanent damage to the pressure regulator and/or permanent
damage to connected equipment
REGULATOR USE AND STARTUP
Diaphragm
Manual Pressure
Regulator
Inlet
Outlet
Electro-
Pneumatic
Regulator
Pilot
(Reference)
E/P
Outlet
Inlet
- OR -
2 SET-POINT OPTIONS
!
The Equilibar® Research Series valves are precision back pressure regulators (BPR’s).
These BPR’s control the fluid pressure at the inlet “I” port. The Equilibar BPR controls the
inlet pressure by allowing excess flow to vent from the system through the regulator’s
outlet “O” port. The flow direction is from inlet to outlet. The Equilibar BPR is pilot
operated, where the pressure setpoint is determined by the pressure applied to the
“Pilot” or “Reference” port on the BPR (see
Fig. 1
). The BPR will control the pressure at
its inlet port in a precise 1 to 1 relationship with the setpoint pressure applied to the
pilot port. The pilot pressure may be applied using a manual pressure regulator or an
electronic pressure regulator (electro-pneumatic regulator).
Refer to
Fig. 1
. The Equilibar BPR uses a flexible membrane diaphragm to both sense
the pressure and to provide a direct seal against the orifices in the regulator body. The
pilot pressure is applied to one side of the diaphragm. The Inlet “I” port pressure is
sensed on the other side of the diaphragm. When the pilot pressure is higher than the
Inlet pressure the diaphragm is pushed firmly against the orifices to form a seal and
the regulator is effectively closed. When the inlet pressure builds and just equals the
pilot pressure, the closing forces are removed from the diaphragm and media can begin
to pass from the Inlet to the Outlet port. When sufficient media has passed through
the regulator, the Inlet pressure will be reduced slightly, and the diaphragm is allowed
to seal against the orifices again. In normal practice equilibrium is achieved and the
diaphragm modulates into a position where just enough flow is allowed out of the
regulator in order to maintain a steady pressure on the Inlet port. (see
Fig. 2
)
Typical Circuits:
A back pressure regulator is used to control the pressure in a system
by venting any excess flow that would otherwise cause the system pressure to increase
above the pilot setpoint pressure. In the example circuit shown, the BPR is used to
control the outlet pressure of a pump (see
Fig. 3
). Excess fluid is vented through the
BPR back to the fluid reservoir.
Another example application is to use a BPR to control the pressure in a catalyst reactor
as various reactants are added (see
Fig. 4
). The reaction process, the influx of the
reactants, and the rise in temperature of the mixture all act together to increase reactor
pressure. The Equilibar BPR maintains the reactor pressure at the desired setpoint by
venting any media which would otherwise cause the pressure to increase above its
septoint.
Equilibar has trained engineers who can work with you to suggest a regulator design and
wetted materials for your specific application. These suggestions are recommendations
only and are dependent on complete and accurate information from the end user
about the application. It is the ultimate responsibility of the user to determine the
compatibility of the media with both the materials of construction of the back pressure
regulator and the pilot gas in use.
The diaphragm installed in the back pressure regulator is a careful balance between
the pressure, temperature, media compatibility, and flow rate. Often performance
in one area must be sacrificed to obtain acceptable performance in another. Many
diaphragm types cannot achieve tight shutoff and must have some minimum system
flow always present. If the system flow rate into the back pressure regulator is less than
the minimum flow rate required by the installed diaphragm, then the system pressure
will fall below the target setpoint pressure.
BACKGROUND