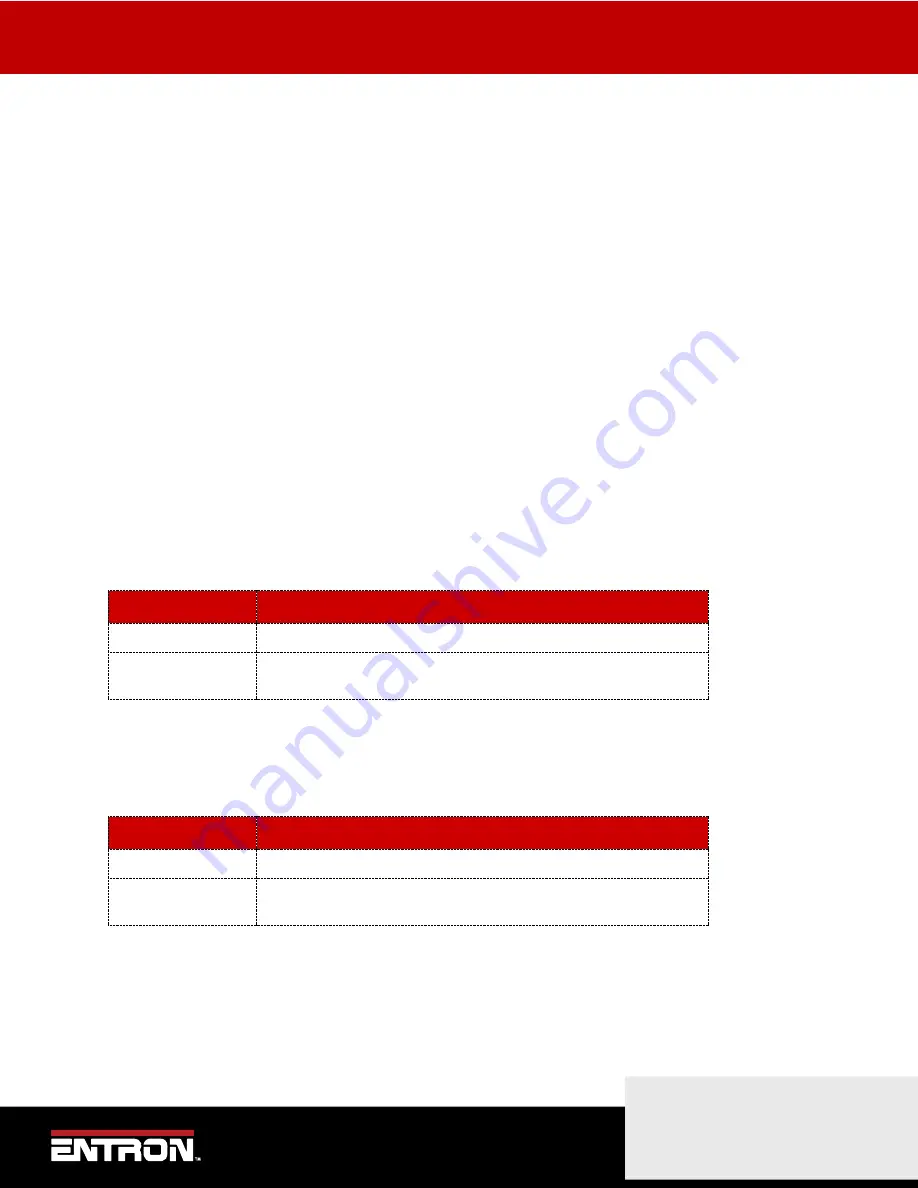
INTRODUCTION
Installation
36 |
P a g e
Copyright © 2021 BF ENTRON and/or its affiliates. All rights reserved
Product Model:
iPAK2v2
Firmware Version:
V2.10
May 22 | Doc No 700253-2
2.9.2.4
Stop on Fault
The Stop on Fault checkbox is used to define how the system will react to a fault. When the parameter is checked the
weld-air valve opens as normal but subsequent events are inhibited until a fault reset command is given.
2.9.2.5
EOS on Fault
When the “EOS (End of
Sequence) on Fault” checkbox is checked the EOS signal will be activated even on a fault, when a
fault is detected.
2.9.2.6
Headlock on Fault
When the “Headlock on Fault” checkbox is checked, the weld air
-valve output is held On and subsequent welds are
inhibited until the fault is reset.
2.9.2.7
iPAK (v1) Mode
When the “iPAK (v1) Mode” checkbox is checked the sense of the
READY
output is changed to
NOT READY
. AV4, AV5,
& AV6 are used for Multi-Welder (Cascade) selection. This flag may be needed when an iPAK or iPAK-MUX is updated to
an iPAK2 timer in the field.
2.9.2.8
Measure
The Measure parameter determines which current value will be measured by the control and output as a signal.
Value
Description
Primary
Measure the primary welding current (ie weld transformer primary current)
Secondary
Measure the secondary welding current.
This function requires a toroid sensor
(Rogowski coil) to be connected to the weld control.
2.9.2.9
Regulation
The Regulation parameter defines which current will be regulated when using the CCu and CCC control modes.
Value
Description
Primary
Regulate the primary current
Secondary
Regulate the secondary welding current.
This function requires a toroid sensor
(Rogowski coil) to be connected to the weld control.
2.9.2.10
Toroid Test
The Toroid Test checkbox defines whether the connected toroid (Rogowski coil) should be validated by the weld control.
When the value is checked the signal from an external toroid (Rogowski coil) must lie with a range of 10 to 300 Ohms.