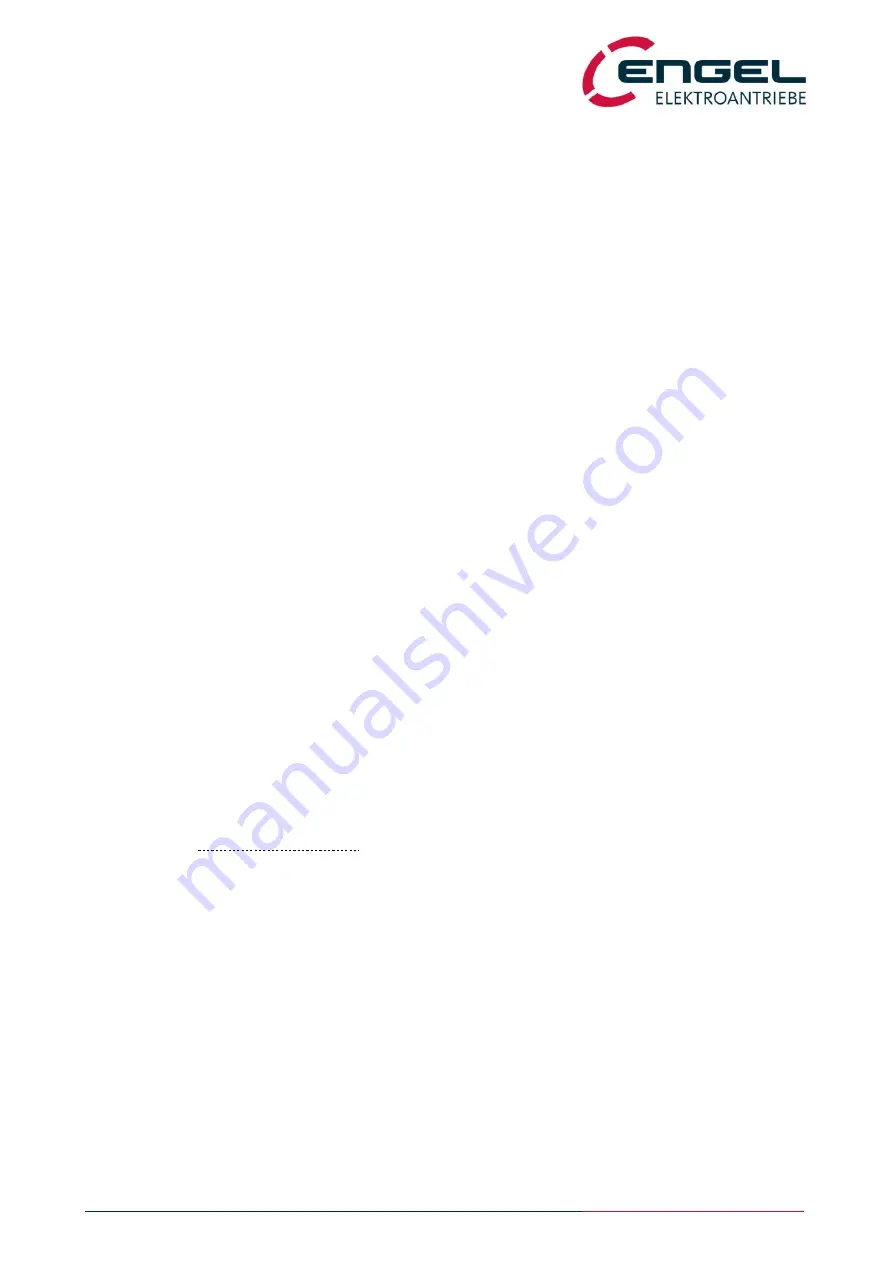
Integrated Synchronous Servo Drives
HBI 22xx / HBI 26xx / HBI 32xx / HBI 37xx
Operating Manual Rev. 1.6
www.engelantriebe.de
page 9
3.5
Integrated control electronics technical data
Control electronics
supply
approx. 50mA
Control electronics power
requirement
24V supply, disabled power
stage
(X1.A or. X1.C see chapter 5.1)
Analogue inputs
AI1 (differential input)
10V, 10bit, R
i
=20k
Digital inputs
DI1 ... DI8
0.0V
U
off
5.0V
15.0V
U
on
30V
DI1 = control enable.
DI4/DI5 can optionally be used
as output DO2/DO1
Digital outputs
DO1 ... DO2
24V, 50mA
o.C., ground switching,
33
series resistance,
without pull-up resistance,
can optionally be used as an
input
Serial interfaces
RS232
Communication with DSerV
parameterisation software
CAN 2.0B (Max. 1MBit/s)
only "-xCx" design
Without galvanic isolation by
default.
*7)
Without terminating resistor.
Incremental output
only "-xIx" design
A,A/,B,B/,Z,Z/
RS422 , 1024 increments/revolution
Hysteresis approx. 0.17°
Linearity error approx. 1.0°
min. edge spacing: 2µs
*8)
Electromagnetic compatibility
*4)
Emission
DIN EN 61800-3: 2004, 2005-07
second environment / limited
availability (Cat. C3)
Immunity
DIN EN 61800-3: 2004, 2005-07
second environment
*1) The specified values apply for the installation of the drive on a system surface made of aluminum (A=0.1m²,d=10mm).
It must be taken into consideration that the specified continuous output power must be derated for thermally unfavourable couplings.
*2) Observe chapter 3.6.1 Regenerative operation
*3) The rated current is the direct current drawn in nominal operation (n=3000rpm M=M
N
) from the supply voltage (+Ub=24V or 48V). The
current drawn from the supply voltage is proportional to the converted power, not be confused with the torque-building motor current,
which is displayed as sine peak value in DSerV and is proportional to the motor torque.
Please also observe that the supply line is lossy. This leads to a reduction in voltage and speed at the motor system and to increased
power consumption of the device. A connection line with a nominal cross-section of 1.5mm² already has an overall loss resistance of
approx. 25mΩ/m (conductors and return conductors)! Appropriate power reserves must be provided in the supply!
*4) Cable-conducted emissions must be suppressed through appropriate filtering measures in the energy supply (e.g. power supply unit)
of the device.
*5) Tolerance -10%
*6) Motor phase current as a sine peak value, which is required for the generation of the rated or peak torque. Motor phase current is
displayed in DSerV. Not to be confused with the current taken from the supply.
*7) With the drives HBI32xx / HBI37xx, a galvanic isolation of the CAN interface is available on request.
*8) For the proper
detection of the incremental signals, a counter with a count frequency of ≥ 500kHz is required.