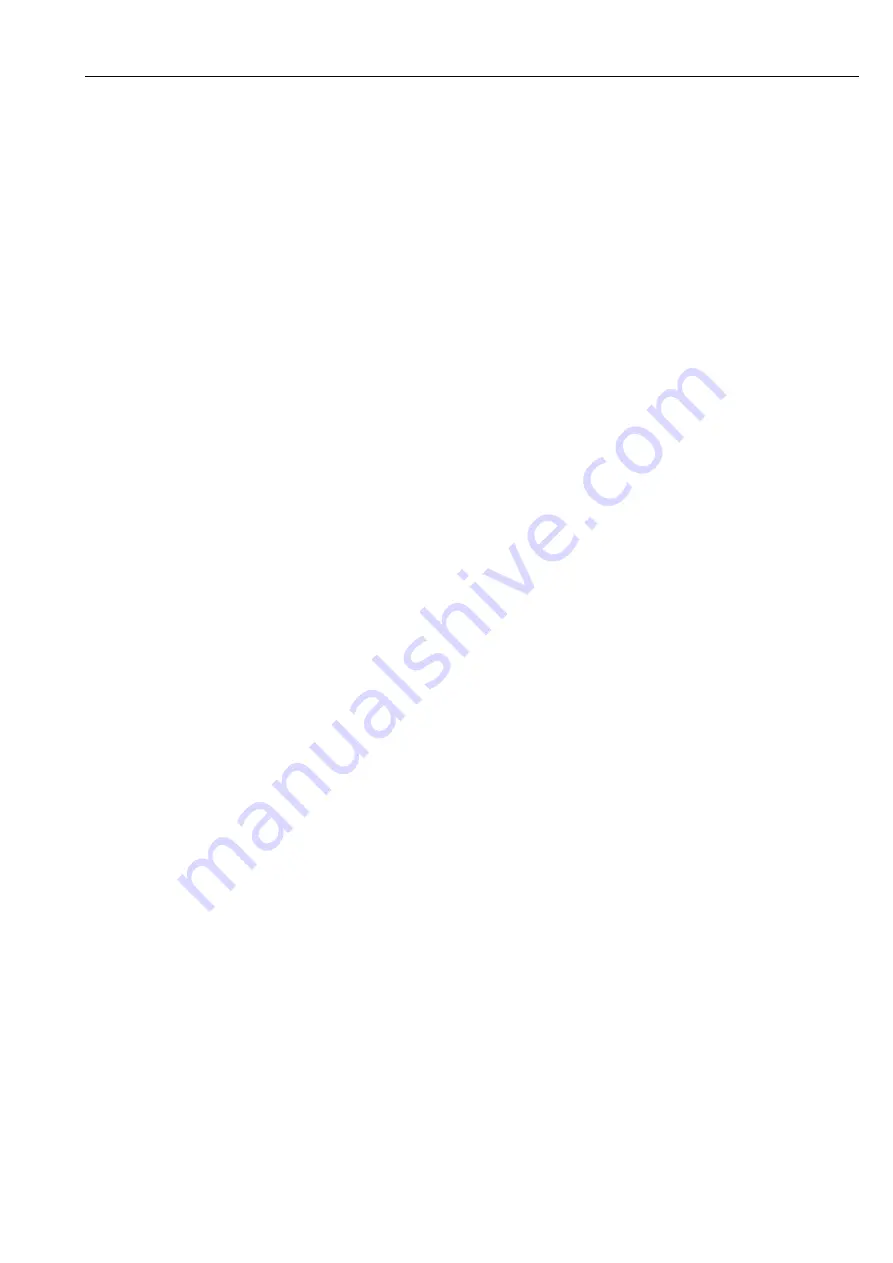
Proline Promag 55 PROFIBUS PA
Commissioning
Hauser
95
6.8
PROFIBUS PA acyclic data transmission
Acyclic data transmission is used to transmit parameters during commissioning or maintenance, or
to display additional measured variables that are not included in cyclic data traffic. Thus parameters
for identification, control or adjustment in the various blocks (Physical block, Transducer block,
function block) can be changed while the device is in the process of cyclic data transmission with a
PLC.
The measuring device supports the two basic types of acyclic data transmission:
• MS2AC communication with 2 available SAPs
• MS1AC communication
6.8.1
Master class 2 acyclic (MS2AC)
MS2AC is acyclic data transmission between a field device and a Class 2 master (z.B. FieldCare,
Siemens PDM etc.
Page 64 ). During this process, the master opens a communication channel
via an SAP (Service Access Point) to access the device.
All parameters to be exchanged with a device via PROFIBUS must be made known to a Class 2
master. This assignment to each individual parameter takes place either in a device description
(DD), a DTM (Device Type Manager), or inside a software component in the master via slot and
index addressing.
When using MS2AC communication, note the following:
• As described above, a Class 2 master accesses a device via special SAPs.
Therefore, the number of Class 2 masters that can communicate with a device simultaneously is
limited to the number of SAPs available for this data transmission.
• The use of a Class 2 master increases the cycle time of the bus system. This must be taken into
account when programming the control system used.
6.8.2
Master class 1 acyclic (MS1AC)
In MS1AC, a cyclic master,
that is already reading the cyclic data from the device or writing to the device opens the
communication channel via the SAP 0x33 (special Service Access Point for MS1AC) and can then
read or write a parameter acyclically like a Class 2 master via the slot and the index (if supported).
When using MS1AC communication, note the following:
• Currently, few PROFIBUS masters on the market support this data transmission.
• MS1AC is not supported by all PROFIBUS devices.
• In the user program, note that constant writing of parameters (for example, at every cycle of the
program) can drastically reduce the service life of a device. Acyclically written parameters are
written to voltage-resistant memory modules (EEPROM, Flash etc.). These memory modules are
designed for a limited number of write operations. In normal operation without MS1AC (during
parameter configuration), the number of write operations does not even come close to this
number. If programming is incorrect, this maximum number can be reached quickly, drastically
reducing a device's service life.
!
Note!
The memory module of the device is designed for one million writes.