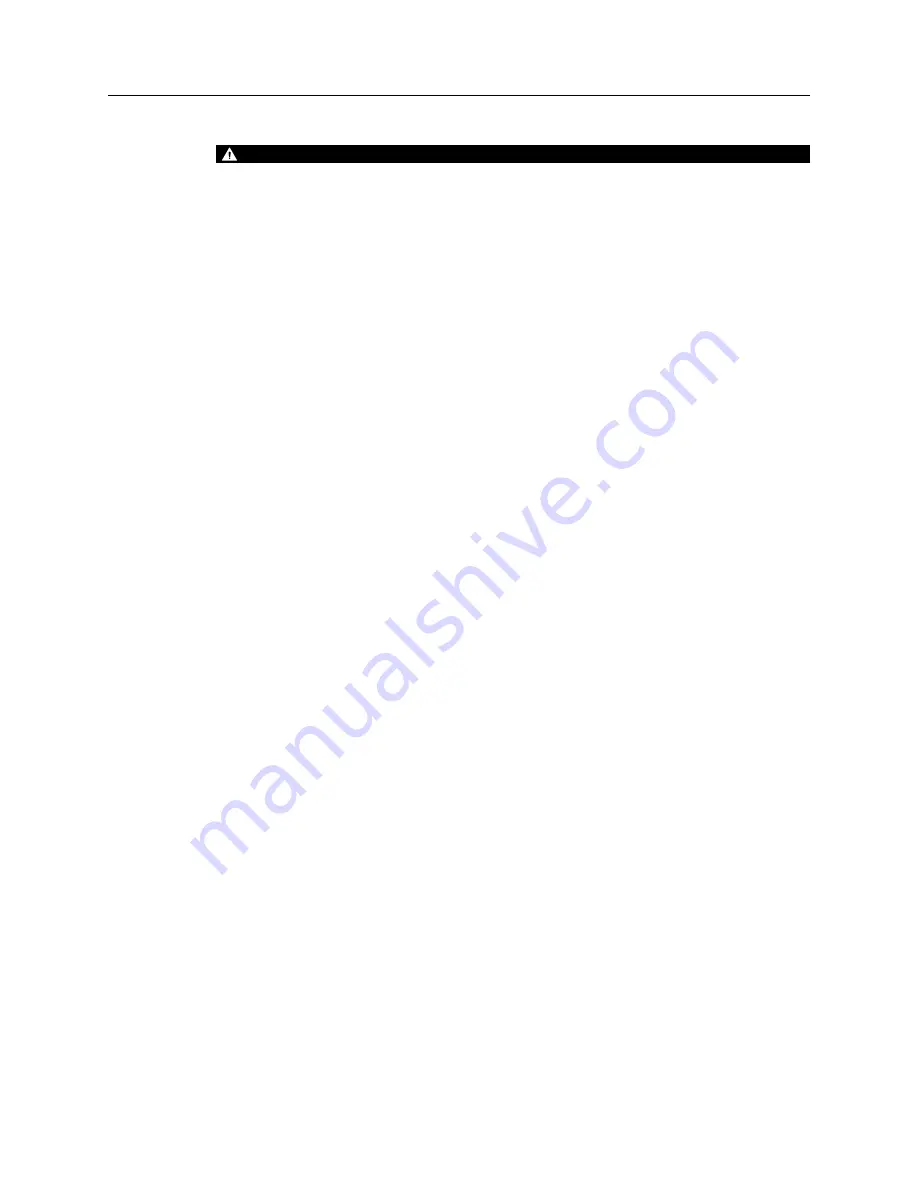
Section 3: Product Description
January 2017
ERNG-X
dopsm2107x012
Section 3: Product Description
6
CAUtioN
Proper Component Selection
1 . Consider the total system design when selecting a component for use in a system .
2 . The user is responsible for assuring all safety and warning requirements of the
application are met through his/her own analysis and testing .
3 . Component function, adequate ratings, proper installation, operation and maintenance
are the responsibilities of the system user .
Section 3: Product Description
The ERNG-X is an accurate and reliable way of controlling natural gas . The product includes a
pressure regulator, preconditioning filters and an electro pneumatic controller for automated
control . The product is panel mounted and can be easily installed in an enclosure or on a wall .
The ERNG-X is a unique and flexible electropneumatic, closed loop, PID controller . The included
ERTune software program provides an easy means of setup, tuning and data acquisition .
3.1 Features
3 .1 .1
Accurate Pressure Control
—
Eliminates droop within the flowing capacity of the pipeline regulator
—
Pipeline outlet pressure control is independent of the pipeline inlet pressure
3 .1 .2 Automation
—
Remote set point control from a PC or PLC
3 .1 .3
ERTune™ Program
—
Included with every ERNG-X, provides data acquisition routine
3 .1 .4
Items Included
All ERNG-X include:
—
ER5050FX-1-002 with ERTune program and ER5000 User Manual (DOPMS2080X012)
—
ER Supply Regulator with relief valve and gauges
—
Two preconditioning coalescing filters
3.2
Controlling System Pressure
In a typical application, the control port of the ERNG-X connects to the spring case of the
pipeline pilot regulator . This is shown in Figure 2 . Supply pressure of up to 110 psig / 7 .5 bar,
is provided to the ERNG-X controller by the factory preset supply regulator .
The ERNG-X increases pressure to the spring case of the pipeline pilot regulator by opening
the Pulse Width Modulation (PWM) solenoid valve at the inlet port of the ER5050FX-1-002
and reduces pressure by opening the PWM solenoid valve at the exhaust port of the
ER5050FX-1-002 . The controller, configured in external feedback mode, senses system
pressure through input from a transducer mounted downstream in the process line . The
controller reads the feedback and compares it to the setpoint, which it receives from an
external source or from a profile in its onboard memory . The ERNG-X is factory set to update
every 500 milliseconds and can be adjusted between 25 milliseconds and 2,500 milliseconds
to better suit the application .