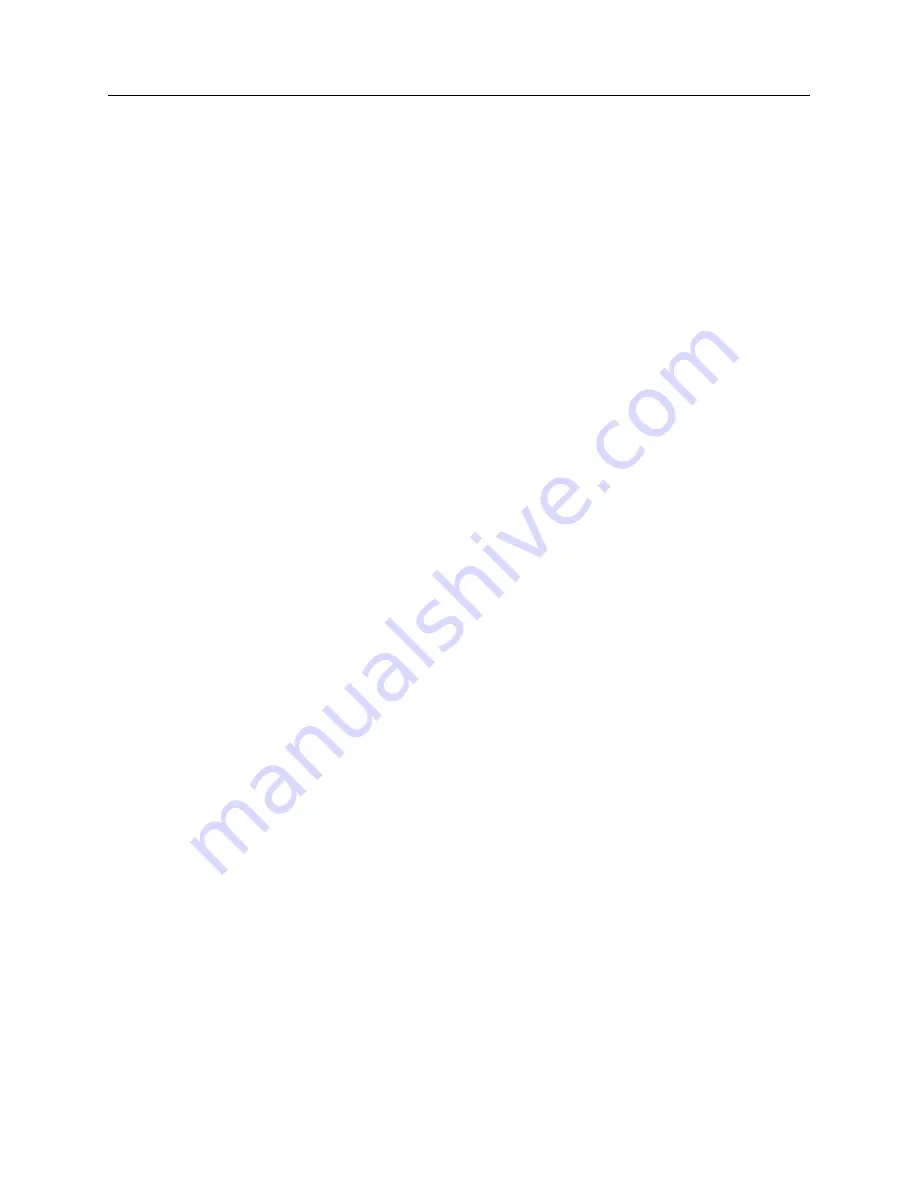
Section 4: Installation
January 2017
ERNG-X
dopsm2107x012
Section 4: Installation
9
4.4 wiring
1 . Refer to ER5000 User Manual for wiring information .
4.5 Communication
The ER5000 communicates using a USB or RS485 interface . The required USB driver is
provided on the ER5000 User Support Software and Manual CD or online . An RS485
communications link can be established between the ER5000 and a PC using either a USB to
RS485 or RS232 to RS485 converter . RS485 communication must be used for daisy-chaining
two or more (up to 32) ER5000s on the same network . RS485 is recommended for
ERNG-X communication . USB is not recommended for hazardous locations and is also not
recommended for distances greater than 10 ft .
4.6
System Leak Check
After installation of all components and wiring:
•
Switch on the ER5050FX-1-002’s power supply .
•
Set the controller output pressure to a safe value . Slowly apply ER5050FX-1-002
supply pressure .
Note: ER Supply Regulator is preset from the factory to 110 psig / 7 .5 bar and may be
adjusted to better suit application . The ER5050FX-1-002 inlet port should not exceed
110 psig / 7 .5 bar .
•
Check all fittings for tightness using leak test fluid . No bubbles should be seen .
Note: Due to the increased volume of the spring case on the pipeline pilot regulator, the
ER5050FX-1-002 automatic solenoid leak test should not be used .
4.7
ERNG-X Tuning
•
When tuning, use conditions similar to the final application (i .e . similar pressures, flow
and medium) . A tuning procedure is provided in the ER5000 User Manual . There is also
“Help” available in the ERTune™ program itself, available on the “Diagnostic Tools” tab
in the ERTune program by clicking the “Tuning Tips” button .
•
The ERNG-X is factory set to tuning parameters for the application shown in Figure 2 .
The update rate is slowed down from 25 milliseconds to 500 milliseconds to allow
for better stability in the system and to allow for the response of the ER controller to
be translated downstream to the external pressure or flow transducer before making
another set-point change . There are also control limits placed on the Analog Set Point
and External Sensor in case of lost communication and/or power . Both the Analog
Set Point and External Sensor are preset to a minimum of -1% with a condition of Inlet
Closed and Exhaust Closed . If the application does not use a 4-20 mA Analog Set Point
and/or a 4-20 mA External Sense Transducer, these control limits must be changed . To
better suit all applications, the tuning parameters and control features may need to be
modified . Refer to ER5000 User Manual for more details .