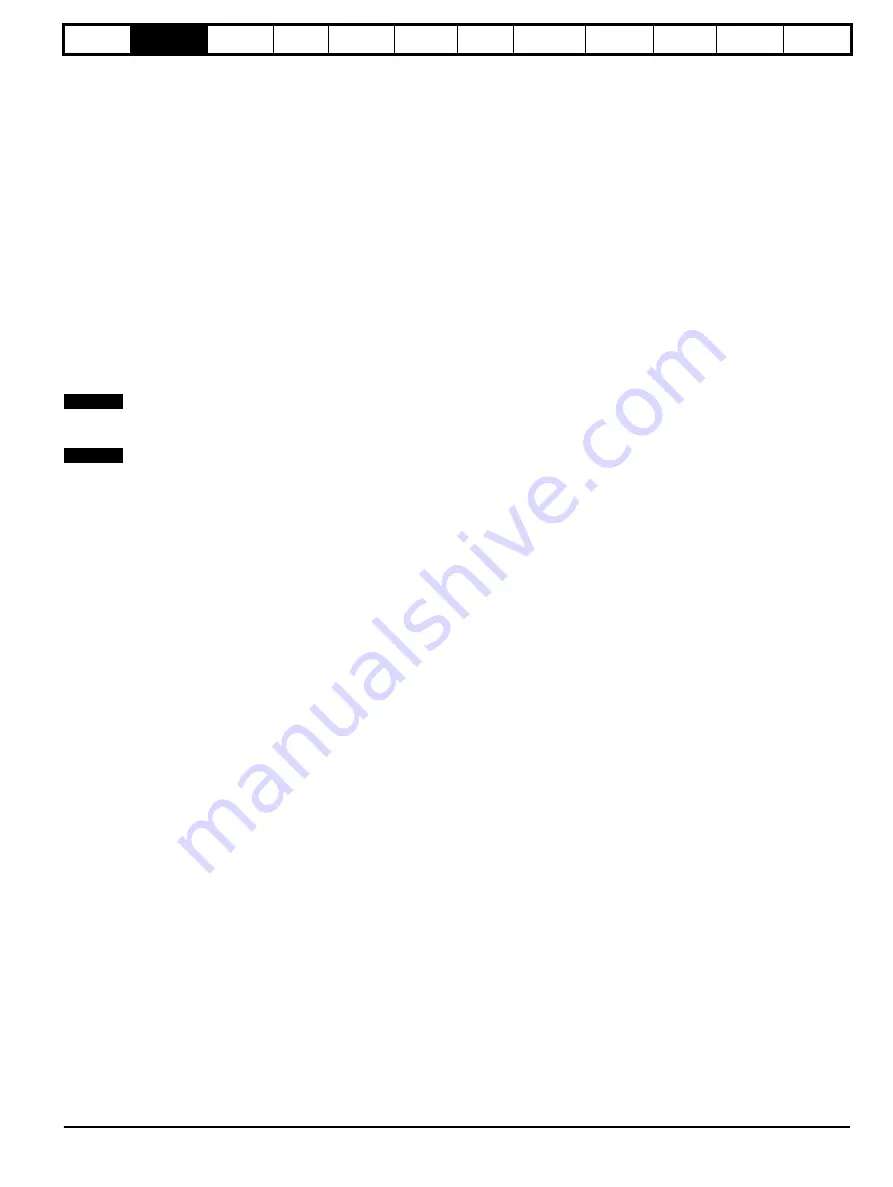
Safety
Information
Introduction
Product
information
System
design
Mechanical
installation
Electrical
installation
Getting
started
Optimisation
Parameters
Technical
data
Component
sizing
Diagnostics
Unidrive SP Regen Installation Guide
7
Issue Number: 2 www.controltechniques.com
2 Introduction
The following installation guide should be read in conjunction with the
Unidrive SP User Guide
.
Any Unidrive SP drive can be configured as an AC Regenerative Unit
(hereafter referred to as a Regen drive).
This guide covers the following:
•
Principles and advantages of operation in regen mode
•
Safety information
•
EMC information
•
Detailed information on additional components required
•
System design
•
Special considerations
•
Installation
•
Commissioning and optimisation of the completed system
At least two Unidrive SP drives are required to form a complete
regenerative system - one connected to the supply and the second one
connected to the motor. A Unidrive SP in regen mode converts the AC
mains supply to a controlled DC voltage, which is then fed into another
drive(s) to control a motor(s).
The motoring drive(s) in a regen configuration could be another drive
other than a Unidrive SP, e.g. Unidrive classic or Commander SK etc.
The following regen components are also required in addition to the
Unidrive SP drives.
1. Regen inductor
2. Switching frequency filter inductor
3. Switching frequency filter capacitor
4. Softstart resistor
5. Varistors
6. MCBs
7. Overload relays
2.1 Regen operation
For use as a regenerative front end for four quadrant operation.
Regen operation allows bi-directional power flow to and from the AC
supply. This provides far greater efficiency levels in applications which
would otherwise dissipate large amounts of energy in the form of heat in
a braking resistor.
The harmonic content of the input current is negligible due to the
sinusoidal nature of the waveform when compared to a conventional
bridge rectifier or thyristor front end.
2.2 Advantages of Unidrive SP operating
in regen mode
The main advantages of an AC Regen system are:
•
Energy saving
•
The input current waveform is sinusoidal
•
The input current has a near unity power factor
•
Power factor correction can be implemented using Pr
4.08
•
The output voltage for the motor can be higher than the available AC
mains supply.
•
The Regen drive will synchronise to any frequency between 30 and
100Hz, provided the supply voltage is within the supply requirements
(operating frequency range of 48Hz to 65Hz)
•
Under conditions of AC mains instability, a Unidrive SP Regen
system can continue to operate down to approximately 75Vac (200V
product) 150Vac (400V product) 225Vac (575V and 690V product)
supply voltage without any effect on the DC bus voltage and hence
on the operation of the motoring drives (increased current will be
taken from the AC supply during this condition to compensate up to
the current limit of the Regen drive)
•
Transient operation is possible between 40 and 72Hz down to the
above supply voltage levels for approximately 1 second.
•
The Regen and motoring drives are identical (when using Unidrive
SP).
•
Power feed-forward term available, using analogue I/O set-up
•
A fast transient response is possible using the power feed forward
term.
2.3 Principles of operation
The input stage of a non-regenerative AC drive is usually an
uncontrolled diode rectifier, therefore power cannot be fed back onto the
AC mains supply. By replacing the diode input rectifier with a voltage
source PWM input converter (Unidrive SP), AC supply power flow can
be bi-directional with full control over the input current waveform and
power factor. Currents can now be controlled to give near unity power
factor and a low level of line frequency harmonics.
In the case of a Unidrive SP operating in regenerative mode, the IGBT
stage is used as a sinusoidal rectifier converting the AC supply to a
controlled DC voltage.
Furthermore, by maintaining the DC bus voltage above the peak supply
voltage the load motor can be operated at a higher speed without field
weakening. Alternatively, the higher output voltage available can be
exploited by using a motor with a rated voltage higher than the AC mains
supply, thus reducing the current for a given power.
Regen inductors must be used to ensure a minimum source impedance,
these being selected and specified later in the guide.
The difference between the PWM line voltage and the supply voltage
occurs across the regen inductors at the Regen drive. This voltage has a
high frequency component, which is blocked by the regen inductor, and
a sinusoidal component at line frequency. As a result currents flowing in
these inductors are sinusoidal with a small high frequency ripple
component.
NOTE
NOTE
Содержание SP1201
Страница 219: ......
Страница 220: ...0471 0029 02 ...