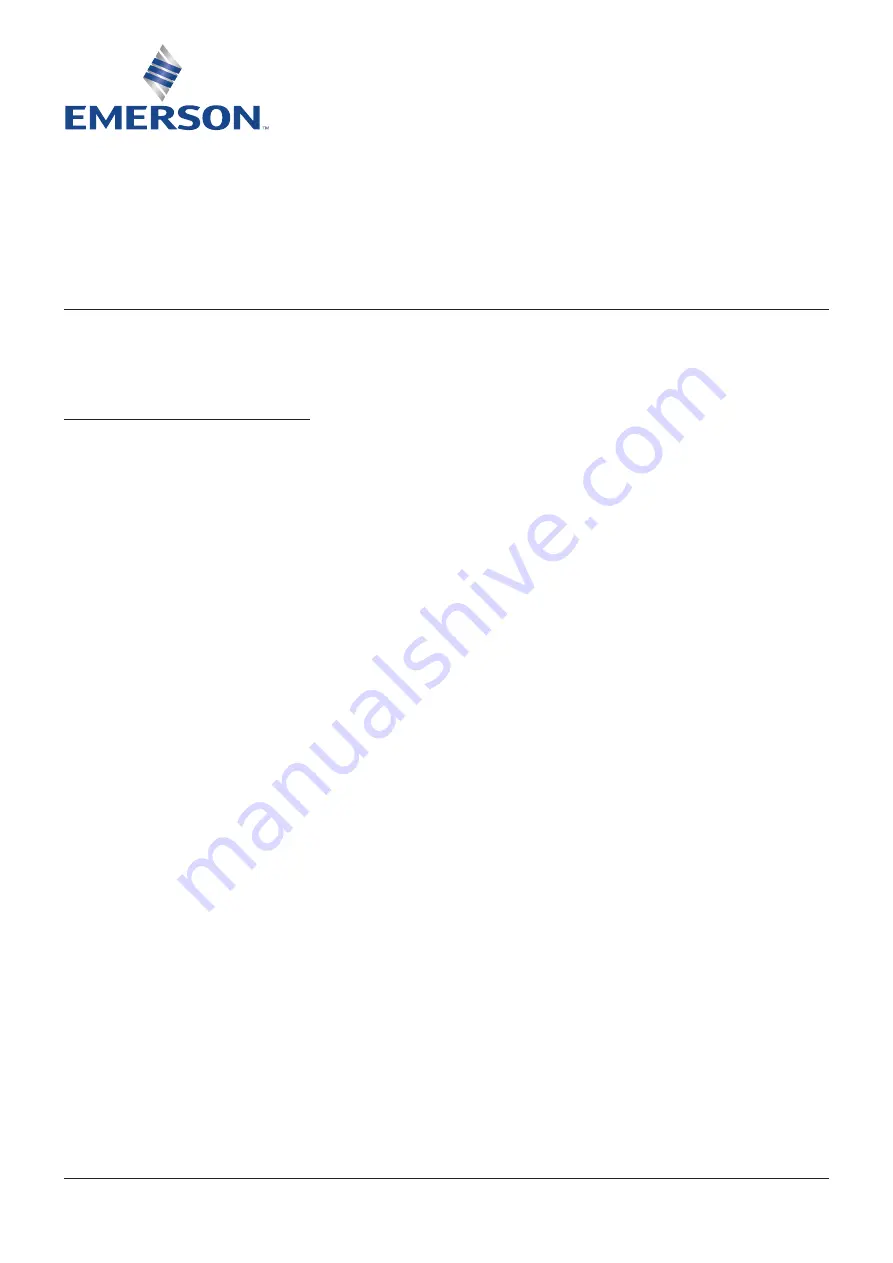
Sempell
SerieS STe 4 ConTrol DeviCe for SafeTy valveS
Operating instructiOns
Before installation these instructions must be fully read and understood
1 Danger anD Warning inDicationS
The construction of the Sempell safety
valves and control devices corresponds to
the standard technology and the valid safety
regulations.
nevertheless, improper use or improper
installation may cause risks for personnel
or can lead to restrictions in regard of the
operational safety. Therefore Sempell GmbH
recommends the operator of the valves to take
appropriate measures and make sure that
the present operating instruction is read and
understood by the assigned personnel.
please observe the following points besides
the notes given in the text
• Danger of burning when in contact with safety
valves and connecting pipes while operating
at increased temperature.
• Disassembly of the safety valve only in case
of pressureless system and after cooling
down. Wait for official permission. Disconnect
electrical supply.
• Protection against risks caused by
evaporation also in case of pressureless
system; for information please contact the
responsible safety inspector.
• After assembly check all sealing points in
regard of tightness.
• Carry ear protection during adjustment,
if necessary.
• Danger of burning by discharge of small
amounts of possibly hot medium in case
of safety valves with open spring bonnet
(type So..., vSe 1, vSr 1, vSe 8).
• Danger of injury while discharging in case of
open discharge line.
• Extreme vibrations (chatter) can lead to an
inadmissible increase of operating pressure
with possibly destruction of the safety valve
or to destruction of the balanced bellows with
unintentional escape of medium.
Application limits
It is only allowed to use the safety valves and the
control device according to the details of this
operating instruction and/or according to the
parameters and application data agreed in the
delivery contract (see nameplate).
The application of the valve has to take place
adequate to the medium tolerances of the used
materials.
Warnings for the operating and maintenance
personnel
Before commissioning and maintenance works
familiarise yourself with the legal accident
prevention regulations, the local safety
instructions and this operating instruction and
observe them.
Use safety valve, control device and their
individual parts and accessories only for the
purpose intended by us.
Work on the electrical systems or equipment
must only be carried out by an electrician
or instructed personnel under control and
supervision of an electrician according to the
electrotechnical regulations.
exclusion of liability
Sempell GmbH cannot be held liable in case
of improper maintenance and adjustment of
a Sempell valve, use of inadmissible spare
parts or utilities and in case of temporary or
permanent connection of equipment with the
safety valve which is not approved by us.
Vciom-02238-en 15/01
Ma.330.02.0505.e
Series
STE 4 Control device for safety valves with
pneumatic actuator.
www.valves.emerson.com
© 2017 Emerson. All rights reserved.