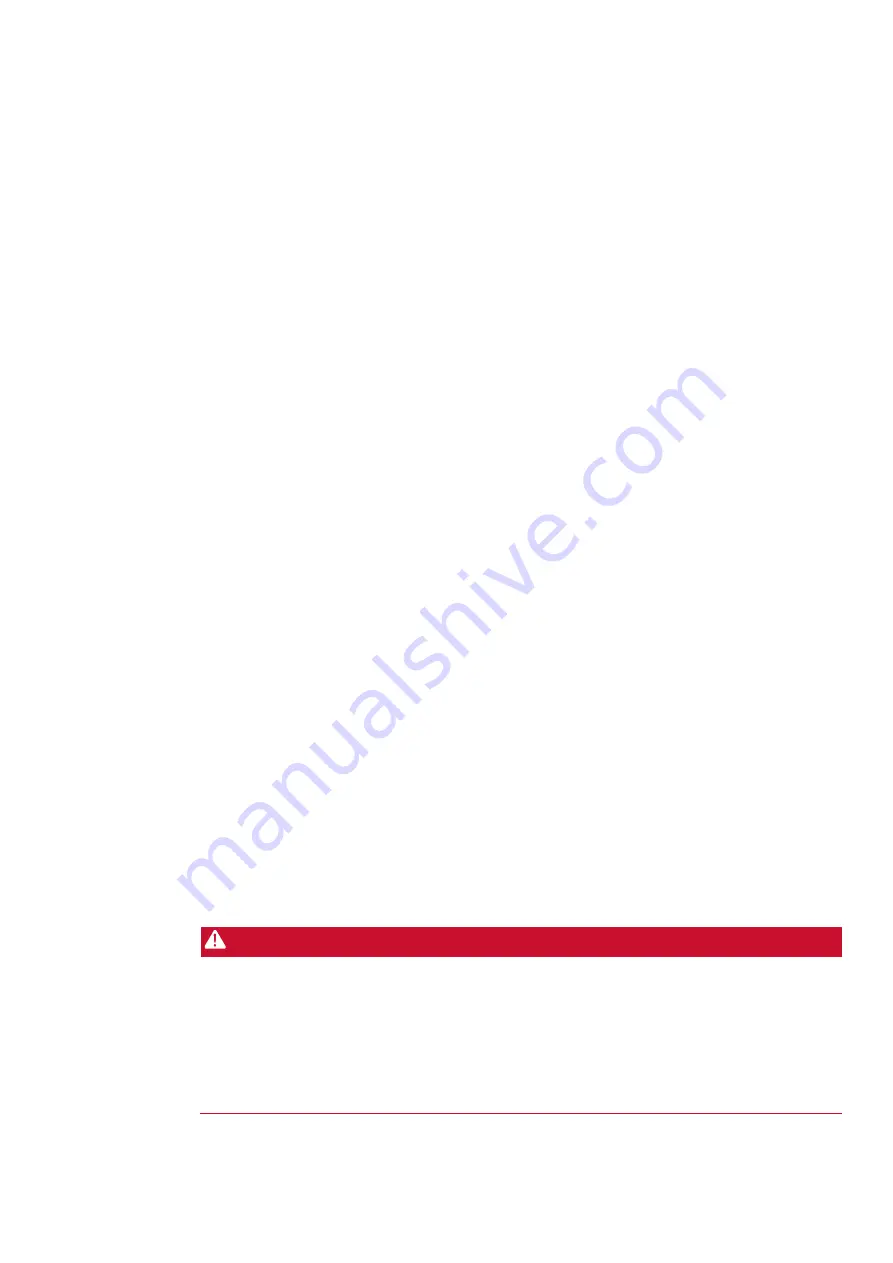
PACMotion™ PSD Installation and User Manual
Section 5
GFK-3168A
September 2020
Mechanical Installation
53
5.5
Guide to electrical installation
Install the drive electrical system as follows:
1.
Select cables in accordance with IEC 60204 (
2.
Install shielding and ground the drive.
For EMC-compliant shielding and grounding, see (
Ground the mounting plate, motor housing and CNC-GND of the control system.
3.
Wire the drive and connectors.
Observe the "Recommendations for EMI noise reduction": (
•
Wire the FAULT contact in series into the emergency off circuit of the system. Connect the
digital control inputs and outputs.
•
Connect up analog ground (also if fieldbuses are used). Connect the analog input source, if
required.
•
Connect the feedback device. Connect the hardware option. Connect the motor cable
•
Connect shielding at both ends. Use a motor choke if cable > 25m. Connect motor-holding
brake, connect shielding at both ends.
•
If required, connect the external regen resistor (with fusing).
•
Connect the auxiliary supply (maximum permissible voltage values see electrical data (
•
Connect the mains filter with IC830DPzzz06 (shielded lines between filter and drive).
Connect the main electrical supply.
•
Check maximum permitted voltage value (
•
Check proper use of residual-current circuit breakers (RCD): (
# 172) for setting up the drive.
4.
Check the wiring against the wiring diagrams.
5.6
Wiring
The installation procedure is described as an example. A different procedure may be appropriate or
necessary, depending on the application of the equipment. Emerson can provide training courses
for this procedure upon request.
DANGER
High electrical voltage up to 900 V!
There is a danger of serious personal injury or death by electrical shock or electrical arcing. Only
install and wire the equipment when it is not live, that is, when neither the electrical supply nor the
24 V auxiliary voltage nor the supply voltages of any other connected equipment is switched on.
Make sure that the cabinet is safely disconnected (for instance, with a lock-out and warning signs).
The individual voltages are switched on for the first time during setup.
Note: Only professional staff who are qualified in electrical engineering are allowed to install the
drive. Wires with color green with one or more yellow stripes must not be used other than for