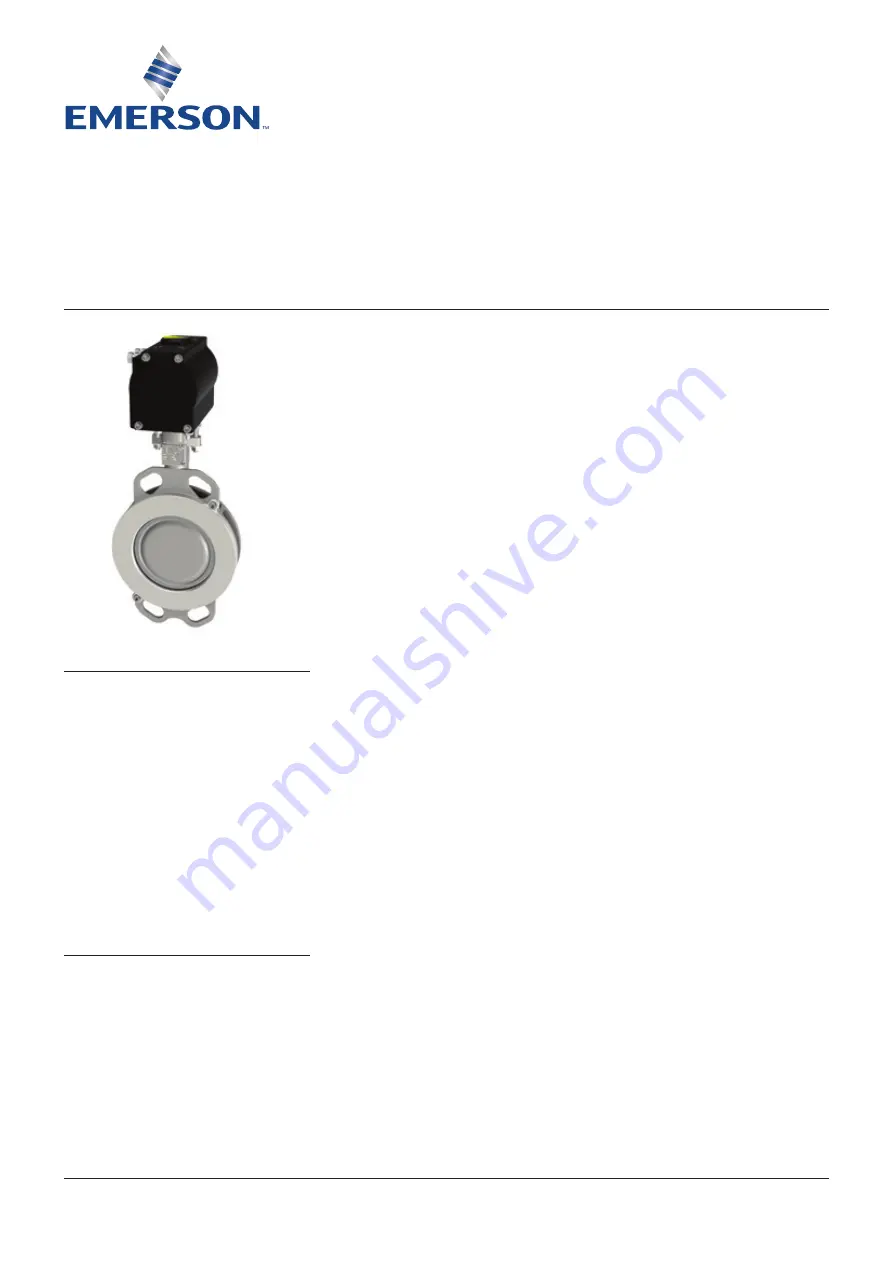
IMPORTANT
Whenever possible, install the valve with the shaft
in the horizontal position and, if possible, with the
cast-in disc stop located top-side of the pipe. If the
shaft cannot be positioned horizontally, position
the shaft so that it is not on the vertical centerline
in a horizontal pipe run. This will minimize any
depositing of solid particles present in the fluid
into the lower bearing.
CAUTION
The valve should be installed in the closed
position to ensure that the seat and disc are
not damaged during installation. Particular
care should be taken with valves equipped with
‘fail open’ actuators. Failure to ensure proper
handling may result in damage to the valve.
If the pipe is lined, confirm that the disc rotation
does not contact the lining during the opening
stroke. Failure to confirm that the disc rotation
does not contact the lining may result in damage
to the valve.
Emerson.com/FinalControl
KEYSTONE
K-LOK SERIES H HIGH PERFORMANCE BUTTERFLY VALVES
INSTALLATION, OPERATION AND MAINTENANCE INSTRUCTIONS
INSPECTION
1. Carefully remove the valve from the
shipping package (box or pallet) to avoid
any damage to the valve and, in the
case of automated valves, to the electric
or pneumatic/hydraulic actuator or
instrumentation.
GENERAL
Suggested installation orientation is with
valve shaft horizontal or inclined from vertical.
Unless otherwise recommended by Emerson,
mount the valve in the preferred direction with
the directional arrow pointing to the lower
pressure side so that the front face of the disc
will be upstream when the valve is in the closed
position.
Thermal insulation of the body is mandatory for
operating temperatures above 200°C (392°F).
H-series K-LOK offers the following body
styles:
Series H1W and H2W - Wafer
Series H1L and H2L - Lugged
Before installation these instructions must be read fully and understood
© 2017 Emerson. All Rights Reserved.
VCIOM-03381-EN 17/11
2. Prior to installation, clean the inside of
the valve. Ensure that there are no solid
objects such as pieces of wood, plastic or
packing materials within the valve or on
the valve seat.
3 Inspect the seat and disc edge to ensure
that they were not damaged in handling.
This is especially important in the case of
valves with ‘fail-open’ actuators.
4. Confirm that the materials of construction
listed on the valve nameplate are
appropriate for the service intended and
are as specified.
5. Locate the directional arrow on the body
that defines the preferred mounting
orientation in respect to the pressure. In
most cases, the valve is properly installed
when the actual fluid flow or high pressure
is acting on the front face of the disc when
the valve is closed.
6. Ensure that the packing gland bolting nuts
are tight.