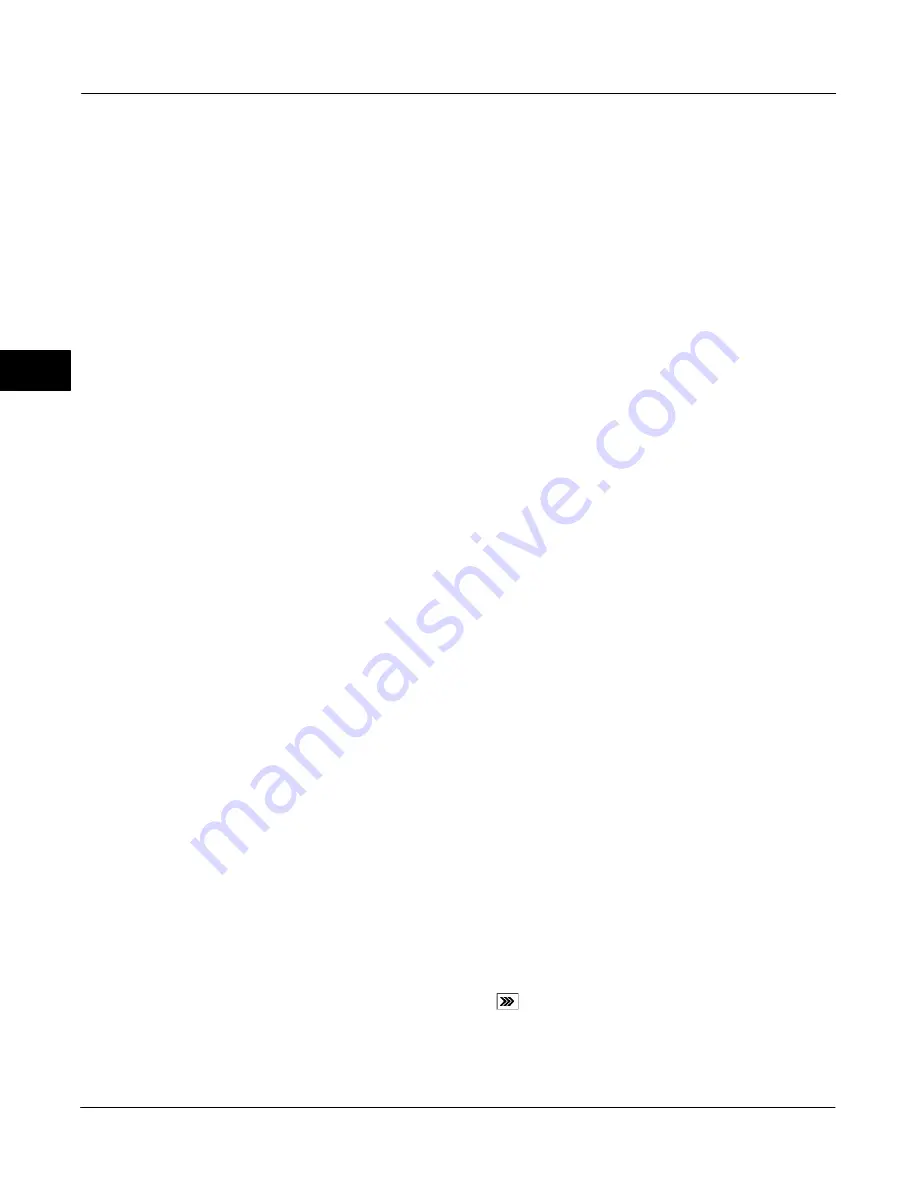
DVC2000 Digital Valve Controller
July 2009
4-4
Control Mode
You can change the control mode by selecting Control
Mode from the Mode menu, or press the Hot Key and
select Control Mode.
Control Mode lets you define where the instrument
receives its set point. Follow the prompts on the Field
Communicator display to choose one of the following
control modes: Analog or Digital.
Choose Analog if the instrument is to receive its set
point over the 4-20 mA loop. Normally the instrument
control mode is Analog.
Choose Digital if the instrument is to receive its set
point digitally, via the HART communications link.
A third mode, Test, is also displayed. Normally the
instrument should not be in the Test mode. The Field
Communicator automatically switches to this mode
whenever it needs to stroke the valve, for example
during calibration or stroke valve. However, if you
abort from a procedure where the instrument is in the
Test mode, it may remain in this mode. To take the
instrument out of the Test mode, select Control Mode
then select either Analog or Digital.
Restart Control Mode
Restart Control Mode (Restart Ctrl Mode) lets you
choose which operating mode you want the instrument
to be in after a restart. Follow the prompts on the Field
Communicator display to define the restart control
mode as Resume Last, Analog, or Digital.
Burst Mode
Enabling burst mode provides continuous
communication from the digital valve controller. Burst
mode applies only to the transmission of burst mode
data (analog input, travel target, pressure, and travel)
and does not affect the way other data is accessed.
Access to information in the instrument is normally
obtained through the poll/response of HART
communication. The 375 Field Communicator or the
control system may request any of the information that
is normally available, even while the instrument is in
burst mode. Between each burst mode transmission
sent by the instrument, a short pause allows the Field
Communicator or control system to initiate a request.
The instrument receives the request, processes the
response message, and then continues “bursting” the
burst mode data.
There are four burst mode commands. Command 3 is
recommended for use with the Rosemount
333
HART Tri-Loop
HART-to-analog signal converter.
The other three are not used at this time.
Command 3 provides the following variables:
Primary variable—analog input in % or mA,
Secondary variable—travel target (valve set
point) in % of ranged travel,
Tertiary variable—output pressure in psig, bar, or
kPa,
Quaternary variable—travel in % of ranged
travel.
To enable burst mode, from the Online menu, select
Setup & Diag, Detailed Setup, Mode, Burst, and Burst
Enable. To send a burst mode command, select Setup
& Diag, Detailed Setup, Mode, Burst, and Burst
Command. Burst mode must be enabled before you
can change the burst mode command.
Restarting the Instrument
Restart resets the instrument in the same manner as
when power to the instrument is interrupted. When
Restart is issued, all of the newly entered configuration
variables become active. Otherwise, they may not
take effect until the instrument is placed In Service.
Setting Protection
Some setup parameters may require changing the
protection with the Field Communicator.
Two levels of protection are available:
Config & Calib—Both setup and calibration are
protected. Prohibits changing calibration and protected
setup parameters.
None—Neither setup nor calibration is protected.
Allows changing calibration and setup parameters.
Table 4-2 lists configurable parameters in the
instrument and the requirements for modifying these
parameters, in terms of instrument mode and
protection.
To change an instrument’s protection, press the Hot
key
on the Field Communicator display window
and select Protection or select Protection from the
Detailed Setup menu. Select the desired level of
protection. Follow the prompts on the Field
Communicator display to set the protection level.
4
Содержание Fisher FIELDVUE DVC2000
Страница 40: ...DVC2000 Digital Valve Controller July 2009 3 14 3 ...
Страница 70: ...DVC2000 Digital Valve Controller July 2009 6 10 6 ...
Страница 71: ...Parts July 2009 7 1 7 7 Section 7 Parts Parts Ordering 7 2 Parts Kits 7 2 Parts List 7 2 7 ...
Страница 77: ...Principle of Operation July 2009 A 1 A A Appendix A Principle of Operation DVC2000 Operation A 2 A ...
Страница 80: ...DVC2000 Digital Valve Controller July 2009 A 4 A ...
Страница 104: ...DVC2000 Digital Valve Controller July 2009 Index 8 C Index ...
Страница 105: ......