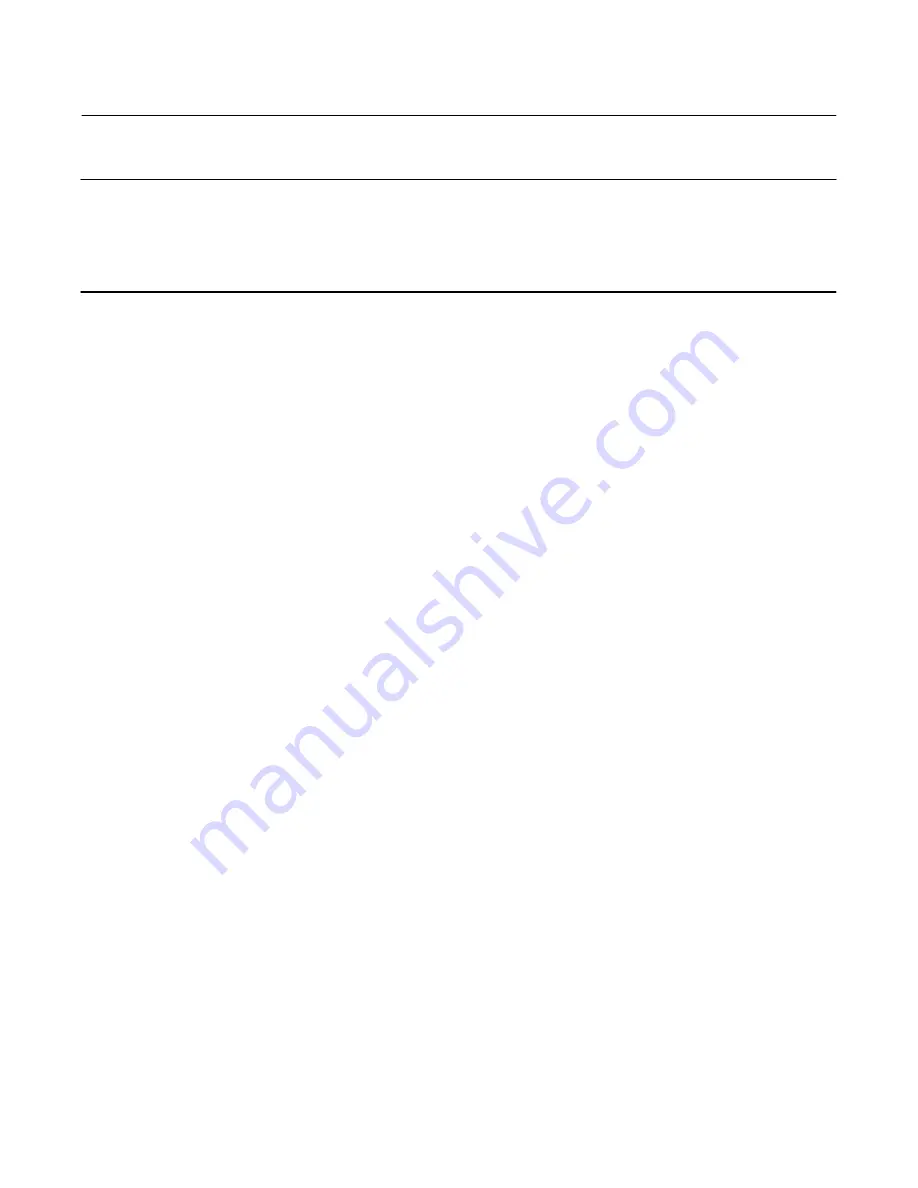
Instruction Manual
D103292X012
C1 Controllers and Transmitters
March 2017
31
Note
Key 2 is used as both a supply gauge and an output gauge on units without a process pressure gauge. A quantity of 2 is required for
these units. On units with a process pressure indicator gauge (key 4), key 2 is used for the output gauge. A quantity of 1 is required
for these units.
Use key 3 for supply pressure indication when a process pressure gauge is installed. Key 3 installs on the supply pressure regulator.
1. Shut off the supply pressure and process lines to the controller or transmitter.
2. Remove the gauge to be replaced:
D
Unscrew the output or supply gauge (key 2) from the relay base.
D
Unscrew the process pressure gauge (key 4) from the process connection (key 14).
D
Unscrew the supply gauge (key 3) from the supply pressure regulator.
3. Coat the threads of the replacement gauge with a sealant.
4. Screw the replacement gauge into the relay base, process connection, or supply pressure regulator.
5. Check for leaks by applying the correct supply pressure with the nozzle capped to produce full output pressure.
Replacing Bourdon Tube
Refer to figure 24 for key number locations unless otherwise directed.
1. Shut off the supply pressure and process lines to the controller or transmitter.
2. Unscrew the machine screw (key 56) to disconnect the link (key 16) and bearing (key 31) from the beam (key 39).
Be careful to avoid losing the bearing (key 31). Washer(s) (key 62) for the machine screw (key 56) are at times
furnished for insertion at the beam (key 39) connection to ensure alignment of the connecting link (key 16).
remove the Bourdon tube (key 5).
4. Unscrew the machine screw (key 56), and remove the link and bearing (keys 16 and 31) from the Bourdon tube. Be
careful to avoid losing the bearing.
5. Attach the link and bearing to the replacement Bourdon tube.
6. Attach the Bourdon tube with two machine screws and washers (keys 55 and 45).
7. Connect the link and bearing to the beam (key 39).
8. After connecting the link to the beam, make sure that the link is parallel to the sensing element (key 5) and the
beam (key 39) so that it does not bind against the sensing element of the beam. Figure 15 shows a properly aligned
connecting link; the connecting link is not in contact with the Bourdon tube or or washers. When properly
configured, the connecting link moves freely when touched. Washers (key 62) are used as shims to set parallelism.
9. Check to be sure that the beam is parallel with the bottom of the case and that the link (key 16) is in tension. If the
beam is not parallel with the case, loosen the machine screws (key 55), reposition the Bourdon tube to get the
beam parallel, and retighten the screws.
10. If a Bourdon tube with a different range was installed, remove the machine screw and washer (keys 61 and 60) and
dial (key 6). Install a new dial having an adjustment range corresponding to the range of the Bourdon tube. If an
optional process pressure gauge (key 4, figure 22) is being used, install a new gauge with the appropriate
measurement capability.