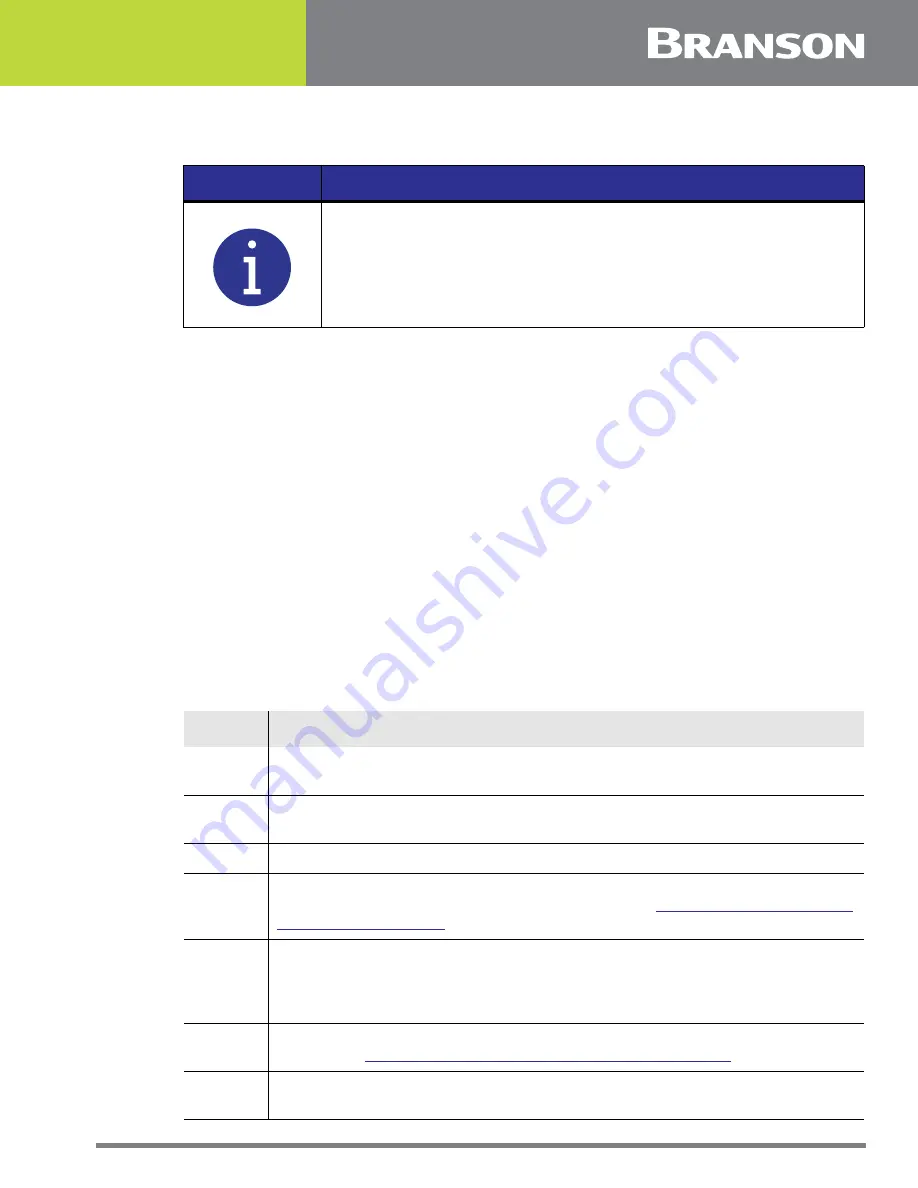
100-412-183 REV. 13
115
8.2.2
Recondition the Stack (Converter, Booster, and Horn)
Welding system components work most efficiently when the converter-booster-horn stack
mating surfaces are flat, in solid contact, and free from fretting corrosion. Poor contact
between mating surfaces wastes power output, makes tuning difficult, increases noise and
heat, and may cause damage to the converter.
For standard 20 kHz and 30 kHz products, a Branson Mylar polyester film washer should
be installed between the horn and booster, and horn and converter. Replace the washer if
torn or perforated. Stacks using Mylar plastic film washers should be inspected every
three months.
Stacks used with silicone grease, as with certain 20 kHz, 30 kHz and all 40 kHz products,
should be periodically reconditioned to eliminate fretting corrosion. A stack using silicone
grease should be inspected every two weeks for corrosion. When experience is gained for
specific stacks, the inspection interval can be adjusted to a longer or shorter period as
required.
Stack Reconditioning Procedure
To recondition stack mating surfaces, take the following steps:
NOTICE
Never clean the converter-booster-horn stack mating surfaces by
using a buffing wheel or by filing.
Table 8.1
Stack Reconditioning Procedure
Step
Action
1
Disassemble the converter-booster-horn stack and wipe the mating surfaces
with a clean cloth or paper towel.
2
Examine all mating surfaces. If any mating surface shows corrosion or a
hard, dark deposit, recondition it.
3
If necessary, remove the threaded stud from the part.
4
Tape a clean sheet of #400 (or finer) grit emery cloth to a clean, smooth,
flat surface (such as a sheet of plate glass), as in
5
Place the interface surface on the emery cloth. Grasp the part at the lower
end, with your thumb over the spanner-wrench hole, and lap the part in a
straight line across the emery cloth. Do not apply downward pressure — the
weight of the part alone provides sufficient pressure.
6
Lap the part, two or three times, in the same direction against the emery
cloth. (See
Figure 8.1 Reconditioning Stack Mating Surfaces
7
Rotate the part 120 degrees, placing your thumb over the spanner-wrench
hole, and repeat the lapping procedure in step 6.
Содержание DCX S
Страница 4: ...iv 100 412 183 REV 13 ...
Страница 14: ...4 100 412 183 REV 13 Figure 1 2 Safety related Labels found on the DCX S Power Supply Vertical ...
Страница 22: ...12 100 412 183 REV 13 ...
Страница 36: ...26 100 412 183 REV 13 ...
Страница 47: ...100 412 183 REV 13 37 4 3 Declaration of Conformity Figure 4 1 Declaration of Conformity ...
Страница 50: ...40 100 412 183 REV 13 ...
Страница 54: ...44 100 412 183 REV 13 Figure 5 1 DCX S Power Supply Benchtop Dimensional Drawing ...
Страница 86: ...76 100 412 183 REV 13 ...
Страница 87: ...100 412 183 REV 13 77 Chapter 6 Converters and Boosters 6 1 Converters and Boosters 78 ...
Страница 120: ...110 100 412 183 REV 13 ...
Страница 137: ...100 412 183 REV 13 127 8 5 Circuit Diagram Figure 8 2 Interconnect Diagram Power Supply ...
Страница 144: ...134 100 412 183 REV 13 ...
Страница 145: ...100 412 183 REV 13 135 Appendix A Timing Diagrams A 1 Timing Diagrams 136 ...
Страница 146: ...136 100 412 183 REV 13 A 1 Timing Diagrams Figure A 1 Weld Cycle Figure A 2 Weld Cycle Figure A 3 Weld Cycle ...
Страница 147: ...100 412 183 REV 13 137 Appendix B Signal Diagrams B 1 Signal Diagrams 138 ...
Страница 154: ...144 100 412 183 REV 13 ...