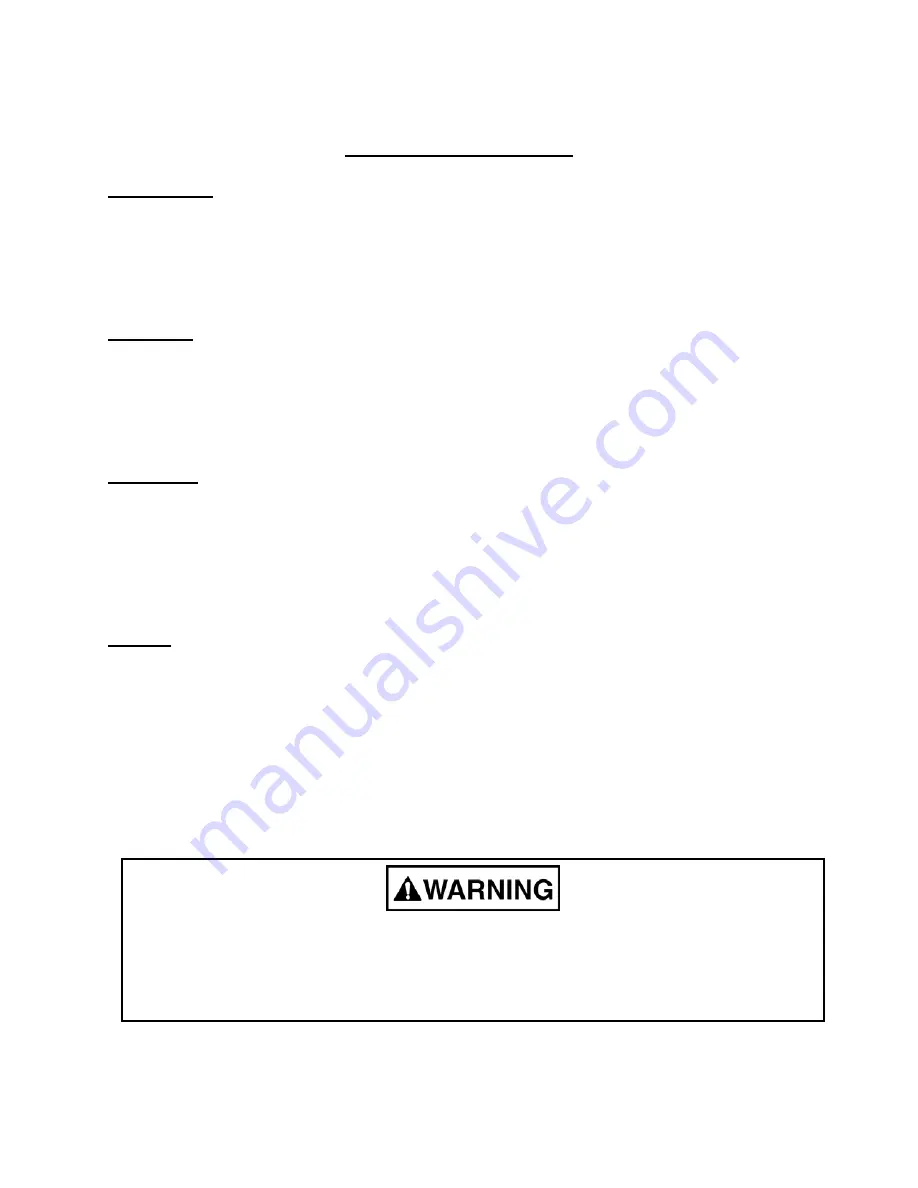
General Information
Introduction
The purpose of this manual is to provide the user with the information needed to
install, start-up, and maintain the Focus 3 drive. This instruction manual should be read
in its entirety, paying special attention to the warning and caution notices, before
installation and before performing any start-up or drive maintenance.
Receiving
The user is responsible for inspecting the equipment thoroughly before accepting
the shipment from the freight company. Check the items received against the purchase
order. If any items are obviously damaged, do not accept delivery until the damage has
been noted on the freight paperwork.
Inspection
Before installation and start-up of the drive, inspect the unit for mechanical integrity
(i.e. loose parts, wires, etc). If physical damage was sustained during shipment, leave
the shipping container intact and notify the freight agent. After unpacking, check the
drive nameplate catalog number against the purchase order. See page 10 for
nameplate location.
Storing
Store the drive in its shipping container prior to installation. If the drive isn’t used
for a period of time, store according to the following instructions in order to maintain
warranty coverage:
Clean, dry location
Ambient Temperature Range: -40
0
C to 70
0
C
Humidity: 95%, Non-condensing
Improper procedures can result in personal injury or equipment damage. Only
qualified electrical maintenance technicians familiar with electronic drives and their
standard safety precautions should be permitted to install, start-up, or maintain this
apparatus.
Page 8
Содержание Control Techniques Focus 3N
Страница 7: ...Page vii ...
Страница 52: ...Page 46 Tuning Adjus Optional tments Current Ref Gain Speed Ref Gain Zero Bias ...
Страница 53: ...Page 47 ...
Страница 54: ...Page 48 ...
Страница 74: ......