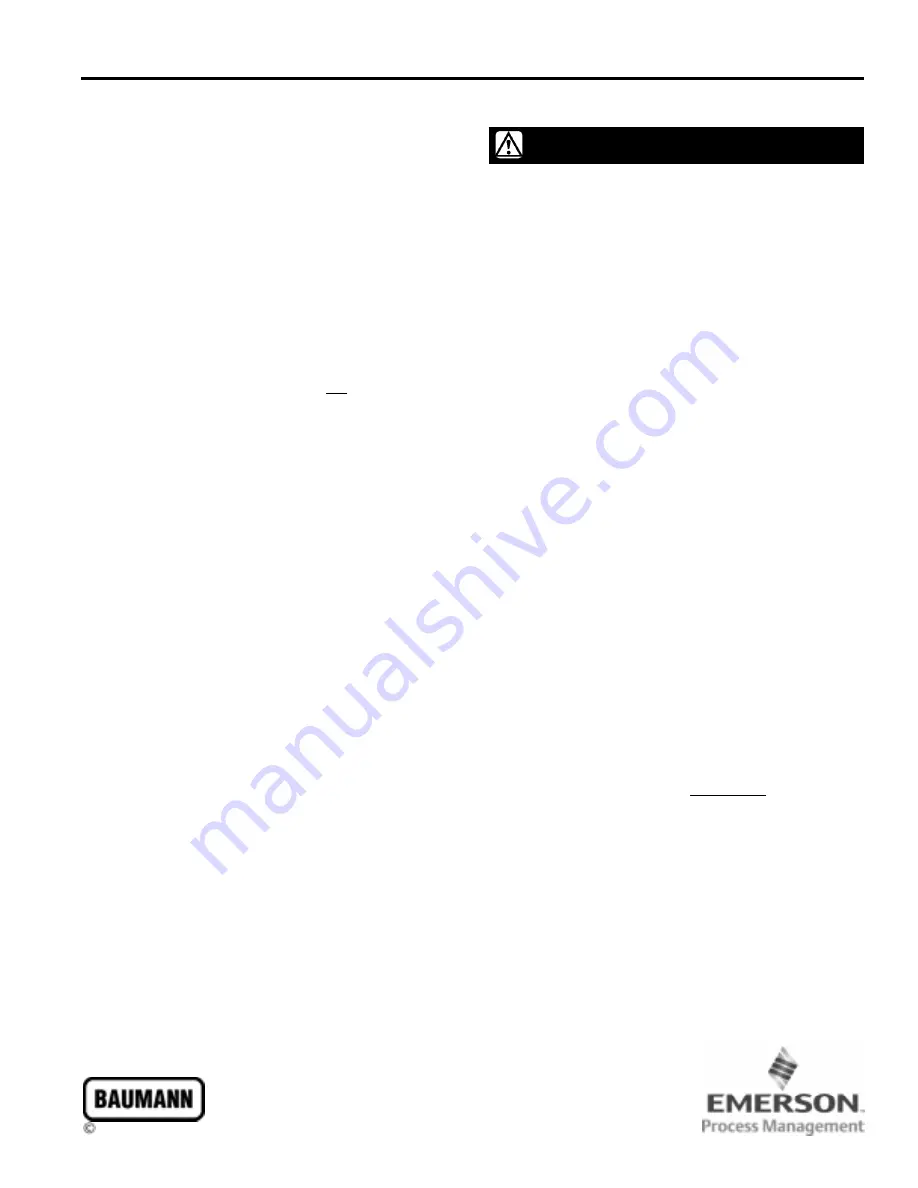
PRELIMINARY STEPS
Before installation, note the flow direction arrow on the valve
body. The flow should enter the valve on the concave side
of the vane. That is, the side having the exposed shaft.
All valve bodies are rated Class 300 and installs between
ANSI Class 150 and 300 or DIN PN 10 and 25 line flanges.
However, make sure that the vane (2) is in the open position
after installation when the pipe line is hydrostatically tested
since the vane (2) and shaft (3) are not rated for the full
hydrostatic pressure differential.
INSTALLATION
Before installing the valve body between the mating pipe line
flanges, make sure that the vane(2) is in the closed position.
For fail open valves, this can be done by applying 20 psi air
pressure to the actuator (do not exceed 35 psi) or with the top
mounted handwheel (optional). After installation, please back-
off handwheel to allow for full vane operation.
The valve bodies are flangeless and will fit between line
flanges with raised faces of Class 150 or 300 and between
metric flanges of PN 10,16 and 25. Nevertheless, the valve
must be properly aligned with the center of the flange to
avoid interference of the flange bore with the vane. The
vane is purposely kept undersized so that it will swing freely
into a flange bore corresponding to a schedule 80 pipe ID.
1. Install tie rods through lower flange holes to form a cradle
for the valve body. For 4” body or Class 300 flange
mounting, tubular spacers may be placed over lower tie rods
to lift body to center. Next, place gaskets on either side of
valve body and add remaining tie rods. Be sure body is
centered with flanges before tightening all tie rods.
2. Before placing the valve in operation, stroke the valve
through its full travel by applying manually regulated air
pressure to the actuator, or by stroking the valve by means of
a handwheel (if provided).
TEMPERATURE LIMITS
NOTE: The bearings and packing are Teflon lubricated which
limits the operating temperatures to 450
0
F (325
0
F for
stainless steel bodies) unless special materials are
specified.
VALVE BODY MAINTENANCE
BODY DISASSEMBLY
1.
Disconnect air lines from actuator or positioner.
2.
Apply air pressure or use handwheel, if provided, to bring
the actuator stem(35) down (only required for “air-to-open
installations).
3.
Remove 5/16”-24 hex head cap screws(25), washer(26)
and pointer(38) from shaft end(3).
4.
Unscrew hex head cap screw(39) and locknut(29) to
loosen linkages(18 &18a) on shaft(3).
5.
Remove hex nuts(13) and slide packing flange(7) and
packing follower(6) away from valve bonnet.
6.
Remove two (2) hex head cap screws(12) from bracket
(17) and pull complete actuator with bracket(17) from
shaft(3) and away from valve body(1).
NOTE: Orientation of bracket and linkage for reassembly.
REMOVAL OF GUIDE BUSHINGS
1.
Remove packing rings(15), bottom ring(5) and spring (10).
2.
Remove outboard bearing cover assembly(16). (Not
required for 2” valve size.)
3.
Drive out taper pins(14) by placing a 5/32” diameter pin
through drilled holes from the downstream side of the vane
and hit gently with hammer.
4.
Remove shaft(3) and pull out vane(2).
NOTE: Remember orientation of vane for reassembly.
5.
Use an 11/16” diameter or 18 mm diameter metal rod and
push guides(4) towards center opening of the body.
REPLACING PACKING RINGS
1.
Insert compression spring(10) and bottom ring(5) over
shaft(3) and into bonnet.
25000 Series Lo-T
TM
Butterfly Control Valve
Instructions
November 2001
Instruction No. 25.1:IM
WARNING:
For Warnings and Cautions refer to
Supplemental Safety Instruction No. SSI-1
BAUMANN INC., 2001; All Rights Reserved