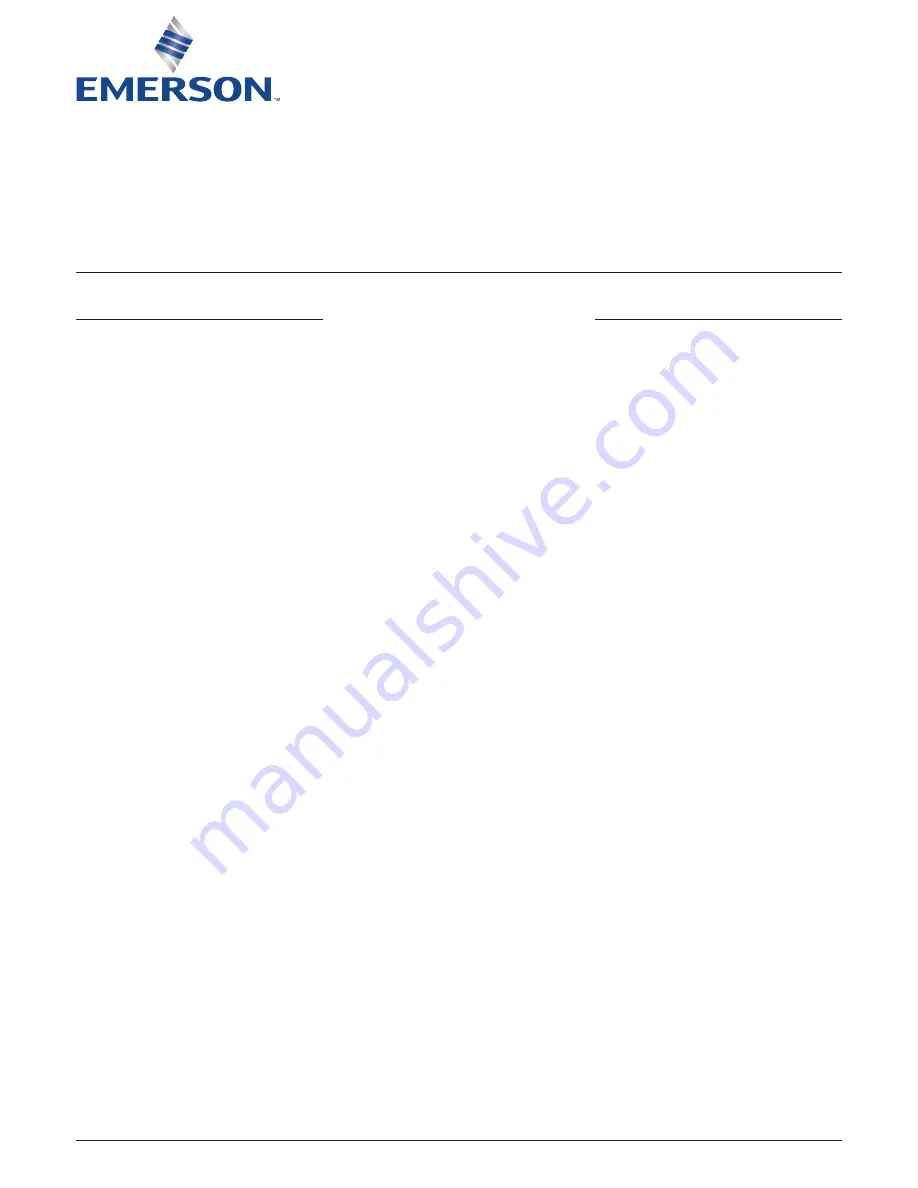
Anderson Greenwood
SerieS 9300 Pilot oPerated Safety relief ValVeS
InstallatIon and MaIntenance InstructIons
Before installation these instructions must be fully read and understood
storAGe And HAndlinG
Pressure/vacuum relief valve performance may
be adversely affected if the valve is stored for
an extended period without proper protection.
rough handling and dirt may damage, deform,
or cause misalignment of valve parts and
may alter the pressure setting and adversely
affect valve performance and seat tightness.
it is recommended that the valve be stored in
the original shipping container in a warehouse
or at a minimum on a dry surface with a
protective covering until installation. inlet and
outlet protectors should remain in place until
the valve is ready to be installed in the system.
tAble of contents
1 introduction .................................................. 2
2 Main valve .................................................... 3
3 Pilot maintenance ...................................... 14
4 functional testing of complete
assembly of main valve and pilot .............. 27
5 Storage and handling ................................ 29
6 trouble shooting ........................................ 30
7 Main valve spare parts and repair kits ..... 30
8 Pilot spare parts and repair kits ............... 31
9 accessories, options, and
accessory repair kit ................................... 32
10 lubricants and sealants for Series 9300.. 32
installation and Maintenance instructions
for anderson Greenwood Series 9300 Pilot
operated Safety relief Valves (PoSrV).
the intent of these instructions is to acquaint
the user with the storage, installation and
operation of this product. Please read these
instructions carefully before installation.
sAfety PrecAutions
When the safety valve is under pressure
never place any part of your body near
the outlet/exhaust of the valve.
The valve outlet and any separate drains should
be piped or vented to a safe location.
Always wear proper safety gear to protect hands,
head, eyes, ears, etc. anytime you are near
pressurized valves.
Never attempt to remove the safety valve from
a system that is pressurized.
Never make adjustments to or perform
maintenance on the safety valve while in service
unless the valve is isolated from the system
pressure. If not properly isolated from the system
pressure, the safety valve may inadvertently open
resulting in serious injury.
Remove the safety valve prior to performing any
pressure testing of the system.
The safety of lives and property often depends on
the proper operation of the safety valve. The valve
must be maintained according to appropriate
instructions and must be periodically tested and
reconditioned to ensure correct function.
VcioM-06024-us 15/01
wArninG
The protection and safety of equipment, property
and personnel depends on the proper operation
of the safety valves described in this manual.
All
Emerson
safety valves should be kept in proper
working condition in accordance with the
manufacturer’s written instructions. Periodic
testing and maintenance by the user of this
equipment is essential for reliable and safe valve
operation.
All installation, maintenance, adjustment,
repair and testing performed on safety valves
should be done by qualified technicians having
the necessary skills and training adequate to
perform such work. All applicable Codes and
Standards, governing regulations and authorities
should be adhered to when performing safety
valve repair. No repair, assembly, adjustment or
testing performed by other than Emerson or its
authorized assemblers and representatives shall
be covered by the warranty extended by Emerson
to its customers. The user should use only original,
factory supplied OEM parts in any maintenance or
repair activity involving this product.
This Maintenance Manual is provided as a general
guide for the repair and maintenance of the safety
valves described herein. It is not possible to
describe all configurations or variations with such
equipment. The user is advised to contact
Emerson
or its authorized assemblers and representatives
for assistance in situations that are not adequately
covered or described in this manual.
Before removing a safety valve for maintenance,
ensure that the system pressure has been fully
depressurized. If an isolation block valve is used
ensure that any trapped fluid between the block
valve and the safety valve is safely vented.
Before disassembling the safety valve ensure that the
valve has been decontaminated from any harmful
gasses or fluids and that it is at a safe temperature
range for handling. Fluids can be trapped in
the dome space of pilot operated safety valves.
Before
installation, the Installation and Operational Safety
Instructions should be fully read and understood.
These Instructions may
be requested from the factory or are available at
www.valves.emerson.com.
engineering doc. #05.9040.275 rev.d
Emerson.com/FinalControl
© 2017 Emerson. All rights reserved.